Download PDF
Improving Gearbox Efficiency with IoT: A Case Study on HYCET
Technology Category
- Sensors - Flow Meters
- Sensors - Liquid Detection Sensors
Applicable Industries
- Electrical Grids
- Oil & Gas
Applicable Functions
- Product Research & Development
- Quality Assurance
Use Cases
- Experimentation Automation
- Time Sensitive Networking
Services
- Hardware Design & Engineering Services
- Testing & Certification
The Challenge
HYCET Transmission Technology Hebei Co. Ltd (HYCET), a comprehensive enterprise focusing on E-drive systems, faced a significant challenge in troubleshooting gearbox mechanical failures. These failures, including pitting, erosion, and peeling, were primarily caused by insufficient lubrication. Given that E-drive speed can reach up to 20,000 rpm, HYCET needed a solution that could accurately calculate churning losses. The company also needed to consider factors such as windage effects, oil volume, and the amount of air bubbles (aeration) present in oil. The challenge was to find a solution that could provide detailed insights into these complex flow phenomena and help the team answer vital questions related to oil flow and potential leaks.
About The Customer
HYCET Transmission Technology Hebei Co. Ltd (HYCET) is a comprehensive enterprise that specializes in E-drive systems. The company designs and manufactures transmission systems for both pure electric vehicles (EV) and hybrid vehicles (HEV), catering to the needs of vehicles from A0 class to medium and large SUVs. HYCET's research and development center covers both domestic and foreign vehicle transmission systems and can perform simulations and experiments from the component level to the full-vehicle level. The company is committed to improving the efficiency and reliability of its products, and to this end, it continually seeks innovative solutions to address its challenges.
The Solution
To address its challenges, HYCET adopted Altair solutions, which combine smooth particle hydrodynamics (SPH) with GPU hardware to streamline innovation and problem-solving. The company primarily utilized Altair® nanoFluidX® and Altair® SimLab® throughout the process. With SimLab, a powerful pre-processing solution, the team was able to create smoothed-particle hydrodynamics (SPH) models from complex raw CAD geometry in less than a day and define physical and numeric parameters. The team could also submit calculations directly from local and remote GPU servers. The use of nanoFluidX gave the HYCET designers more insight into complex flow phenomena and helped them answer vital questions related to oil flow and potential leaks. The solution also allowed the team to assess multiple different scenarios, augmenting the physical testing process with unprecedented power and accuracy.
Operational Impact
Quantitative Benefit
Related Case Studies.
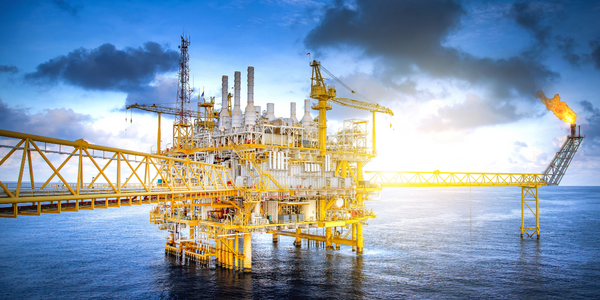
Case Study
Taking Oil and Gas Exploration to the Next Level
DownUnder GeoSolutions (DUG) wanted to increase computing performance by 5 to 10 times to improve seismic processing. The solution must build on current architecture software investments without sacrificing existing software and scale computing without scaling IT infrastructure costs.
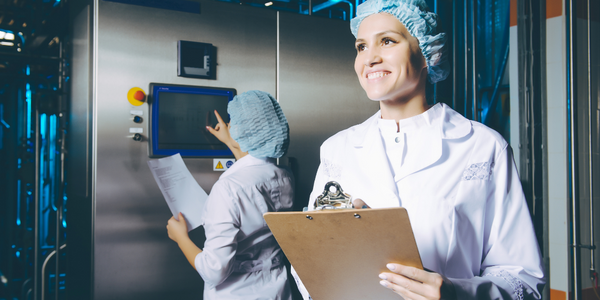
Case Study
Remote Wellhead Monitoring
Each wellhead was equipped with various sensors and meters that needed to be monitored and controlled from a central HMI, often miles away from the assets in the field. Redundant solar and wind generators were installed at each wellhead to support the electrical needs of the pumpstations, temperature meters, cameras, and cellular modules. In addition to asset management and remote control capabilities, data logging for remote surveillance and alarm notifications was a key demand from the customer. Terra Ferma’s solution needed to be power efficient, reliable, and capable of supporting high-bandwidth data-feeds. They needed a multi-link cellular connection to a central server that sustained reliable and redundant monitoring and control of flow meters, temperature sensors, power supply, and event-logging; including video and image files. This open-standard network needed to interface with the existing SCADA and proprietary network management software.
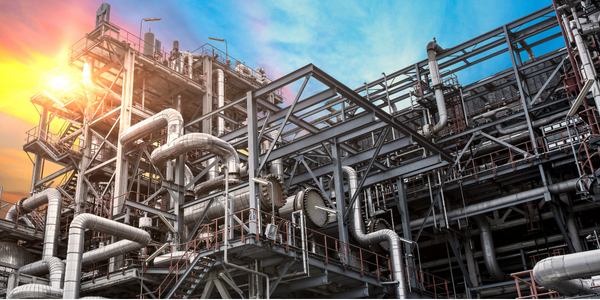
Case Study
Refinery Saves Over $700,000 with Smart Wireless
One of the largest petroleum refineries in the world is equipped to refine various types of crude oil and manufacture various grades of fuel from motor gasoline to Aviation Turbine Fuel. Due to wear and tear, eight hydrogen valves in each refinery were leaking, and each cost $1800 per ton of hydrogen vented. The plant also had leakage on nearly 30 flare control hydrocarbon valves. The refinery wanted a continuous, online monitoring system that could catch leaks early, minimize hydrogen and hydrocarbon production losses, and improve safety for maintenance.