Download PDF
Jones Plastic fast-tracks to scalability & agility with Atera
Technology Category
- Functional Applications - Enterprise Asset Management Systems (EAM)
- Functional Applications - Remote Monitoring & Control Systems
Applicable Functions
- Business Operation
- Facility Management
Use Cases
- Predictive Maintenance
- Remote Asset Management
Services
- Software Design & Engineering Services
- System Integration
The Challenge
Jones Plastic, a global leader in injection molding, manufacturing, and assembly, had challenges managing its IT infrastructure to support remote and on-premise employees. Only seven employees were answering support tickets submitted by more than 800 employees across six international sites. As a result, IT support response times were slow, and communication was ineffective, resulting in wasted time and resources. Jones Plastic sought a solution to control its IT infrastructure and improve its remote access capabilities to employees’ devices.
About The Customer
Jones Plastic is a global leader in injection molding, manufacturing, and assembly. The company operates across six international sites and employs over 800 people. Despite its large scale, the company faced significant challenges in managing its IT infrastructure, particularly in supporting both remote and on-premise employees. With only seven IT employees handling support tickets, the response times were slow, and communication was often ineffective. This inefficiency led to wasted time and resources, prompting the company to seek a more robust IT management solution.
The Solution
By using Atera, Jones Plastic accesses hardware remotely, views the apps used, monitors hard drive space, runs therapeutic reboots, and deploys software bundles effortlessly. Additionally, Atera's customizability allows IT managers to set alarms and receive notifications before problems escalate. For example, alerts can be set for the core temperature of hard drives and the hard drive space available. The implementation of Atera has enabled Jones Plastic to improve its IT support response times to under one hour per ticket, well below the industry standard of between 4-6 hours. The IT team can now deploy fixes to other devices, eliminating recurring problems. As Atera is priced per technician rather than per end-user, the implementation of the solution was easy and cost-effective for Jones Plastic. The company plans to continue to use Atera's services to further improve IT support response times and enable future growth.
Operational Impact
Quantitative Benefit
Related Case Studies.
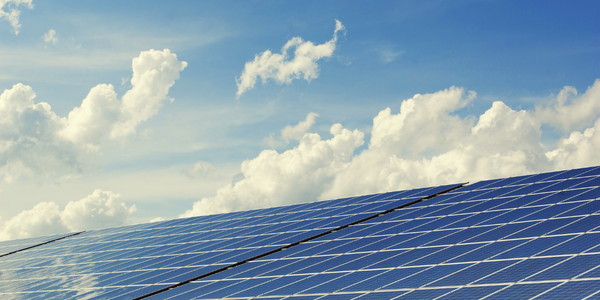
Case Study
Remote Monitoring & Predictive Maintenance App for a Solar Energy System
The maintenance & tracking of various modules was an overhead for the customer due to the huge labor costs involved. Being an advanced solar solutions provider, they wanted to ensure early detection of issues and provide the best-in-class customer experience. Hence they wanted to automate the whole process.
.png)
Case Study
Improving Vending Machine Profitability with the Internet of Things (IoT)
The vending industry is undergoing a sea change, taking advantage of new technologies to go beyond just delivering snacks to creating a new retail location. Intelligent vending machines can be found in many public locations as well as company facilities, selling different types of goods and services, including even computer accessories, gold bars, tickets, and office supplies. With increasing sophistication, they may also provide time- and location-based data pertaining to sales, inventory, and customer preferences. But at the end of the day, vending machine operators know greater profitability is driven by higher sales and lower operating costs.
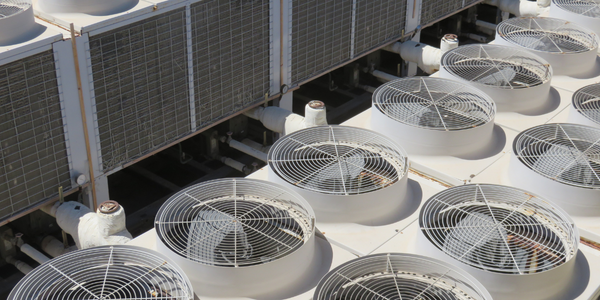
Case Study
Predictive Maintenance for Industrial Chillers
For global leaders in the industrial chiller manufacturing, reliability of the entire production process is of the utmost importance. Chillers are refrigeration systems that produce ice water to provide cooling for a process or industrial application. One of those leaders sought a way to respond to asset performance issues, even before they occur. The intelligence to guarantee maximum reliability of cooling devices is embedded (pre-alarming). A pre-alarming phase means that the cooling device still works, but symptoms may appear, telling manufacturers that a failure is likely to occur in the near future. Chillers who are not internet connected at that moment, provide little insight in this pre-alarming phase.
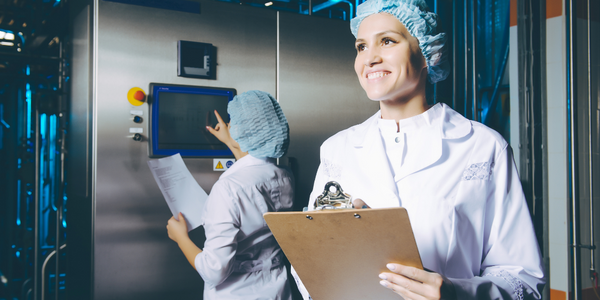
Case Study
Remote Wellhead Monitoring
Each wellhead was equipped with various sensors and meters that needed to be monitored and controlled from a central HMI, often miles away from the assets in the field. Redundant solar and wind generators were installed at each wellhead to support the electrical needs of the pumpstations, temperature meters, cameras, and cellular modules. In addition to asset management and remote control capabilities, data logging for remote surveillance and alarm notifications was a key demand from the customer. Terra Ferma’s solution needed to be power efficient, reliable, and capable of supporting high-bandwidth data-feeds. They needed a multi-link cellular connection to a central server that sustained reliable and redundant monitoring and control of flow meters, temperature sensors, power supply, and event-logging; including video and image files. This open-standard network needed to interface with the existing SCADA and proprietary network management software.