Download PDF
HyperWorks Optimization Capabilities Streamline Unilever's Packaging Design Process
Technology Category
- Analytics & Modeling - Digital Twin / Simulation
Applicable Industries
- Equipment & Machinery
- Packaging
Applicable Functions
- Product Research & Development
- Quality Assurance
Use Cases
- Intelligent Packaging
- Virtual Prototyping & Product Testing
Services
- Testing & Certification
The Challenge
Unilever's Global Packaging Design Group was faced with the challenge of identifying potential packaging issues early in the design process. The discovery of problems after manufacturing had begun could lead to costly impacts, sometimes necessitating modifications in the tools used during production. This made the design process time-consuming as designers had to consider a wide range of possible issues. The group used simulation to validate potential designs and ensure they could be produced. However, outsourcing the simulation work was considered, which would require an average of two months to develop and carry out the appropriate testing.
About The Customer
Unilever, a company with over 120 years of experience in developing consumer products, is one of the world's most well-known companies. The company aims to meet everyday needs for nutrition, hygiene, and personal care with brands that help people feel good, look good, and get more out of life. Today, Unilever produces more than 400 brands focused on health and wellbeing, from food to soap, and other household care products. Unilever's Global Packaging Design Group, based in Trumbull, Conn., develops hard-plastic containers for such brands as Dove, Suave, Caress, Axe, Degree, Ponds, Lux and other hair care, skin and deodorant products. The group works with outside design agencies to develop package concepts and then brings those ideas into a 3D modeling environment to ensure that the initial designs are able to be manufactured.
The Solution
Unilever turned to Altair HyperWorks suite of computer-aided engineering tools to reduce the time required for simulation and significantly lower costs. HyperWorks allowed Unilever to automate the meshing process, as well as the set-up of loads and boundary constraints. The designer could input CAD-based models and simply select a prepared set of parameters. Unilever also used other HyperWorks tools, including the RADIOSS solver, HyperStudy and OptiStruct for topology and topography optimization. These tools helped Unilever ensure that new designs used less material and were more optimized than the ones they were replacing, without compromising their structure.
Operational Impact
Quantitative Benefit
Related Case Studies.
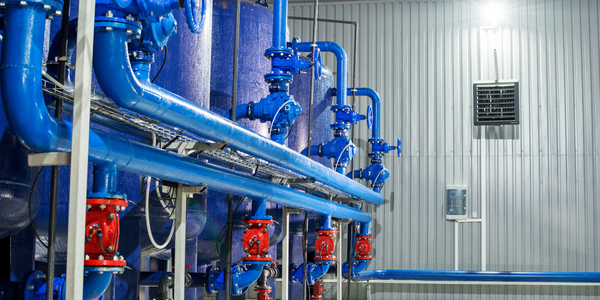
Case Study
Smart Water Filtration Systems
Before working with Ayla Networks, Ozner was already using cloud connectivity to identify and solve water-filtration system malfunctions as well as to monitor filter cartridges for replacements.But, in June 2015, Ozner executives talked with Ayla about how the company might further improve its water systems with IoT technology. They liked what they heard from Ayla, but the executives needed to be sure that Ayla’s Agile IoT Platform provided the security and reliability Ozner required.
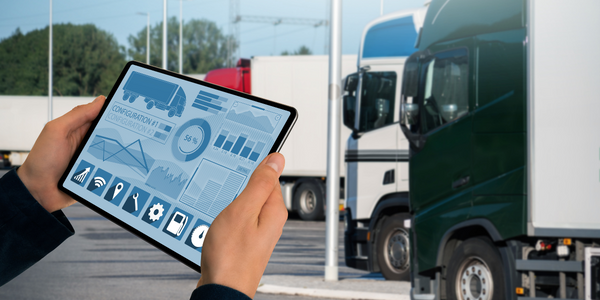
Case Study
IoT enabled Fleet Management with MindSphere
In view of growing competition, Gämmerler had a strong need to remain competitive via process optimization, reliability and gentle handling of printed products, even at highest press speeds. In addition, a digitalization initiative also included developing a key differentiation via data-driven services offers.
