Download PDF
HyperWorks Assists ACENTISS in Developing Elias, an Ultra-Lightweight Electric Airplane
Technology Category
- Analytics & Modeling - Digital Twin / Simulation
- Functional Applications - Manufacturing Execution Systems (MES)
Applicable Industries
- Aerospace
- Automotive
Applicable Functions
- Product Research & Development
- Quality Assurance
Use Cases
- Manufacturing Process Simulation
- Virtual Prototyping & Product Testing
Services
- System Integration
- Testing & Certification
The Challenge
ACENTISS, a company that provides engineering services for structural design, stress and fatigue competencies for metallic and composite structures, was tasked with the development of ELIAS, an all-electric technology demonstrator airplane. The project, named EUROPAS, required the development of a full electric reconnaissance system, datalinks, and a ground control station. Additionally, ACENTISS had to design the structure of the wings and the landing gear. The challenge was to create a lightweight plane that could fly long distances, while also keeping development time and costs to a minimum. To achieve the optimum balance between weight, strength and performance, and to reduce design iterations with the real-world prototype, ACENTISS needed to leverage computer-aided engineering tools, particularly for the structural layout of the composite wings and the kinematics of the landing gear.
About The Customer
ACENTISS is an Approved Center of Engineering, Technology and In Service Support that supports clients through all phases of the product life cycle. The company primarily serves the Aerospace, Renewable Energy, and Automotive industries. ACENTISS leverages its knowledge and experience to investigate and develop new technologies, analyze and optimize clients’ processes, transfer engineering know-how, and provide interim management services. In the area of Engineering, Simulation & Optimization, ACENTISS provides engineering services for structural design, stress and fatigue competencies for metallic and composite structures in all project phases. The organization uses advanced simulation techniques to achieve high quality for the developed products and employs numerical optimization methods and evolutionary strategies to ensure a lightweight design at reasonable costs.
The Solution
To meet the challenges of the project, ACENTISS utilized the Altair HyperWorks Suite, which includes HyperMesh, HyperView, MotionSolve, and OptiStruct. These tools were used to design, calculate, and proof the composite structure of the plane wings, allowing the engineers to determine the optimal fiber volume of the wings to ensure they were lightweight yet sufficiently stiff. ACENTISS also performed kinematic simulations of the landing gear design and topology optimization to ensure the best possible weight/performance ratio. The optimization enabled ACENTISS to shorten the needed development time until they reached a final valid design with a minimum of weight. The HyperWorks products allowed them to create optimal dimensions of all the components and systems they designed. The components were then produced based on the virtually determined specifications and the new plane passed all certification tests easily.
Operational Impact
Quantitative Benefit
Related Case Studies.
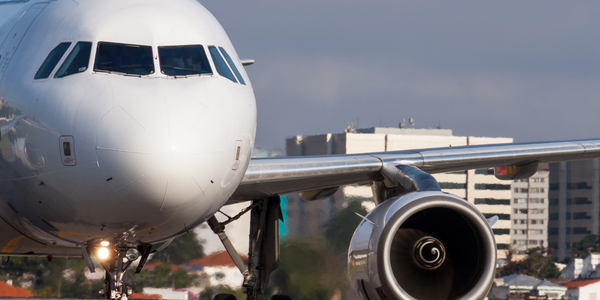
Case Study
Airbus Soars with Wearable Technology
Building an Airbus aircraft involves complex manufacturing processes consisting of thousands of moving parts. Speed and accuracy are critical to business and competitive advantage. Improvements in both would have high impact on Airbus’ bottom line. Airbus wanted to help operators reduce the complexity of assembling cabin seats and decrease the time required to complete this task.
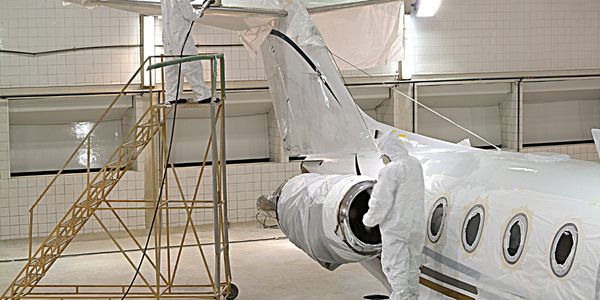
Case Study
Aircraft Predictive Maintenance and Workflow Optimization
First, aircraft manufacturer have trouble monitoring the health of aircraft systems with health prognostics and deliver predictive maintenance insights. Second, aircraft manufacturer wants a solution that can provide an in-context advisory and align job assignments to match technician experience and expertise.
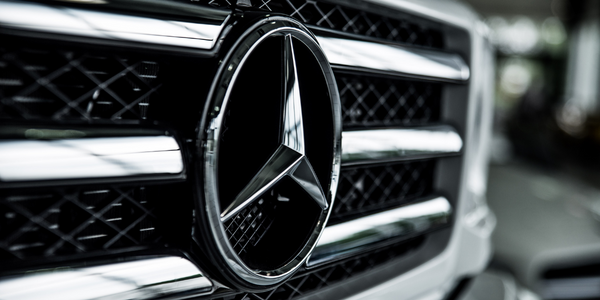
Case Study
Integral Plant Maintenance
Mercedes-Benz and his partner GAZ chose Siemens to be its maintenance partner at a new engine plant in Yaroslavl, Russia. The new plant offers a capacity to manufacture diesel engines for the Russian market, for locally produced Sprinter Classic. In addition to engines for the local market, the Yaroslavl plant will also produce spare parts. Mercedes-Benz Russia and his partner needed a service partner in order to ensure the operation of these lines in a maintenance partnership arrangement. The challenges included coordinating the entire maintenance management operation, in particular inspections, corrective and predictive maintenance activities, and the optimizing spare parts management. Siemens developed a customized maintenance solution that includes all electronic and mechanical maintenance activities (Integral Plant Maintenance).
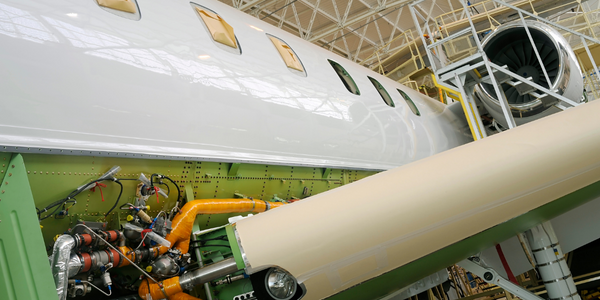
Case Study
Aerospace & Defense Case Study Airbus
For the development of its new wide-body aircraft, Airbus needed to ensure quality and consistency across all internal and external stakeholders. Airbus had many challenges including a very aggressive development schedule and the need to ramp up production quickly to satisfy their delivery commitments. The lack of communication extended design time and introduced errors that drove up costs.