Download PDF
Leveraging IoT in High-Temperature Biomass Reformation
Technology Category
- Sensors - Infrared Sensors
- Sensors - Thermal Conductivity Sensors
Applicable Industries
- Renewable Energy
- Transportation
Applicable Functions
- Logistics & Transportation
Use Cases
- Last Mile Delivery
- Transportation Simulation
The Challenge
A biofuels company based in Longmont, CO, aimed to be a leader in converting woody biomass into drop-in transportation fuels. However, they faced several challenges in the high-temperature bioreforming process. One of the key challenges was the small-scale gas-solid separator classifier, which was designed to separate particles from gases by size from a product stream for subsequent analysis. Another challenge was determining a material’s resistance to thermal stress. The company hypothesized that the rapid insertion of a cold lance into a hot chamber would create a stress spike sufficient to break the specimen. Furthermore, the biomass conversion rates depended on an evolving particle size distribution, particle shape, and porosity. The physical properties used in CFD depended on temperature, pressure, and composition.
About The Customer
The customer in this case study is a biofuels company based in Longmont, Colorado. The company's primary goal is to become a leader in the conversion of woody biomass into drop-in transportation fuels. They are committed to leveraging advanced technologies to overcome the challenges associated with high-temperature bioreforming. The company is focused on improving the efficiency and effectiveness of their processes, particularly in the areas of gas-solid separation, thermal stress resistance, and biomass conversion rates. They are also interested in exploring partnerships with technology providers to enhance their capabilities and achieve their objectives.
The Solution
The company utilized Altair Technologies, specifically AcuSolve and OptiStruct, to address these challenges. AcuSolve was used for one-way coupling finite-massed particle tracing, sliding-deforming mesh, dynamic LES turbulence model, conjugate heat transfer, and variable physical properties. OptiStruct was used for thermal stress analysis. The company also used acuProj with elemental interpolation to map transient temperature fields from CFD to an FEA mesh of the specimen. Additionally, they partnered with LOGESoft, the creator of the DARS kinetic plug-in to Star CCM+, to add gas-solid chemistry to their solver. LOGESoft was used to estimate temperature-dependent density, viscosity, and enthalpy for the fluid. Altair’s AcuSolve Spalart-Allmaras turbulence, conjugate heat transfer, surface-to-surface radiation, user Rosseland radiation model for particle-laden fluid, and OptiStruct for thermal stress were used to model thermal stresses in a laboratory bioreformer.
Operational Impact
Quantitative Benefit
Related Case Studies.
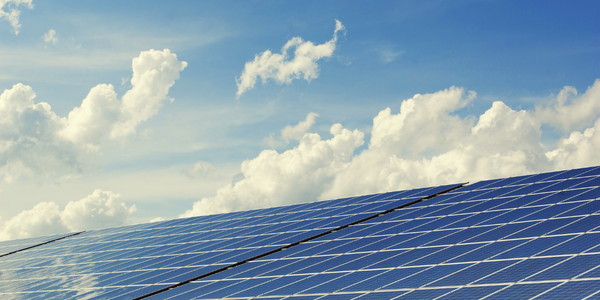
Case Study
Remote Monitoring & Predictive Maintenance App for a Solar Energy System
The maintenance & tracking of various modules was an overhead for the customer due to the huge labor costs involved. Being an advanced solar solutions provider, they wanted to ensure early detection of issues and provide the best-in-class customer experience. Hence they wanted to automate the whole process.
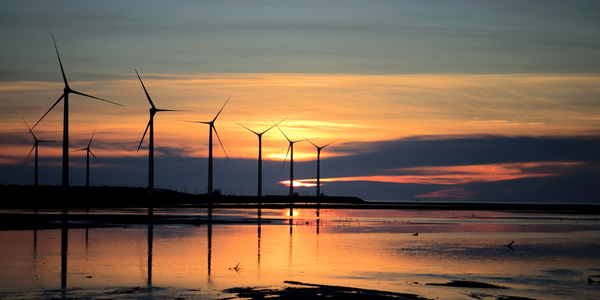
Case Study
Vestas: Turning Climate into Capital with Big Data
Making wind a reliable source of energy depends greatly on the placement of the wind turbines used to produce electricity. Turbulence is a significant factor as it strains turbine components, making them more likely to fail. Vestas wanted to pinpoint the optimal location for wind turbines to maximize power generation and reduce energy costs.
