Download PDF
Lin Engineering uses cloud-based quality control to monitor overseas facility
Technology Category
- Analytics & Modeling - Predictive Analytics
- Application Infrastructure & Middleware - Data Visualization
- Functional Applications - Remote Monitoring & Control Systems
Applicable Industries
- Aerospace
- Semiconductors
Applicable Functions
- Quality Assurance
Use Cases
- Predictive Maintenance
- Process Control & Optimization
- Remote Asset Management
Services
- Cloud Planning, Design & Implementation Services
- System Integration
The Challenge
With a quality policy incorporating continuous improvement and the 4.5 Sigma Way, Lin Engineering has long established itself as a manufacturer of high-quality products. As it expanded on its 4.5 Sigma initiatives, Lin Engineering realized that it would need a Statistical Process Control (SPC) system that would allow for real-time quality monitoring and process control. The company’s overseas operations created an additional challenge; Lin Engineering needed to ensure that products produced in its facility in China were without defects. If a product failed inspection after it was received in the U.S., it was costly to ship it back to China. Plus, Lin Engineering wanted quality analytics to verify that each product meets a stringent quality standard to strengthen the company’s leading market position and drive new revenue.
About The Customer
Lin Engineering is a U.S. manufacturer of hybrid step motors that focuses on leading technology designs, high-quality products, and customer service excellence. Founded in 1987, Lin Engineering began as a consulting company specializing in step motor applications. Today, it is the largest manufacturer of the best 0.9-degree step motor in the motion control industry. Headquartered in Morgan Hill, California, with a second location in Nanjing, China, Lin Engineering offers a breadth of products consisting of stepper motors, integrated stepper motors, stepper motor drivers and controllers, brushless DC motors, encoders, gearheads, and lead screws. The manufacturer serves a broad range of markets including aerospace and defense, automation and packaging, medical, printing and engraving, security and surveillance systems, semiconductors, and solar and green technology.
The Solution
In its search for an SPC provider, Lin Engineering concluded that InfinityQS®, the global authority on real-time Manufacturing Intelligence and enterprise quality, was the best fit. InfinityQS ProFicientTM, a Manufacturing Intelligence hub powered by a centralized SPC analysis engine, offered Lin Engineering a complete package that included both basic and advanced analytical tools and tracking mechanisms. In order to integrate information from its overseas facility, Lin Engineering adopted ProFicient’s cloud-based deployment, ProFicient On Demand. With ProFicient On Demand, Lin Engineering can monitor quality at its China location in real time and access information anywhere, whenever it is needed. For example, when an out-of-spec issue occurs in its China facility, Lin Engineering instantly receives an automated email alert, allowing operators to take immediate corrective action – long before the product is shipped.
Operational Impact
Quantitative Benefit
Related Case Studies.
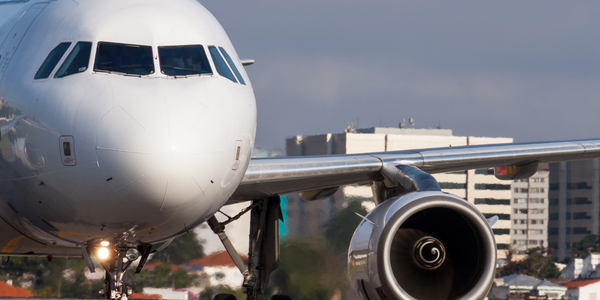
Case Study
Airbus Soars with Wearable Technology
Building an Airbus aircraft involves complex manufacturing processes consisting of thousands of moving parts. Speed and accuracy are critical to business and competitive advantage. Improvements in both would have high impact on Airbus’ bottom line. Airbus wanted to help operators reduce the complexity of assembling cabin seats and decrease the time required to complete this task.
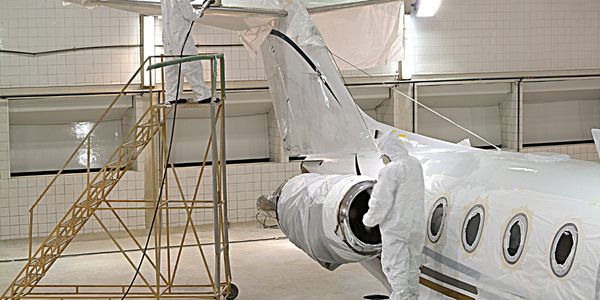
Case Study
Aircraft Predictive Maintenance and Workflow Optimization
First, aircraft manufacturer have trouble monitoring the health of aircraft systems with health prognostics and deliver predictive maintenance insights. Second, aircraft manufacturer wants a solution that can provide an in-context advisory and align job assignments to match technician experience and expertise.
