Download PDF
Large Automotive Manufacturer Integrates eFlex Vision with Cognex Cameras to Optimize Vision Inspection System, Improve Part Quality and Reduce Warranty Costs
Technology Category
- Analytics & Modeling - Real Time Analytics
- Application Infrastructure & Middleware - Data Exchange & Integration
- Sensors - Camera / Video Systems
Applicable Industries
- Automotive
Applicable Functions
- Discrete Manufacturing
- Quality Assurance
Use Cases
- Machine Condition Monitoring
- Predictive Maintenance
- Visual Quality Detection
Services
- Software Design & Engineering Services
- System Integration
The Challenge
The customer, a global automobile manufacturer, was facing challenges with their existing transmission manufacturing process. The detailed nature of automotive transmission manufacturing and the high cost of errors made it crucial to ensure high levels of quality and minimize warranty costs. Prior to implementing a vision inspection system, the transmission line and all previous assembly lines were managed in a manner that was inefficient and costly. Images were stored on 50 PCs scattered throughout the plant, requiring engineers to visit each storage area to retrieve images associated to a particular serial number. This incurred excessive PC life-cycle cost and labor due to the initial investment, and ongoing OS patches, virus updates and hardware failures. The PCs failed to integrate and store images reliably, resulting in lost images. The system also lacked diagnostic capabilities, such as alerts when quality was degrading, as well as data and reporting capabilities.
About The Customer
The customer is a global automobile manufacturer with a 2 million sq. ft. transmission manufacturing plant and 2,000 employees. The company invested $323 million into its new 6-speed, front-wheel drive transmission assembly line. Automotive transmissions are very complex assemblies that can be rendered defective by a single faulty component or incorrect assembly operation. The cost of repairing and replacing a defective transmission can easily run to hundreds of times the cost of the component that caused the problem. This explains why transmission plants have traditionally deployed hundreds of inspectors who were assigned to manually view each of the many parts and assembly operations involved in building the final product.
The Solution
To address the challenges, improve quality and reduce warranty costs, the transmission plant incorporated eFlex Vision to create an integrated environment for managing and retrieving process images. This transmission assembly line now has over 300 Cognex cameras and uses eFlex Vision to process and store approximately 200,000 images per day (with associated data for each part in every stage of the assembly process) at roughly 200 images per minute, into a central system that includes numerous search capabilities. There is a tool inside the application to facilitate an automated standardized file naming convention for every camera. The naming convention facilitates the user to easily sort and search through millions of images to find any part number from any station within seconds. The solution by eFlex Systems included a Dell EqualLogic storage server with 12 network interface cards and 48 2 Terabyte hard disk drives providing 71 Terabytes net storage space. The plant floor cameras were all modified within two days to FTP files to the eFlex Vision server.
Operational Impact
Quantitative Benefit
Related Case Studies.
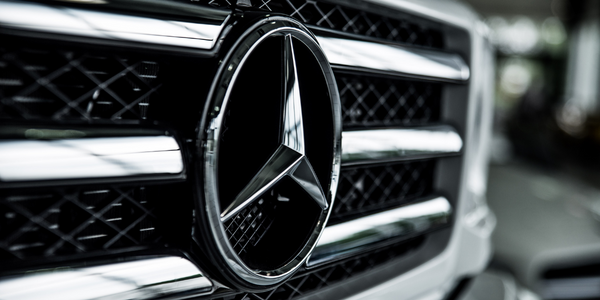
Case Study
Integral Plant Maintenance
Mercedes-Benz and his partner GAZ chose Siemens to be its maintenance partner at a new engine plant in Yaroslavl, Russia. The new plant offers a capacity to manufacture diesel engines for the Russian market, for locally produced Sprinter Classic. In addition to engines for the local market, the Yaroslavl plant will also produce spare parts. Mercedes-Benz Russia and his partner needed a service partner in order to ensure the operation of these lines in a maintenance partnership arrangement. The challenges included coordinating the entire maintenance management operation, in particular inspections, corrective and predictive maintenance activities, and the optimizing spare parts management. Siemens developed a customized maintenance solution that includes all electronic and mechanical maintenance activities (Integral Plant Maintenance).
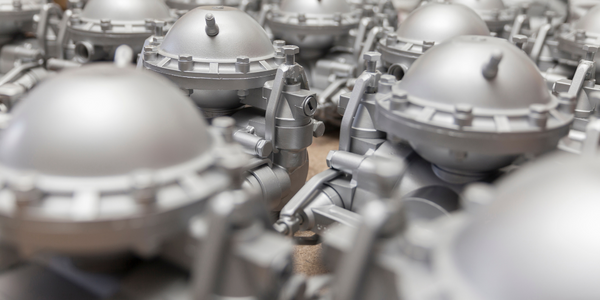
Case Study
Monitoring of Pressure Pumps in Automotive Industry
A large German/American producer of auto parts uses high-pressure pumps to deburr machined parts as a part of its production and quality check process. They decided to monitor these pumps to make sure they work properly and that they can see any indications leading to a potential failure before it affects their process.