Industry 4.0 and Cognitive Manufacturing
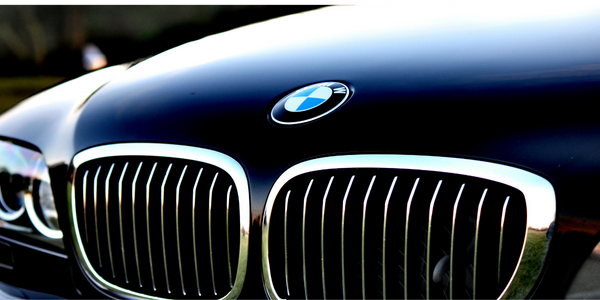
- Analytics & Modeling - Machine Learning
- Automotive
- Discrete Manufacturing
- Quality Assurance
- Computer Vision
- Machine Condition Monitoring
- System Integration
Manufacturers are facing risky challenges associated with complex visual inspection activities. Many human inspectors, operators and engineers are needed at each manufacturer. They have a full workload of repetitive tasks aimed at identifying hundreds of defects. This results in major plant labour costs, issues with inspection accuracy and consistency, a need for employee training and potential health problems for inspections in hazardous areas.
BMW
KUKA
BMW - multinational corporate manufacturer of luxury vehicles and motorcycles headquartered.
KUKA - manufacturer of industrial robots and systems for factory automation.
The visual inspection system is based on machine-learning algorithms and leverages many patterns of visual inspection, such as impurity/high-contrast areas, geometry detection and verification, abnormal texture and area detection, and color/brightness feature extraction and verification to determine quality defects. (Examples of what this system can detect include brake caliper defects, body shop and paint shop defects or damage, part deformation, spare part bumps and car dashboard scratches.)
The visual inspection capability of IBM’s suite of solutions is integrated inside the equipment line and robotics. In this showcase, IBM is inspecting several door handles from the new BMW 5 Series for manufacturing defects using the Watson Visual Recognition Service.
Related Case Studies.
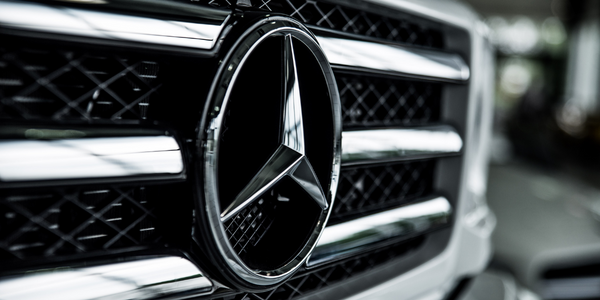
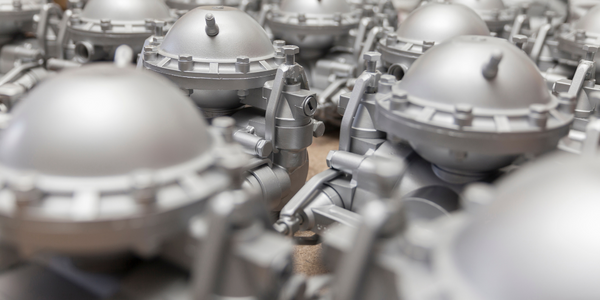