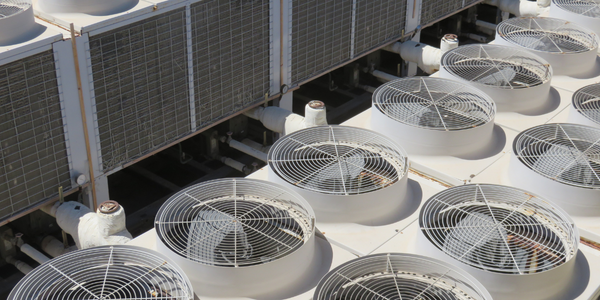
Case Study
Predictive Maintenance for Industrial Chillers
For global leaders in the industrial chiller manufacturing, reliability of the entire production process is of the utmost importance. Chillers are refrigeration systems that produce ice water to provide cooling for a process or industrial application. One of those leaders sought a way to respond to asset performance issues, even before they occur. The intelligence to guarantee maximum reliability of cooling devices is embedded (pre-alarming). A pre-alarming phase means that the cooling device still works, but symptoms may appear, telling manufacturers that a failure is likely to occur in the near future. Chillers who are not internet connected at that moment, provide little insight in this pre-alarming phase.
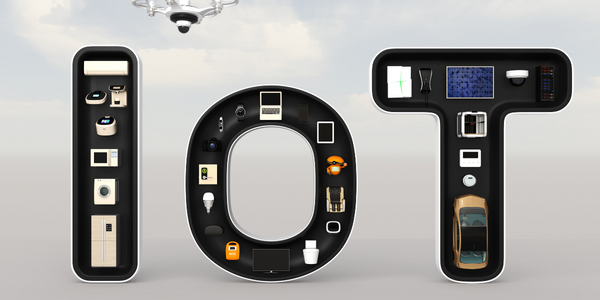
Case Study
Premium Appliance Producer Innovates with Internet of Everything
Sub-Zero faced the largest product launch in the company’s history:It wanted to launch 60 new products as scheduled while simultaneously opening a new “greenfield” production facility, yet still adhering to stringent quality requirements and manage issues from new supply-chain partners. A the same time, it wanted to increase staff productivity time and collaboration while reducing travel and costs.
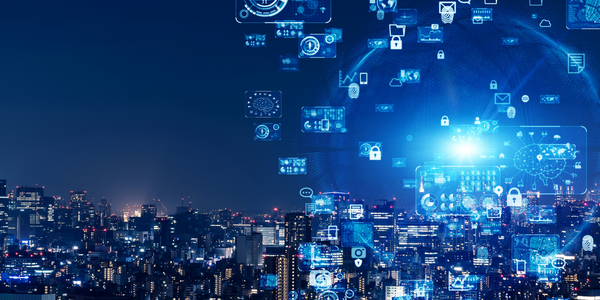
Case Study
Integration of PLC with IoT for Bosch Rexroth
The application arises from the need to monitor and anticipate the problems of one or more machines managed by a PLC. These problems, often resulting from the accumulation over time of small discrepancies, require, when they occur, ex post technical operations maintenance.
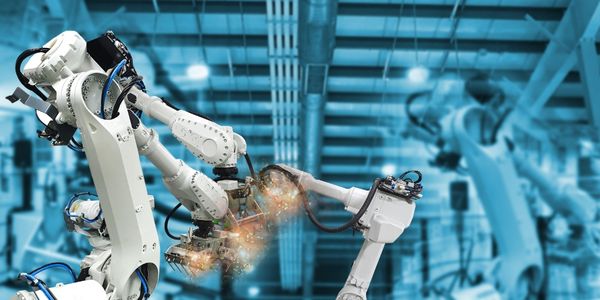
Case Study
Robot Saves Money and Time for US Custom Molding Company
Injection Technology (Itech) is a custom molder for a variety of clients that require precision plastic parts for such products as electric meter covers, dental appliance cases and spools. With 95 employees operating 23 molding machines in a 30,000 square foot plant, Itech wanted to reduce man hours and increase efficiency.