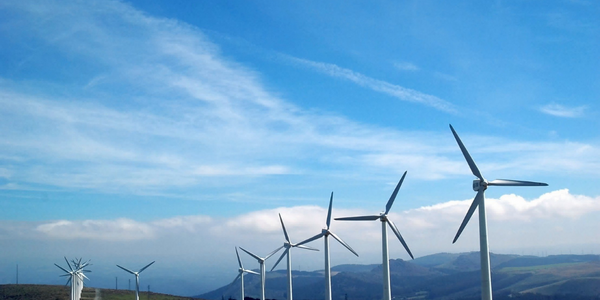
Case Study
Siemens Wind Power
Wind provides clean, renewable energy. The core concept is simple: wind turbines spin blades to generate power. However, today's systems are anything but simple. Modern wind turbines have blades that sweep a 120 meter circle, cost more than 1 million dollars and generate multiple megawatts of power. Each turbine may include up to 1,000 sensors and actuators – integrating strain gages, bearing monitors and power conditioning technology. The turbine can control blade speed and power generation by altering the blade pitch and power extraction. Controlling the turbine is a sophisticated job requiring many cooperating processors closing high-speed loops and implementing intelligent monitoring and optimization algorithms. But the real challenge is integrating these turbines so that they work together. A wind farm may include hundreds of turbines. They are often installed in difficult-to-access locations at sea. The farm must implement a fundamentally and truly distributed control system. Like all power systems, the goal of the farm is to match generation to load. A farm with hundreds of turbines must optimize that load by balancing the loading and generation across a wide geography. Wind, of course, is dynamic. Almost every picture of a wind farm shows a calm sea and a setting sun. But things get challenging when a storm goes through the wind farm. In a storm, the control system must decide how to take energy out of gusts to generate constant power. It must intelligently balance load across many turbines. And a critical consideration is the loading and potential damage to a half-billion-dollar installed asset. This is no environment for a slow or undependable control system. Reliability and performance are crucial.
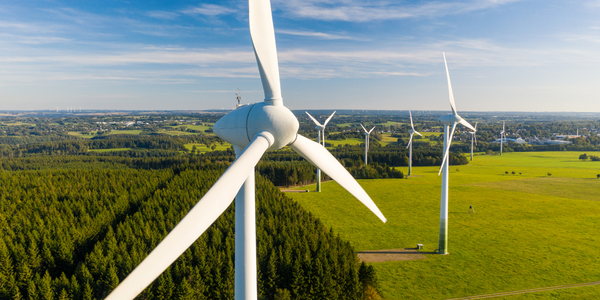
Case Study
Remote Monitoring and Control for a Windmill Generator
As concerns over global warming continue to grow, green technologies are becoming increasingly popular. Wind turbine companies provide an excellent alternative to burning fossil fuels by harnessing kinetic energy from the wind and converting it into electricity. A typical wind farm may include over 80 wind turbines so efficient and reliable networks to manage and control these installations are imperative. Each wind turbine includes a generator and a variety of serial components such as a water cooler, high voltage transformer, ultrasonic wind sensors, yaw gear, blade bearing, pitch cylinder, and hub controller. All of these components are controlled by a PLC and communicate with the ground host. Due to the total integration of these devices into an Ethernet network, one of our customers in the wind turbine industry needed a serial-to-Ethernet solution that can operate reliably for years without interruption.
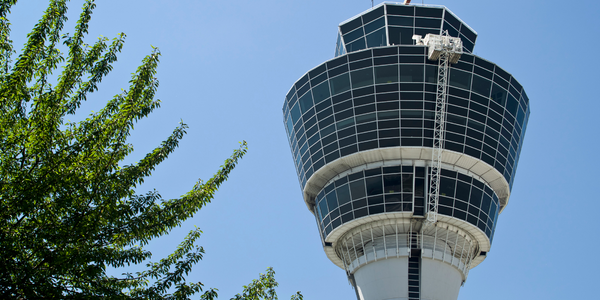
Case Study
Airport SCADA Systems Improve Service Levels
Modern airports are one of the busiest environments on Earth and rely on process automation equipment to ensure service operators achieve their KPIs. Increasingly airport SCADA systems are being used to control all aspects of the operation and associated facilities. This is because unplanned system downtime can cost dearly, both in terms of reduced revenues and the associated loss of customer satisfaction due to inevitable travel inconvenience and disruption.
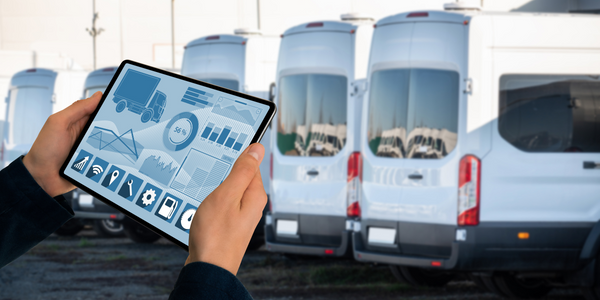
Case Study
IoT-based Fleet Intelligence Innovation
Speed to market is precious for DRVR, a rapidly growing start-up company. With a business model dependent on reliable mobile data, managers were spending their lives trying to negotiate data roaming deals with mobile network operators in different countries. And, even then, service quality was a constant concern.