Download PDF
How Phillips 66 doubled employee engagement with intelligent content delivery
Technology Category
- Analytics & Modeling - Machine Learning
- Functional Applications - Enterprise Resource Planning Systems (ERP)
Applicable Industries
- Oil & Gas
Applicable Functions
- Business Operation
- Human Resources
Services
- Software Design & Engineering Services
- System Integration
The Challenge
Phillips 66, a diversified energy manufacturing and logistics company, faced a significant challenge in effectively communicating with its 12,000+ employees spread across different time zones and shift patterns. Traditional methods of sending company-wide emails at a fixed time often resulted in messages being lost in digital noise, leading to low engagement rates. The company needed a smarter way to deliver communications that would consider individual employee preferences and schedules to ensure higher engagement and productivity.
About The Customer
Phillips 66 is a diversified energy manufacturing and logistics company headquartered in Houston, Texas. The company operates 12 oil refineries and various other facilities worldwide, employing over 12,000 people. Known for its commitment to innovation and operational excellence, Phillips 66 has been a significant player in the energy sector, focusing on refining, marketing, and transporting petroleum products. The company has a strong emphasis on employee engagement and productivity, recognizing that a connected workforce is crucial for achieving its business objectives.
The Solution
Phillips 66 implemented Firstup Orchestration, an intelligent communication platform, to enhance its digital employee experience. A key feature of this platform is Engagement Boost, which uses machine learning to automate millions of micro-decisions daily. This feature determines the best time, format, and channel for delivering notifications to each employee based on behavioral data. By personalizing the delivery of communications, Engagement Boost reduces digital overwhelm and fatigue, ensuring that messages are received and engaged with at the most opportune times. After deploying Engagement Boost for corporate communications, Phillips 66 saw a significant increase in employee engagement, prompting the company to expand its use across the organization.
Operational Impact
Quantitative Benefit
Related Case Studies.
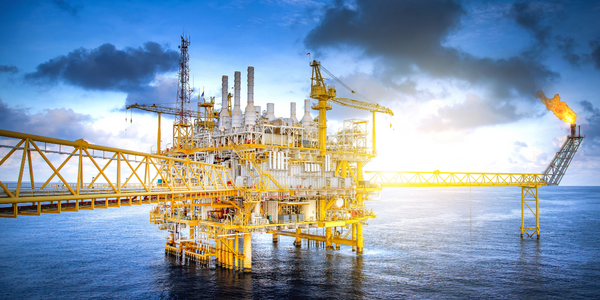
Case Study
Taking Oil and Gas Exploration to the Next Level
DownUnder GeoSolutions (DUG) wanted to increase computing performance by 5 to 10 times to improve seismic processing. The solution must build on current architecture software investments without sacrificing existing software and scale computing without scaling IT infrastructure costs.
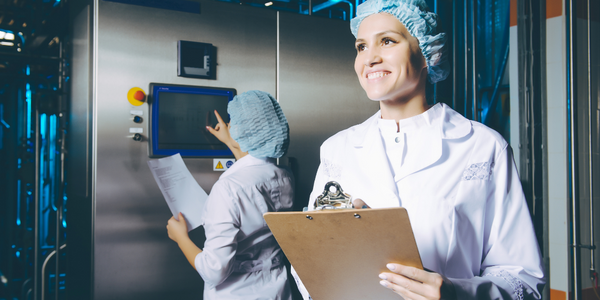
Case Study
Remote Wellhead Monitoring
Each wellhead was equipped with various sensors and meters that needed to be monitored and controlled from a central HMI, often miles away from the assets in the field. Redundant solar and wind generators were installed at each wellhead to support the electrical needs of the pumpstations, temperature meters, cameras, and cellular modules. In addition to asset management and remote control capabilities, data logging for remote surveillance and alarm notifications was a key demand from the customer. Terra Ferma’s solution needed to be power efficient, reliable, and capable of supporting high-bandwidth data-feeds. They needed a multi-link cellular connection to a central server that sustained reliable and redundant monitoring and control of flow meters, temperature sensors, power supply, and event-logging; including video and image files. This open-standard network needed to interface with the existing SCADA and proprietary network management software.
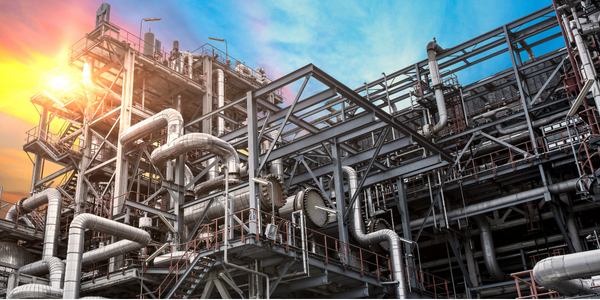
Case Study
Refinery Saves Over $700,000 with Smart Wireless
One of the largest petroleum refineries in the world is equipped to refine various types of crude oil and manufacture various grades of fuel from motor gasoline to Aviation Turbine Fuel. Due to wear and tear, eight hydrogen valves in each refinery were leaking, and each cost $1800 per ton of hydrogen vented. The plant also had leakage on nearly 30 flare control hydrocarbon valves. The refinery wanted a continuous, online monitoring system that could catch leaks early, minimize hydrogen and hydrocarbon production losses, and improve safety for maintenance.