Download PDF
Improving Workforce Productivity and Retention at Associated Food Stores
Technology Category
- Functional Applications - Enterprise Resource Planning Systems (ERP)
Applicable Industries
- Retail
Applicable Functions
- Human Resources
- Warehouse & Inventory Management
Use Cases
- Inventory Management
Services
- System Integration
The Challenge
Associated Food Stores (AFS) is a cooperatively owned wholesale distributor that operates 43 corporate supermarkets and supports over 400 independently owned supermarket locations across eight states. The company was facing challenges with its warehouse labor scheduling, which was based on static schedules from week to week regardless of daily demand changes. This resulted in wasted labor. Additionally, AFS’s warehouse operates in an area with highly competitive demand for labor. A lack of flexibility in scheduling was causing higher than desired turnover which increased hiring and training costs. The previous solution AFS used for labor scheduling and time and attendance was not integrated, causing a lack of cohesion in managing the workforce.
About The Customer
Associated Food Stores (AFS) is a cooperatively owned wholesale distributor headquartered in Salt Lake City, Utah. They operate 43 corporate supermarkets and support over 400 independently owned supermarket locations across eight states. AFS is committed to independent retailers by providing quality products, support and exceptional service. The AFS distribution center is in an area where there is significant competition for labor resources. This raises turnover and the associated costs to hire and train replacement workers.
The Solution
AFS implemented Blue Yonder’s workforce management capabilities which enable them to automatically schedule labor according to actual demand and associate preferences, improving associate satisfaction while saving significant labor costs. The solution’s forecasts allow AFS to look ahead and better plan their cross-department labor. It provides AFS with data on how their warehouse is performing and where they can better allocate labor. Blue Yonder’s workforce management capabilities also allow AFS to be proactive. The solution's mobile self-service features enable AFS associates to create their own schedules to accommodate the needs of their personal lives, as well as process time-off requests. It also gives associates the option to schedule themselves for jobs other than their normal assignments.
Operational Impact
Quantitative Benefit
Related Case Studies.
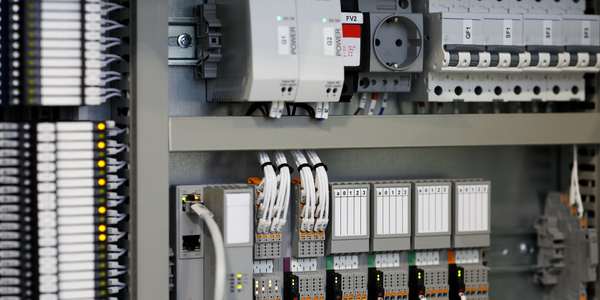
Case Study
Improving Production Line Efficiency with Ethernet Micro RTU Controller
Moxa was asked to provide a connectivity solution for one of the world's leading cosmetics companies. This multinational corporation, with retail presence in 130 countries, 23 global braches, and over 66,000 employees, sought to improve the efficiency of their production process by migrating from manual monitoring to an automatic productivity monitoring system. The production line was being monitored by ABB Real-TPI, a factory information system that offers data collection and analysis to improve plant efficiency. Due to software limitations, the customer needed an OPC server and a corresponding I/O solution to collect data from additional sensor devices for the Real-TPI system. The goal is to enable the factory information system to more thoroughly collect data from every corner of the production line. This will improve its ability to measure Overall Equipment Effectiveness (OEE) and translate into increased production efficiencies. System Requirements • Instant status updates while still consuming minimal bandwidth to relieve strain on limited factory networks • Interoperable with ABB Real-TPI • Small form factor appropriate for deployment where space is scarce • Remote software management and configuration to simplify operations
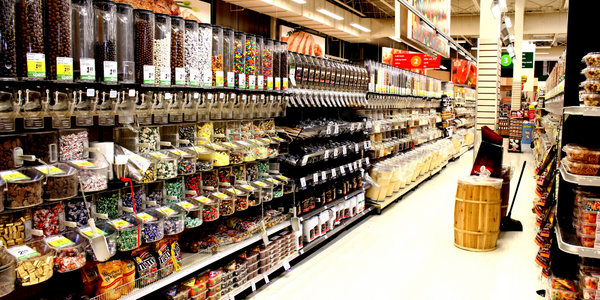
Case Study
How Sirqul’s IoT Platform is Crafting Carrefour’s New In-Store Experiences
Carrefour Taiwan’s goal is to be completely digital by end of 2018. Out-dated manual methods for analysis and assumptions limited Carrefour’s ability to change the customer experience and were void of real-time decision-making capabilities. Rather than relying solely on sales data, assumptions, and disparate systems, Carrefour Taiwan’s CEO led an initiative to find a connected IoT solution that could give the team the ability to make real-time changes and more informed decisions. Prior to implementing, Carrefour struggled to address their conversion rates and did not have the proper insights into the customer decision-making process nor how to make an immediate impact without losing customer confidence.
