Download PDF
Improving Extrusion Die Life and Efficiency with Altair HyperXtrude
Technology Category
- Analytics & Modeling - Digital Twin / Simulation
- Networks & Connectivity - Routers & Bridges
Applicable Industries
- Aerospace
- Automotive
Applicable Functions
- Product Research & Development
- Quality Assurance
Use Cases
- Manufacturing Process Simulation
- Virtual Reality
Services
- Testing & Certification
The Challenge
The aluminum extrusion industry has been facing significant challenges due to the shorter life and frequent failures of dies used in the extrusion of hard alloys. These issues have a direct impact on productivity and increase production costs. The situation is further complicated by the increasing use of aluminum extrusions in various industries such as automotive, aerospace, railway, medical, architectural, and others. These applications have stringent strength and surface quality requirements, often necessitating the use of newer and harder alloys. Traditional die design practices have proven inadequate for these new demands, resulting in dies with shorter lifespans. The Conglin Group, a leader in Chinese aluminum fabrication technology, sought to address these challenges and meet the growing demands from both domestic and international markets.
About The Customer
The Conglin Group is a leading player in the Chinese aluminum fabrication industry. In recent years, they have seen a significant increase in the use of aluminum extrusions in a wide range of applications, including automotive, aerospace, railway, medical, architectural, and other industries. These applications have stringent strength and surface quality requirements, often requiring the use of newer and harder alloys. The Conglin Group has been at the forefront of addressing these challenges and meeting the ever-increasing demands from both domestic and international markets. They have combined their design philosophy, manufacturing experience, and skills in using finite element simulation software to overcome the challenges posed by extruding hard and newer alloys.
The Solution
The Conglin Group turned to Altair HyperXtrude, a finite element simulation software, to predict die performance and conduct virtual die tryouts. By analyzing the extrusion dies using HyperXtrude and interpreting the simulation data, Conglin was able to accurately predict the service life of an extrusion die. The software allowed them to identify areas of stress concentration and their intensity, which are critical factors in determining the life and productivity of a die. Based on the insights gained from the software, Conglin was able to modify and test die designs to improve their lifespan and reduce the number of die trials. For instance, in one case, they redesigned a die that initially fractured after extruding just 10 billets to one that did not fail even after extruding 100 billets. This was achieved by adjusting the design to overcome high levels of stress and introducing several portholes to feed material to different regions of the die, producing a balanced flow at the die exit.
Operational Impact
Quantitative Benefit
Related Case Studies.
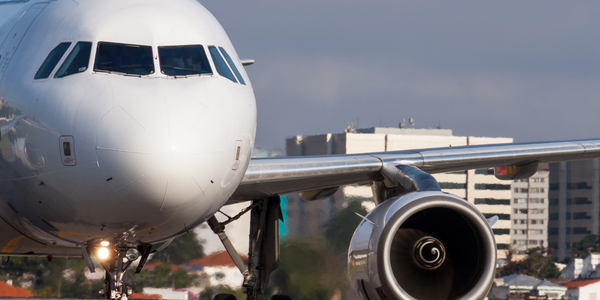
Case Study
Airbus Soars with Wearable Technology
Building an Airbus aircraft involves complex manufacturing processes consisting of thousands of moving parts. Speed and accuracy are critical to business and competitive advantage. Improvements in both would have high impact on Airbus’ bottom line. Airbus wanted to help operators reduce the complexity of assembling cabin seats and decrease the time required to complete this task.
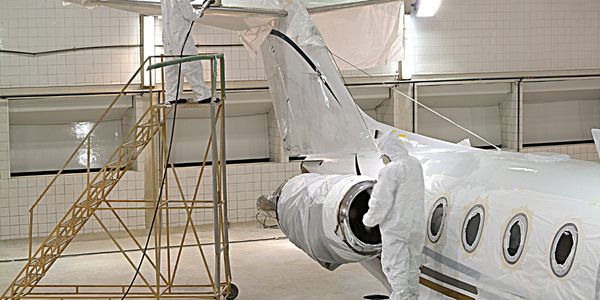
Case Study
Aircraft Predictive Maintenance and Workflow Optimization
First, aircraft manufacturer have trouble monitoring the health of aircraft systems with health prognostics and deliver predictive maintenance insights. Second, aircraft manufacturer wants a solution that can provide an in-context advisory and align job assignments to match technician experience and expertise.
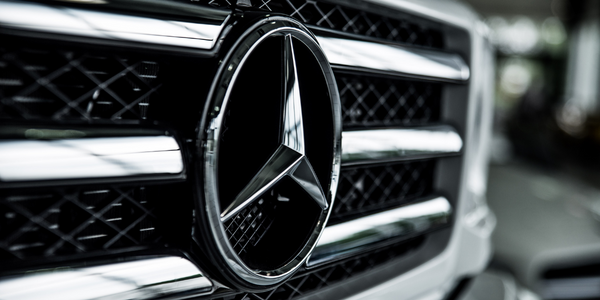
Case Study
Integral Plant Maintenance
Mercedes-Benz and his partner GAZ chose Siemens to be its maintenance partner at a new engine plant in Yaroslavl, Russia. The new plant offers a capacity to manufacture diesel engines for the Russian market, for locally produced Sprinter Classic. In addition to engines for the local market, the Yaroslavl plant will also produce spare parts. Mercedes-Benz Russia and his partner needed a service partner in order to ensure the operation of these lines in a maintenance partnership arrangement. The challenges included coordinating the entire maintenance management operation, in particular inspections, corrective and predictive maintenance activities, and the optimizing spare parts management. Siemens developed a customized maintenance solution that includes all electronic and mechanical maintenance activities (Integral Plant Maintenance).
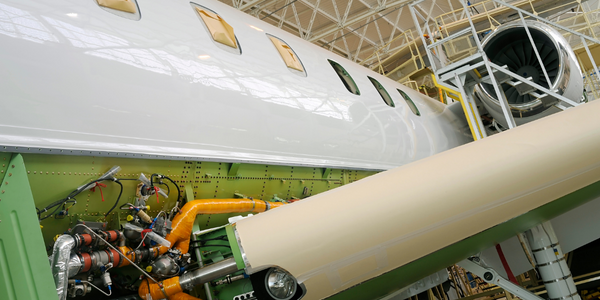
Case Study
Aerospace & Defense Case Study Airbus
For the development of its new wide-body aircraft, Airbus needed to ensure quality and consistency across all internal and external stakeholders. Airbus had many challenges including a very aggressive development schedule and the need to ramp up production quickly to satisfy their delivery commitments. The lack of communication extended design time and introduced errors that drove up costs.