Download PDF
Keeping Success Flowing Strong
Technology Category
- Analytics & Modeling - Predictive Analytics
- Functional Applications - Enterprise Resource Planning Systems (ERP)
Applicable Industries
- Food & Beverage
Applicable Functions
- Business Operation
- Quality Assurance
Use Cases
- Predictive Maintenance
- Process Control & Optimization
- Real-Time Location System (RTLS)
Services
- Software Design & Engineering Services
- System Integration
- Training
The Challenge
Nestlé Waters had been using a cumbersome, paper-based system to collect and analyze data. When issues arose that required immediate attention, the company’s quality engineers had to disrupt operators on the production line to retrieve the necessary data. Nestlé Waters’ goal was to implement a system that would enable them to easily monitor, review, and trend real-time quality data. In addition, they wanted to standardize on one solution—across all their facilities—to complement their existing IT infrastructure.
About The Customer
Nestlé Waters, the world’s leading bottled water company, has built a solid reputation on the quality and purity of its products. Established in more than 100 countries, the company boasts a portfolio of 48 brands and operates 87 manufacturing sites in 30 countries. With an annual revenue exceeding $8 billion and a market share of 11%, Nestlé Waters meets consumer needs by keeping its wide variety of products flowing through strong distribution channels. The company has emerged as a substantial player in the bottled water market, strengthened by continuous improvement efforts.
The Solution
After a thorough needs-analysis evaluation, Nestlé Waters determined that InfinityQS® solutions best satisfied their criteria for quality documentation and analysis. To accelerate and streamline the software implementation, the Nestlé Waters IT team leveraged InfinityQS Professional Services. These expert services are provided by teams of skilled, certified quality engineers, industrial statisticians, and Six Sigma Black Belts—all with extensive manufacturing experience. The teams worked closely during all stages of the implementation, including planning, implementation design, and project management. From an IT standpoint, the implementation focused on two separate manufacturing units: Retail Manufacturing and Home & Office Manufacturing. They spread the implementation across 16 Retail sites, as well as eight Home & Office sites, and integrated them with corporate headquarters.
Operational Impact
Related Case Studies.
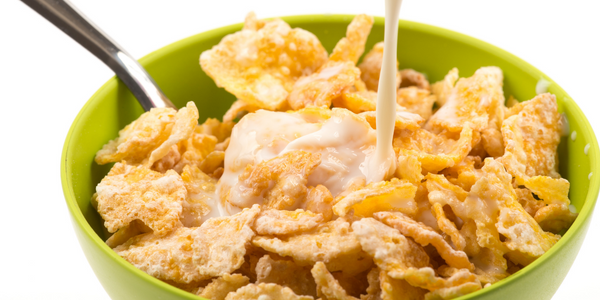
Case Study
The Kellogg Company
Kellogg keeps a close eye on its trade spend, analyzing large volumes of data and running complex simulations to predict which promotional activities will be the most effective. Kellogg needed to decrease the trade spend but its traditional relational database on premises could not keep up with the pace of demand.
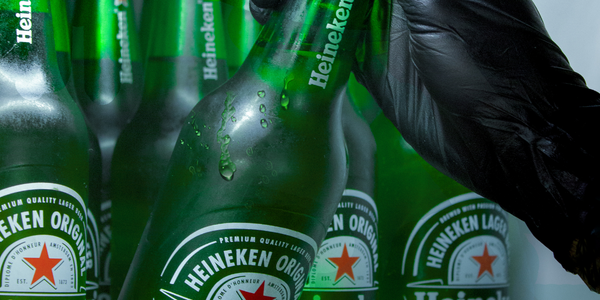
Case Study
HEINEKEN Uses the Cloud to Reach 10.5 Million Consumers
For 2012 campaign, the Bond promotion, it planned to launch the campaign at the same time everywhere on the planet. That created unprecedented challenges for HEINEKEN—nowhere more so than in its technology operation. The primary digital content for the campaign was a 100-megabyte movie that had to play flawlessly for millions of viewers worldwide. After all, Bond never fails. No one was going to tolerate a technology failure that might bruise his brand.Previously, HEINEKEN had supported digital media at its outsourced datacenter. But that datacenter lacked the computing resources HEINEKEN needed, and building them—especially to support peak traffic that would total millions of simultaneous hits—would have been both time-consuming and expensive. Nor would it have provided the geographic reach that HEINEKEN needed to minimize latency worldwide.
