Download PDF
Keep Truck in Case study
Technology Category
- Platform as a Service (PaaS) - Data Management Platforms
Applicable Industries
- Oil & Gas
Applicable Functions
- Logistics & Transportation
Use Cases
- Fleet Management
- Remote Asset Management
Services
- Cloud Planning, Design & Implementation Services
- Data Science Services
The Challenge
Trade Star Energy, an oil and gas company based in Saint George, Utah, had a fleet of 196 drivers spread out over several states. The drivers recorded their logs on paper, which presented significant challenges for DOT compliance. The company's Senior Operations Manager, Kari Gibb, had to wait until the drivers returned to Saint George to drop off their logs. He then manually audited each log, checking for Form & Manner errors or Hours of Service (HOS) violations. The distance the drivers traveled, coupled with the slow audit process, resulted in many errors in the logs. Kari had evaluated electronic logs throughout his career, but found them either too expensive or not meeting the needs of an oil hauling carrier like Trade Star.
About The Customer
Trade Star Energy is an oil and gas company headquartered in Saint George, Utah. The company operates a fleet of 196 vehicles, which are spread out over several states including Montana, North Dakota, Colorado, New Mexico, Wyoming, and Texas. The company's fleet is primarily used for oil hauling. The company's operations are overseen by Senior Operations Manager, Kari Gibb. Prior to implementing KeepTruckin, the company relied on paper logs for recording driver logs, which presented significant challenges for DOT compliance.
The Solution
Trade Star Energy implemented KeepTruckin, a data management platform that incorporated the HOS rules and exemptions specific to fleets hauling oil. The platform was user-friendly and affordable, making it a popular choice among the drivers. The ability to audit driver logs remotely allowed Kari to have much greater oversight over his fleet. KeepTruckin acted as if Kari was sitting next to his drivers instructing them when to pull over, even if the drivers were not 100% familiar with the HOS rules. The implementation of KeepTruckin resulted in perfect roadside inspections and the FMCSA informed Kari that they wouldn't need to do a company-wide audit this round because of the strong shape his driver logs were in.
Operational Impact
Related Case Studies.
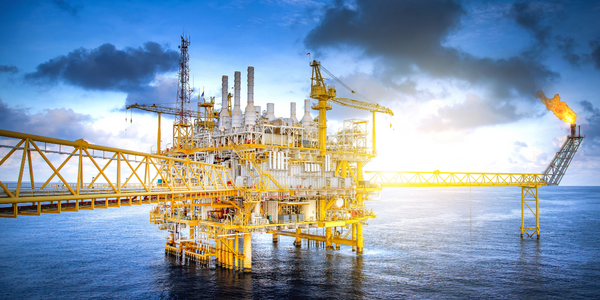
Case Study
Taking Oil and Gas Exploration to the Next Level
DownUnder GeoSolutions (DUG) wanted to increase computing performance by 5 to 10 times to improve seismic processing. The solution must build on current architecture software investments without sacrificing existing software and scale computing without scaling IT infrastructure costs.
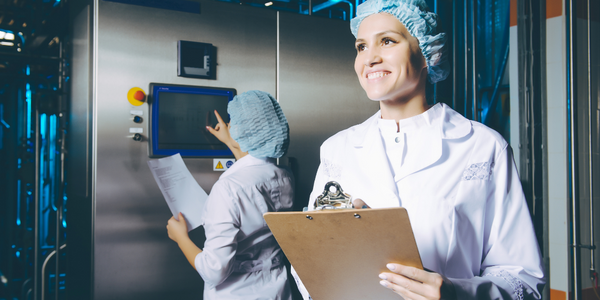
Case Study
Remote Wellhead Monitoring
Each wellhead was equipped with various sensors and meters that needed to be monitored and controlled from a central HMI, often miles away from the assets in the field. Redundant solar and wind generators were installed at each wellhead to support the electrical needs of the pumpstations, temperature meters, cameras, and cellular modules. In addition to asset management and remote control capabilities, data logging for remote surveillance and alarm notifications was a key demand from the customer. Terra Ferma’s solution needed to be power efficient, reliable, and capable of supporting high-bandwidth data-feeds. They needed a multi-link cellular connection to a central server that sustained reliable and redundant monitoring and control of flow meters, temperature sensors, power supply, and event-logging; including video and image files. This open-standard network needed to interface with the existing SCADA and proprietary network management software.
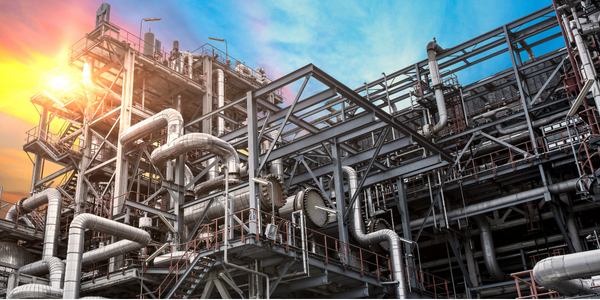
Case Study
Refinery Saves Over $700,000 with Smart Wireless
One of the largest petroleum refineries in the world is equipped to refine various types of crude oil and manufacture various grades of fuel from motor gasoline to Aviation Turbine Fuel. Due to wear and tear, eight hydrogen valves in each refinery were leaking, and each cost $1800 per ton of hydrogen vented. The plant also had leakage on nearly 30 flare control hydrocarbon valves. The refinery wanted a continuous, online monitoring system that could catch leaks early, minimize hydrogen and hydrocarbon production losses, and improve safety for maintenance.