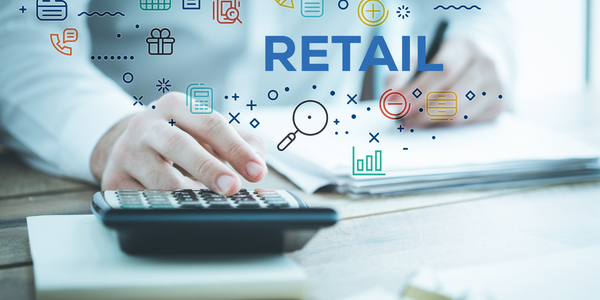
Case Study
Digital Retail Security Solutions
Sennco wanted to help its retail customers increase sales and profits by developing an innovative alarm system as opposed to conventional connected alarms that are permanently tethered to display products. These traditional security systems were cumbersome and intrusive to the customer shopping experience. Additionally, they provided no useful data or analytics.
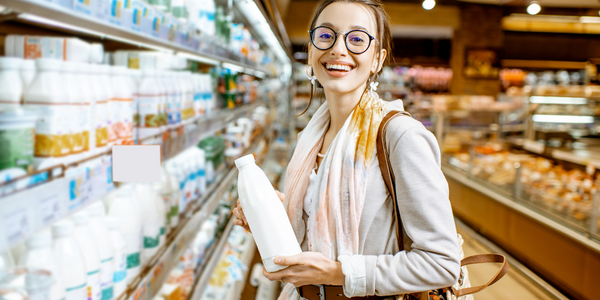
Case Study
Ensures Cold Milk in Your Supermarket
As of 2014, AK-Centralen has over 1,500 Danish supermarkets equipped, and utilizes 16 operators, and is open 24 hours a day, 365 days a year. AK-Centralen needed the ability to monitor the cooling alarms from around the country, 24 hours a day, 365 days a year. Each and every time the door to a milk cooler or a freezer does not close properly, an alarm goes off on a computer screen in a control building in southwestern Odense. This type of alarm will go off approximately 140,000 times per year, equating to roughly 400 alarms in a 24-hour period. Should an alarm go off, then there is only a limited amount of time to act before dairy products or frozen pizza must be disposed of, and this type of waste can quickly start to cost a supermarket a great deal of money.
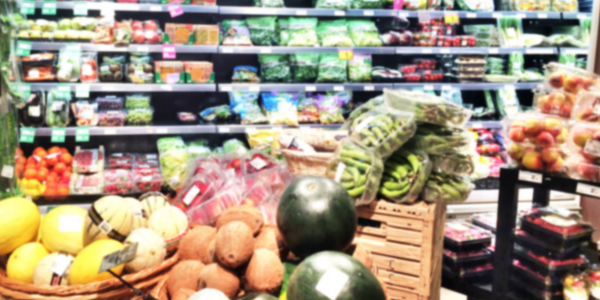
Case Study
Supermarket Energy Savings
The client had previously deployed a one-meter-per-store monitoring program. Given the manner in which energy consumption changes with external temperature, hour of the day, day of week and month of year, a single meter solution lacked the ability to detect the difference between a true problem and a changing store environment. Most importantly, a single meter solution could never identify root cause of energy consumption changes. This approach never reduced the number of truck-rolls or man-hours required to find and resolve issues.