Download PDF
How E2 SHOP Helped Improve Revenue and Catch Mistakes
Technology Category
- Platform as a Service (PaaS) - Application Development Platforms
Applicable Industries
- Equipment & Machinery
Applicable Functions
- Discrete Manufacturing
Use Cases
- Manufacturing System Automation
Services
- Cloud Planning, Design & Implementation Services
The Challenge
Denver Machine Shop, a family-owned heavy industrial repair and prototype machine shop, was facing challenges in managing their operations due to their paper-based system. The system was inefficient and made it difficult to track jobs, billing, and costs accurately. The company was also concerned about missing out on important details such as the actual time taken to complete a job. As the company grew, it became increasingly difficult to keep track of all the operations. For instance, there were instances where jobs were shipped without being billed, and the company had no way of knowing this without a comprehensive system in place.
About The Customer
Denver Machine Shop is a family-owned business located in Henderson, Colorado. The company specializes in heavy industrial repair and also operates as a prototype machine shop. The business has been in the family since 1916 when Fred White bought out his partner. The company prides itself on being a generational business, not just in terms of ownership, but also in terms of its employees. There are several father-son teams working in the shop, and the company values the continuity this brings to the office and shop floor. The company was looking to grow and realized that their paper-based system was not sufficient to support this growth.
The Solution
In 2007, Scott and Eric, the owners of Denver Machine Shop, decided to implement an ERP system to improve their operations. They chose E2 SHOP, a digital database that would make it easier to find information and quickly check on everything happening in the shop. The software allowed them to compare shipped vs. billed jobs and ensure there were no discrepancies. A few years later, they upgraded to the cloud-hosted version of E2 SHOP. This decision proved beneficial during the COVID-19 pandemic, as it allowed employees to work from home easily. The software has been instrumental in supporting the shop's operations and growth over the years.
Operational Impact
Quantitative Benefit
Related Case Studies.
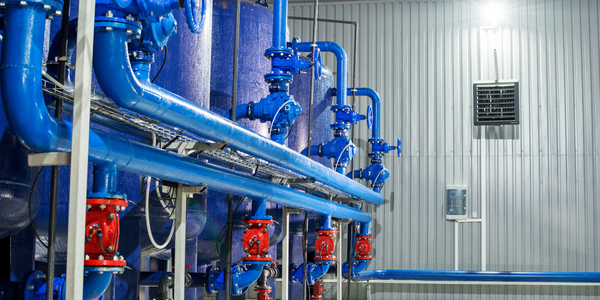
Case Study
Smart Water Filtration Systems
Before working with Ayla Networks, Ozner was already using cloud connectivity to identify and solve water-filtration system malfunctions as well as to monitor filter cartridges for replacements.But, in June 2015, Ozner executives talked with Ayla about how the company might further improve its water systems with IoT technology. They liked what they heard from Ayla, but the executives needed to be sure that Ayla’s Agile IoT Platform provided the security and reliability Ozner required.
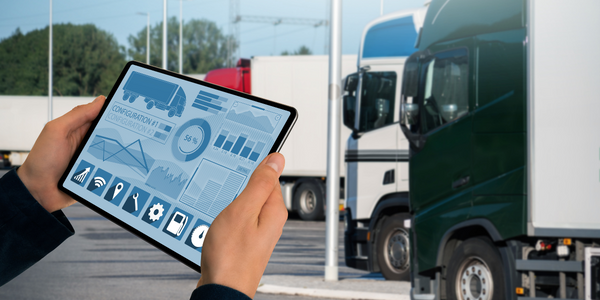
Case Study
IoT enabled Fleet Management with MindSphere
In view of growing competition, Gämmerler had a strong need to remain competitive via process optimization, reliability and gentle handling of printed products, even at highest press speeds. In addition, a digitalization initiative also included developing a key differentiation via data-driven services offers.
