Download PDF
Increasing Transparency with Tablet PCs
Technology Category
- Application Infrastructure & Middleware - Data Exchange & Integration
- Functional Applications - Enterprise Resource Planning Systems (ERP)
- Functional Applications - Warehouse Control Systems (WCS)
Applicable Industries
- Consumer Goods
Applicable Functions
- Quality Assurance
- Warehouse & Inventory Management
Use Cases
- Inventory Management
- Warehouse Automation
Services
- Software Design & Engineering Services
- System Integration
The Challenge
sudhoff technik, a wholesaler of custom rubber, plastic, and aluminum products, was facing challenges with its warehouse workflows. The company was dealing with a large volume of paper documents, including incoming documents and approximately 130,000 outgoing proof-of-shipping slips and invoices. The process of sorting and filing these documents was tedious and prone to errors. If a customer called to track a shipment, an employee in the warehouse would have to go through all of this documentation to find the answer. The company was also building a new logistics center and needed to eliminate the space-wasting paper archive and make their business processes flow more efficiently.
About The Customer
sudhoff technik GmbH is a wholesaler of custom rubber, plastic, and aluminum products. The company works with highly specialized, often very small vendors. Because of limited resources and experience, these vendors might not be able to maintain the high level of quality required by sudhoff technik's customers. Therefore, the company adds an extra step of quality control. Based on a customer’s requirements, sudhoff technik bundles together all kinds of products that can come from all over right in their warehouse. This is only possible with a well-organized facility as well as intelligent electronic warehouse management and order processing. The company was also building a new logistics center and needed to eliminate the space-wasting paper archive and make their business processes flow more efficiently.
The Solution
The company implemented DocuWare, a document management system (DMS), to electronically store incoming documents and outgoing proof-of-shipping slips and invoices. The system was integrated with Microsoft Axapta and Tablet PCs. Outgoing shipping slips are now stored right after a shipment leaves, captured using a Panasonic KV-S2026C Scanner, and stored in a central document pool. A message is automatically sent in real-time to their ERP system. To answer customer queries about a delivery date, employees can check within their Microsoft Axapta system with a few mouse clicks if their shipment has left the facility. More detailed information about the shipment can be accessed from the central document pool. On the receiving side, all records are scanned directly upon a shipment’s arrival. In a window set up in the ERP System, employees in Administration and Quality Control are informed when shipments are received. This electronic shipment is then electronically labeled with the status of “Not Checked” and may not be booked until it has been authorized by Quality Control.
Operational Impact
Quantitative Benefit
Related Case Studies.
.png)
Case Study
Improving Vending Machine Profitability with the Internet of Things (IoT)
The vending industry is undergoing a sea change, taking advantage of new technologies to go beyond just delivering snacks to creating a new retail location. Intelligent vending machines can be found in many public locations as well as company facilities, selling different types of goods and services, including even computer accessories, gold bars, tickets, and office supplies. With increasing sophistication, they may also provide time- and location-based data pertaining to sales, inventory, and customer preferences. But at the end of the day, vending machine operators know greater profitability is driven by higher sales and lower operating costs.
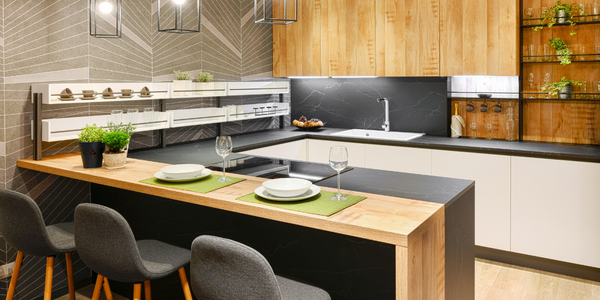
Case Study
Series Production with Lot-size-1 Flexibility
Nobilia manufactures customized fitted kitchens with a lot size of 1. They require maximum transparency of tracking design data and individual processing steps so that they can locate a particular piece of kitchen furniture in the sequence of processes.
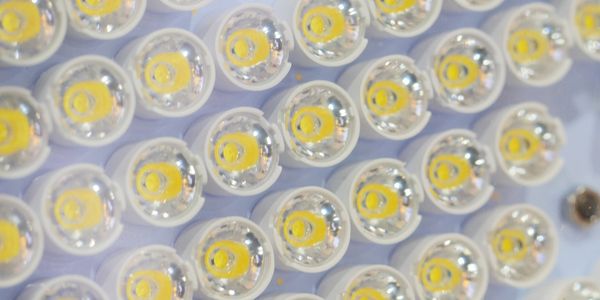
Case Study
American Eagle Achieves LEED with GE LED Lighting Fixtures
American Eagle Outfitters (AEO) was in the process of building a new distribution center. The AEO facility management team decided to look at alternate options for lighting layout that could provide energy and maintenance savings. AEO would need a full-time maintenance employee just to replace burned-out fluorescent tubes.
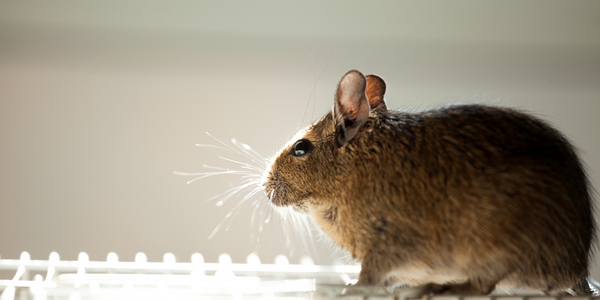
Case Study
Revolutionizing Rodent Control
From pet- and child-safe traps, to touch-free and live-catch rodent control solutions, Victor continues to stay committed to producing superior products that meet the varying needs of today’s pest control professionals. And, with a long standing history supporting customers in the food processing, service, and retail settings, Victor knew that strict regulations were costing organizations thousands of dollars in excess overhead trying to manage their rodent-control solutions. Trap inspections in these environments are often difficult and time consuming, requiring personnel to manually check a trap’s status multiple times per day, amounting to over six hours of manual labor. Victor is looking for an innovative way to increase operational efficiencies with the use of technology.