Download PDF
Leveraging Topology Optimization and Laser Additive Manufacturing for Lightweight Structures
Technology Category
- Sensors - Lidar & Lazer Scanners
Applicable Industries
- Aerospace
- Automotive
Applicable Functions
- Product Research & Development
Use Cases
- Additive Manufacturing
- Rapid Prototyping
Services
- System Integration
- Training
The Challenge
The Laser Zentrum Nord (LZN) and the Technical University Hamburg-Harburg (TUHH) were seeking ways to improve the design and optimization methods for components made with laser additive manufacturing methods. The challenge was to develop structures that are strong yet light, similar to naturally occurring biological structures like bones. The research project, TiLight, aimed to combine innovative design methods with new manufacturing capabilities to economically manufacture lightweight components from the material TiAl6V4, a high-strength titanium alloy. The aerospace industry was the primary focus of the project, where lighter components could lead to higher load capacity or range for aircraft. A standard retaining element in aircraft, a bracket, was selected as a test object for the project.
About The Customer
The Laser Zentrum Nord (LZN) and the Technical University Hamburg-Harburg (TUHH) were the primary entities involved in the research project. LZN was founded in 2009 to support knowledge and technology transfer from fundamental research to industrial application. It works in close cooperation with the Institute of Laser and System Technologies (iLAS) of the Hamburg University of Technology (TUHH). The research project was also supported by funding from the BMBF (German Federal Ministry of Education and Research). Premium Aerotec (PAG), a supplier in the aerospace industry, served as the project’s industrial partner.
The Solution
The solution involved using Altair's HyperWorks, OptiStruct, and Simulation Driven Design Process. The TiAl6V4 material was taken into account, and a customized process chain for the laser additive method was developed. The optimization tool OptiStruct was used to create the fundamental optimized structure. These structures were then compared and adapted to biological examples from nature before a final numerical verification of the final geometry was performed. The HyperWorks Suite was used in the concept phase of component design, providing integrated solutions for modeling, analysis, optimization, visualization, reporting, and data management. The proposed design was then refined with a CAD tool and the final design was numerically verified with OptiStruct.
Operational Impact
Quantitative Benefit
Related Case Studies.
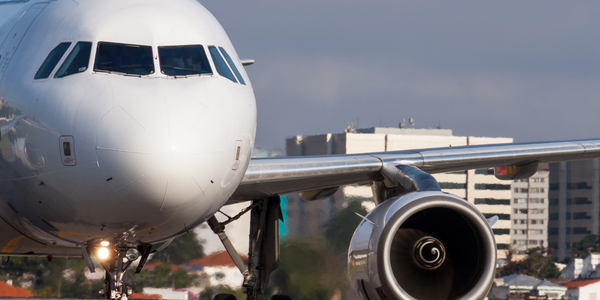
Case Study
Airbus Soars with Wearable Technology
Building an Airbus aircraft involves complex manufacturing processes consisting of thousands of moving parts. Speed and accuracy are critical to business and competitive advantage. Improvements in both would have high impact on Airbus’ bottom line. Airbus wanted to help operators reduce the complexity of assembling cabin seats and decrease the time required to complete this task.
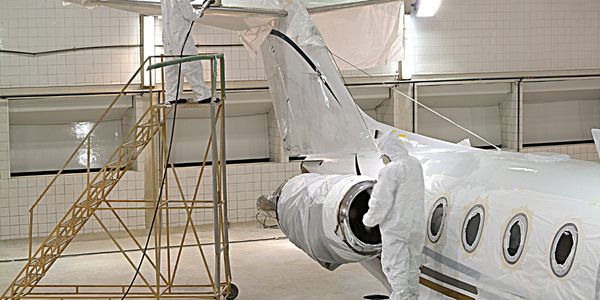
Case Study
Aircraft Predictive Maintenance and Workflow Optimization
First, aircraft manufacturer have trouble monitoring the health of aircraft systems with health prognostics and deliver predictive maintenance insights. Second, aircraft manufacturer wants a solution that can provide an in-context advisory and align job assignments to match technician experience and expertise.
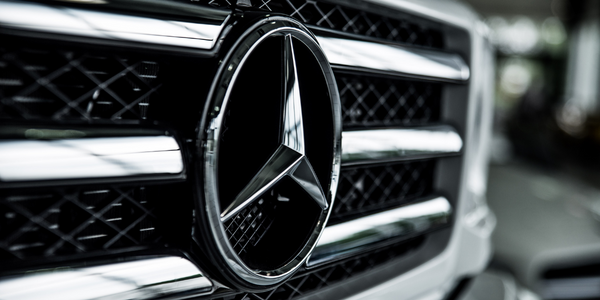
Case Study
Integral Plant Maintenance
Mercedes-Benz and his partner GAZ chose Siemens to be its maintenance partner at a new engine plant in Yaroslavl, Russia. The new plant offers a capacity to manufacture diesel engines for the Russian market, for locally produced Sprinter Classic. In addition to engines for the local market, the Yaroslavl plant will also produce spare parts. Mercedes-Benz Russia and his partner needed a service partner in order to ensure the operation of these lines in a maintenance partnership arrangement. The challenges included coordinating the entire maintenance management operation, in particular inspections, corrective and predictive maintenance activities, and the optimizing spare parts management. Siemens developed a customized maintenance solution that includes all electronic and mechanical maintenance activities (Integral Plant Maintenance).
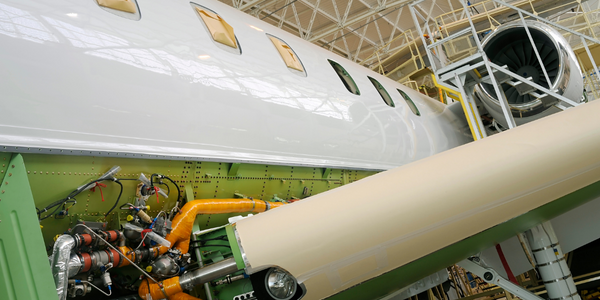
Case Study
Aerospace & Defense Case Study Airbus
For the development of its new wide-body aircraft, Airbus needed to ensure quality and consistency across all internal and external stakeholders. Airbus had many challenges including a very aggressive development schedule and the need to ramp up production quickly to satisfy their delivery commitments. The lack of communication extended design time and introduced errors that drove up costs.