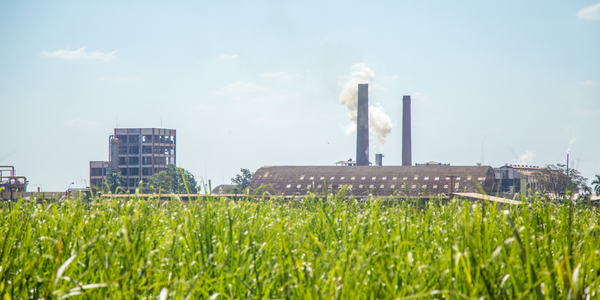
Case Study
Energy Management System at Sugar Industry
The company wanted to use the information from the system to claim under the renewable energy certificate scheme. The benefit to the company under the renewable energy certificates is Rs 75 million a year. To enable the above, an end-to-end solution for load monitoring, consumption monitoring, online data monitoring, automatic meter data acquisition which can be exported to SAP and other applications is required.
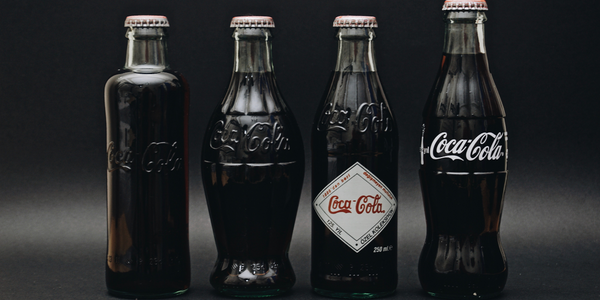
Case Study
Coca Cola Swaziland Conco Case Study
Coco Cola Swaziland, South Africa would like to find a solution that would enable the following results: - Reduce energy consumption by 20% in one year. - Formulate a series of strategic initiatives that would enlist the commitment of corporate management and create employee awareness while helping meet departmental targets and investing in tools that assist with energy management. - Formulate a series of tactical initiatives that would optimize energy usage on the shop floor. These would include charging forklifts and running cold rooms only during off-peak periods, running the dust extractors only during working hours and basing lights and air-conditioning on someone’s presence. - Increase visibility into the factory and other processes. - Enable limited, non-intrusive control functions for certain processes.
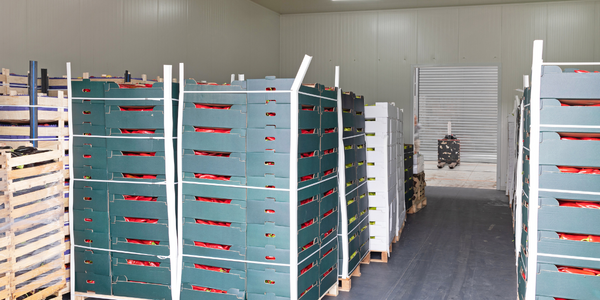
Case Study
Temperature Monitoring for Restaurant Food Storage
When it came to implementing a solution, Mr. Nesbitt had an idea of what functionality that he wanted. Although not mandated by Health Canada, Mr. Nesbitt wanted to ensure quality control issues met the highest possible standards as part of his commitment to top-of-class food services. This wish list included an easy-to use temperature-monitoring system that could provide a visible display of the temperatures of all of his refrigerators and freezers, including historical information so that he could review the performance of his equipment. It also had to provide alert notification (but email alerts and SMS text message alerts) to alert key staff in the event that a cooling system was exceeding pre-set warning limits.
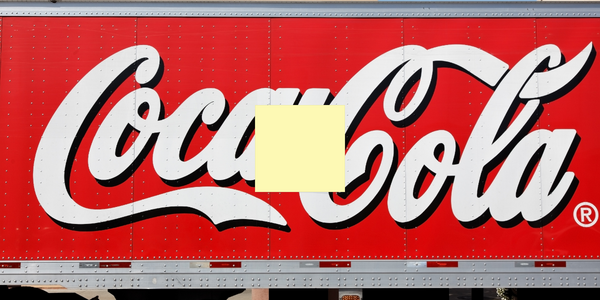
Case Study
Coca-Cola Refreshments, U.S.
Coca-Cola Refreshments owns and manages Coca-Cola branded refrigerators in retail establishments. Legacy systems were used to locate equipment information by logging onto multiple servers which took up to 8 hours to update information on 30-40 units. The company had no overall visibility into equipment status or maintenance history.