Download PDF
Kruitbosch Halves its Error Rate, Speeds Up Orders and Increases Productivity by 30% with Honeywell’s Vocollect Voice Solutions
Technology Category
- Functional Applications - Inventory Management Systems
- Functional Applications - Warehouse Management Systems (WMS)
Applicable Industries
- Consumer Goods
- Retail
Applicable Functions
- Logistics & Transportation
- Warehouse & Inventory Management
Use Cases
- Inventory Management
- Predictive Replenishment
- Warehouse Automation
Services
- System Integration
- Training
The Challenge
The pressure on suppliers for fast and accurate customer service is constantly increasing. An order placed today means delivery for tomorrow. Such delivery terms can have major consequences for suppliers. This was indeed the case for Kruitbosch, a leading bicycle supplier in The Netherlands and Belgium. As well as supplying the well-known bicycle brand ‘Cortina’, Kruitbosch also supplies bicycle parts and accessories to store and direct-to-consumer. In order to improve their service levels, they opted for a VocollectTM voice solution for their picking process.
About The Customer
Kruitbosch is a leading bicycle supplier in The Netherlands and Belgium, known for its well-known bicycle brand ‘Cortina’. The company also supplies bicycle parts and accessories to both stores and direct-to-consumer markets. With a strong reputation in the cycling industry, Kruitbosch has been committed to providing high-quality products and exceptional customer service. The company operates in a highly competitive market where fast and accurate order fulfillment is crucial. To maintain its competitive edge and meet the growing demands of its customers, Kruitbosch continuously seeks innovative solutions to enhance its operational efficiency and service levels.
The Solution
Kruitbosch implemented Honeywell’s Vocollect Voice Solutions to streamline their picking process. Before the introduction of Vocollect voice, employees had to pick, audit, pack, and prepare orders for dispatch. The new system eliminated the need for auditing, reducing error rates to less than 0.05%. Additionally, the packing and dispatch preparation processes were merged into a single step, cutting down the number of processes from four to two. Vocollect voice also enabled workers to pick up to 16 concurrent orders, a significant improvement from the previous system where they could only pick a maximum of three at a time. This change led to a 30% increase in overall employee productivity, allowing more tasks to be completed with the same number of people. To ensure a smooth transition, Kruitbosch involved its employees early in the implementation process. Small working groups were formed to decide on voice commands and other system features, which helped employees feel more comfortable and positive about the new system.
Operational Impact
Quantitative Benefit
Related Case Studies.
.png)
Case Study
Improving Vending Machine Profitability with the Internet of Things (IoT)
The vending industry is undergoing a sea change, taking advantage of new technologies to go beyond just delivering snacks to creating a new retail location. Intelligent vending machines can be found in many public locations as well as company facilities, selling different types of goods and services, including even computer accessories, gold bars, tickets, and office supplies. With increasing sophistication, they may also provide time- and location-based data pertaining to sales, inventory, and customer preferences. But at the end of the day, vending machine operators know greater profitability is driven by higher sales and lower operating costs.
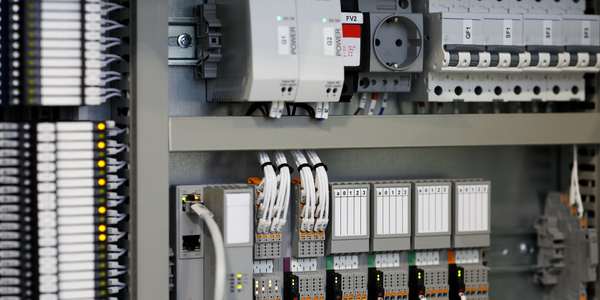
Case Study
Improving Production Line Efficiency with Ethernet Micro RTU Controller
Moxa was asked to provide a connectivity solution for one of the world's leading cosmetics companies. This multinational corporation, with retail presence in 130 countries, 23 global braches, and over 66,000 employees, sought to improve the efficiency of their production process by migrating from manual monitoring to an automatic productivity monitoring system. The production line was being monitored by ABB Real-TPI, a factory information system that offers data collection and analysis to improve plant efficiency. Due to software limitations, the customer needed an OPC server and a corresponding I/O solution to collect data from additional sensor devices for the Real-TPI system. The goal is to enable the factory information system to more thoroughly collect data from every corner of the production line. This will improve its ability to measure Overall Equipment Effectiveness (OEE) and translate into increased production efficiencies. System Requirements • Instant status updates while still consuming minimal bandwidth to relieve strain on limited factory networks • Interoperable with ABB Real-TPI • Small form factor appropriate for deployment where space is scarce • Remote software management and configuration to simplify operations
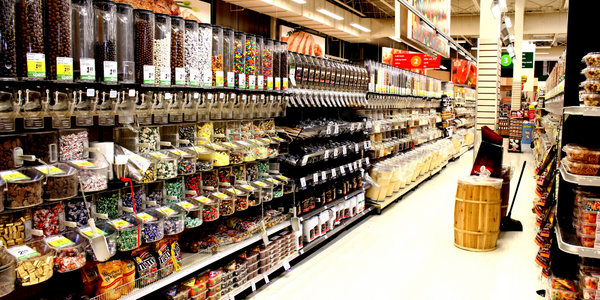
Case Study
How Sirqul’s IoT Platform is Crafting Carrefour’s New In-Store Experiences
Carrefour Taiwan’s goal is to be completely digital by end of 2018. Out-dated manual methods for analysis and assumptions limited Carrefour’s ability to change the customer experience and were void of real-time decision-making capabilities. Rather than relying solely on sales data, assumptions, and disparate systems, Carrefour Taiwan’s CEO led an initiative to find a connected IoT solution that could give the team the ability to make real-time changes and more informed decisions. Prior to implementing, Carrefour struggled to address their conversion rates and did not have the proper insights into the customer decision-making process nor how to make an immediate impact without losing customer confidence.
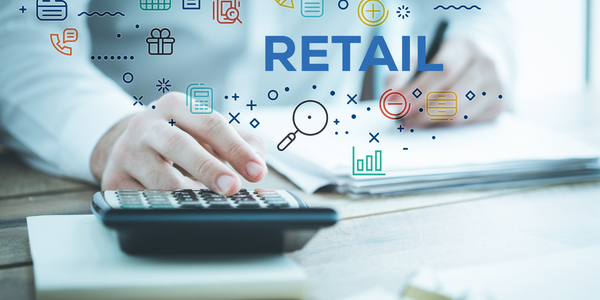
Case Study
Digital Retail Security Solutions
Sennco wanted to help its retail customers increase sales and profits by developing an innovative alarm system as opposed to conventional connected alarms that are permanently tethered to display products. These traditional security systems were cumbersome and intrusive to the customer shopping experience. Additionally, they provided no useful data or analytics.