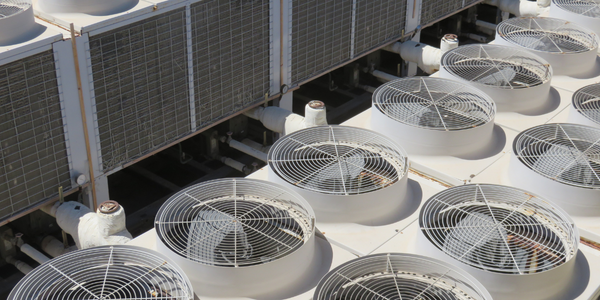
Case Study
Predictive Maintenance for Industrial Chillers
For global leaders in the industrial chiller manufacturing, reliability of the entire production process is of the utmost importance. Chillers are refrigeration systems that produce ice water to provide cooling for a process or industrial application. One of those leaders sought a way to respond to asset performance issues, even before they occur. The intelligence to guarantee maximum reliability of cooling devices is embedded (pre-alarming). A pre-alarming phase means that the cooling device still works, but symptoms may appear, telling manufacturers that a failure is likely to occur in the near future. Chillers who are not internet connected at that moment, provide little insight in this pre-alarming phase.
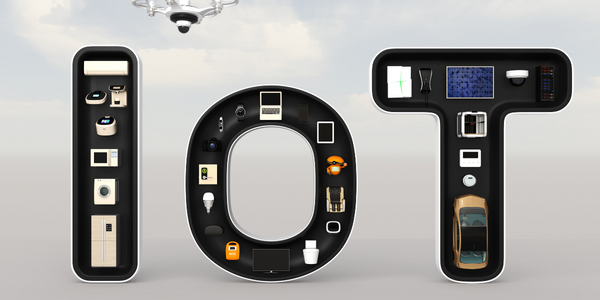
Case Study
Premium Appliance Producer Innovates with Internet of Everything
Sub-Zero faced the largest product launch in the company’s history:It wanted to launch 60 new products as scheduled while simultaneously opening a new “greenfield” production facility, yet still adhering to stringent quality requirements and manage issues from new supply-chain partners. A the same time, it wanted to increase staff productivity time and collaboration while reducing travel and costs.
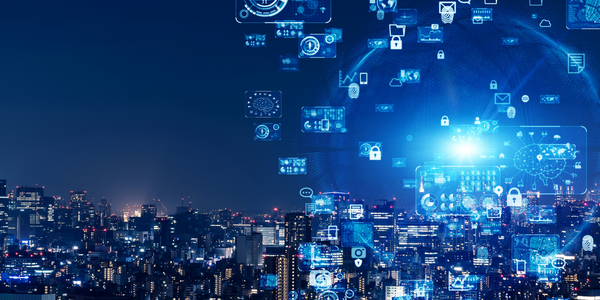
Case Study
Integration of PLC with IoT for Bosch Rexroth
The application arises from the need to monitor and anticipate the problems of one or more machines managed by a PLC. These problems, often resulting from the accumulation over time of small discrepancies, require, when they occur, ex post technical operations maintenance.
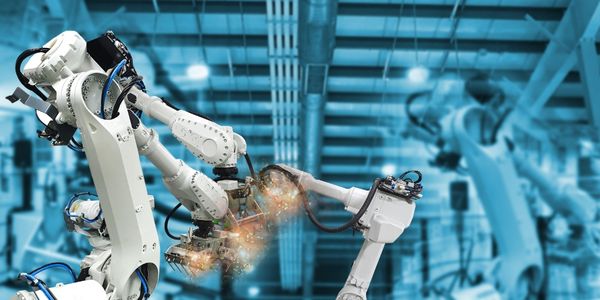
Case Study
Robot Saves Money and Time for US Custom Molding Company
Injection Technology (Itech) is a custom molder for a variety of clients that require precision plastic parts for such products as electric meter covers, dental appliance cases and spools. With 95 employees operating 23 molding machines in a 30,000 square foot plant, Itech wanted to reduce man hours and increase efficiency.