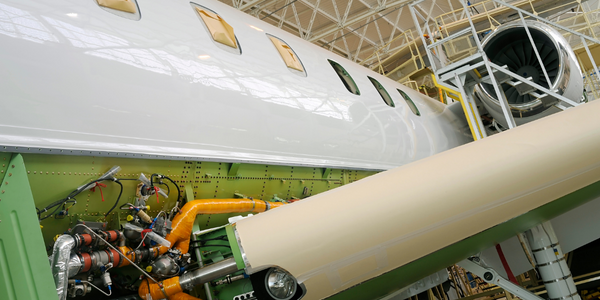
Case Study
Aerospace & Defense Case Study Airbus
For the development of its new wide-body aircraft, Airbus needed to ensure quality and consistency across all internal and external stakeholders. Airbus had many challenges including a very aggressive development schedule and the need to ramp up production quickly to satisfy their delivery commitments. The lack of communication extended design time and introduced errors that drove up costs.
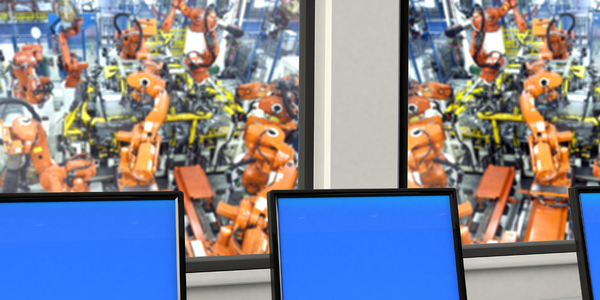
Case Study
KINESYS Semiconductor Factory Automation Software
KINESYS Software provides both Integrated Device Manufacturer (IDM) and Original Equipment Manufacturer (OEM) customers world-class software products and solutions for advanced wafer and device traceability and process management. KINESYS offers state of the art database technology with a core focus on SEMI standards. KINESYS’ challenge was to make back-end processing failure-free and easy to use for clients while supporting licensing models more adaptable to changing industry needs.
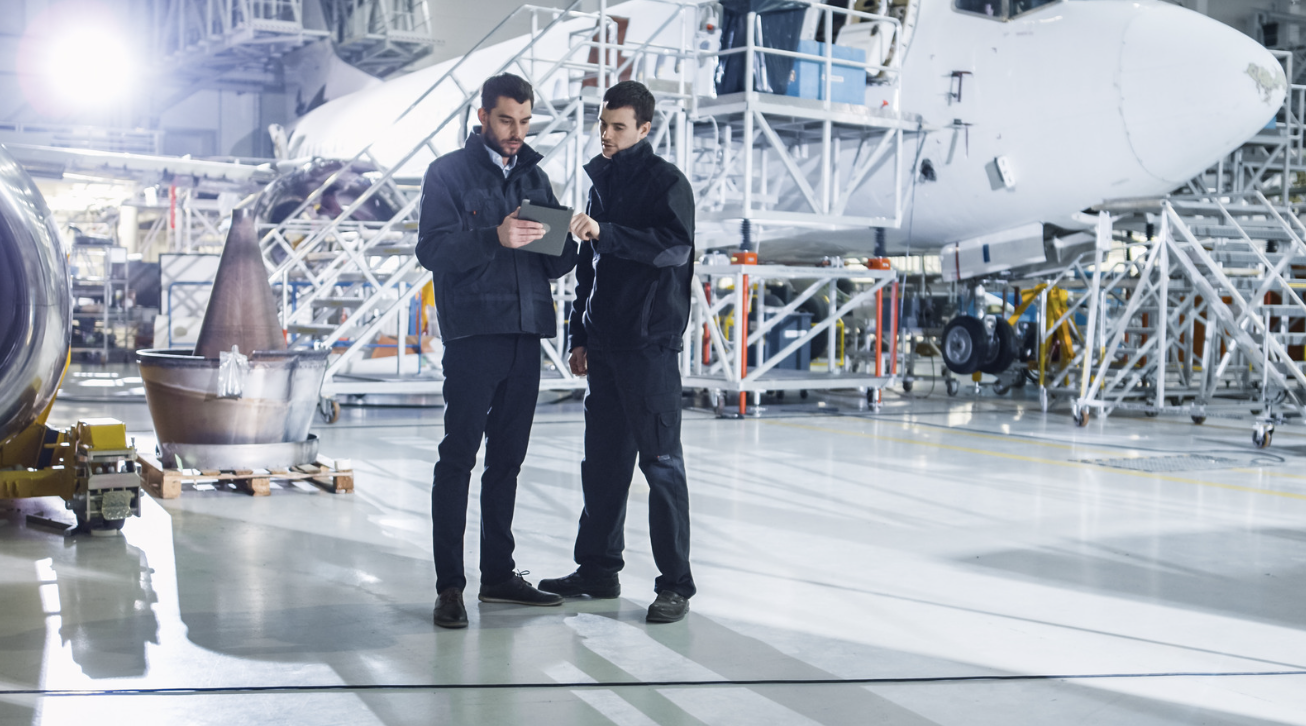
Case Study
Developing Smart Tools for the Airbus Factory
Manufacturing and assembly of aircraft, which involves tens of thousands of steps that must be followed by the operators, and a single mistake in the process could cost hundreds of thousands of dollars to fix, makes the room for error very small.