Download PDF
Lionbridge’s Revsourcesm Streamlines Drafting for the World’s Leading International Gas Turbine Manufacturer
Technology Category
- Functional Applications - Enterprise Resource Planning Systems (ERP)
- Functional Applications - Product Lifecycle Management Systems (PLM)
Applicable Industries
- Aerospace
Applicable Functions
- Business Operation
- Product Research & Development
Use Cases
- Process Control & Optimization
- Remote Collaboration
Services
- Software Design & Engineering Services
- System Integration
The Challenge
A global aerospace and manufacturing leader sought to eliminate inefficiencies in its drafting change order process. Change orders processed through the existing model were time-consuming and irregular and required costly ad hoc efforts on the part of technical documentation professionals and engineers. With so much time spent administrating change orders, technical documentation professionals and engineers had little time to focus on their core responsibilities. With a clear picture of the problem, senior management set out to fix it. The decision was made to outsource the drafting change order process to a select group of 12 qualified vendors, and eventually narrow down to two. The expectation was that, through outsourcing, the company would reduce expenses by leveraging locally managed, globally operated labor resources, while freeing up domestic technical documentation professionals and engineers resources. To their surprise, many of the vendors were not able to deliver the promised cost and time savings, requiring endless training and extensive support. Of the 12, only Lionbridge remains, ranking highest in performance with impressive adaptability and earning an A+ through its unique RevSourceSM process.
About The Customer
The customer is a global leader in the aerospace and manufacturing industry, specifically focusing on gas turbine manufacturing. This company is renowned for its innovative engineering solutions and has a significant international presence. The company faced challenges in its drafting change order process, which was time-consuming and inefficient. The existing model required costly ad hoc efforts from technical documentation professionals and engineers, diverting their focus from core responsibilities. To address these inefficiencies, the company decided to outsource the drafting change order process, aiming to reduce expenses and free up internal resources. After evaluating 12 qualified vendors, the company found that only Lionbridge could meet their expectations, thanks to its unique RevSourceSM process.
The Solution
Lionbridge introduced its RevSourceSM process to streamline the drafting change order process for the gas turbine manufacturer. The RevSourceSM process is designed to support the entire change order process, allowing engineers to focus on actual engineering work. Lionbridge’s team of experts, including technical documentation professionals, engineers, technical writers, and project managers, provided a wide range of technical data revision services. The five-step RevSourceSM process breaks down the total percentage of work from start to finish, saving both time and money. The process includes writing engineering changes, permitting engineers and subject matter experts to review changes, packaging supporting documents, reviewing and checking work, and releasing completed changes into the customer's current system. Due to the success of Lionbridge’s handling of drafting projects, the gas turbine manufacturer expanded the contract to include technical writing services.
Operational Impact
Quantitative Benefit
Related Case Studies.
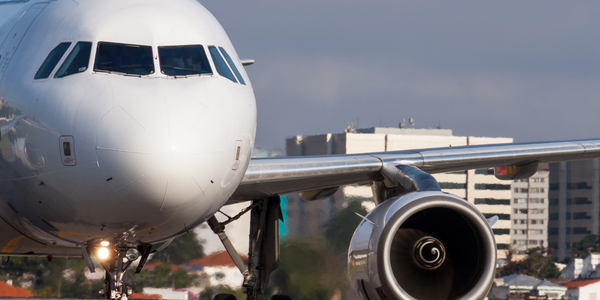
Case Study
Airbus Soars with Wearable Technology
Building an Airbus aircraft involves complex manufacturing processes consisting of thousands of moving parts. Speed and accuracy are critical to business and competitive advantage. Improvements in both would have high impact on Airbus’ bottom line. Airbus wanted to help operators reduce the complexity of assembling cabin seats and decrease the time required to complete this task.
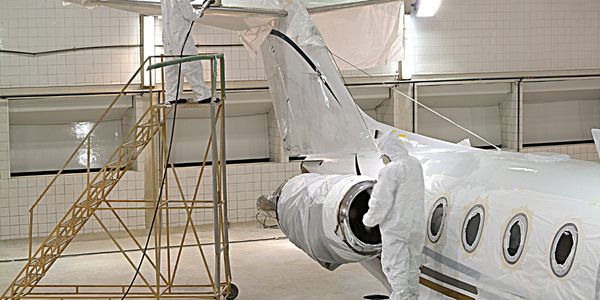
Case Study
Aircraft Predictive Maintenance and Workflow Optimization
First, aircraft manufacturer have trouble monitoring the health of aircraft systems with health prognostics and deliver predictive maintenance insights. Second, aircraft manufacturer wants a solution that can provide an in-context advisory and align job assignments to match technician experience and expertise.
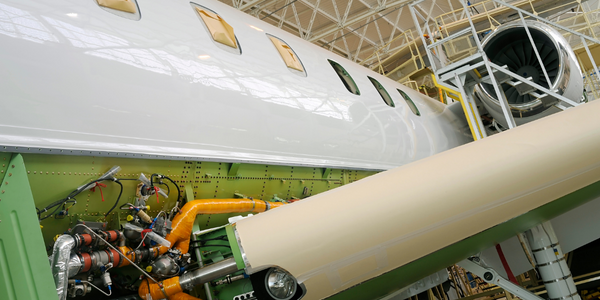
Case Study
Aerospace & Defense Case Study Airbus
For the development of its new wide-body aircraft, Airbus needed to ensure quality and consistency across all internal and external stakeholders. Airbus had many challenges including a very aggressive development schedule and the need to ramp up production quickly to satisfy their delivery commitments. The lack of communication extended design time and introduced errors that drove up costs.
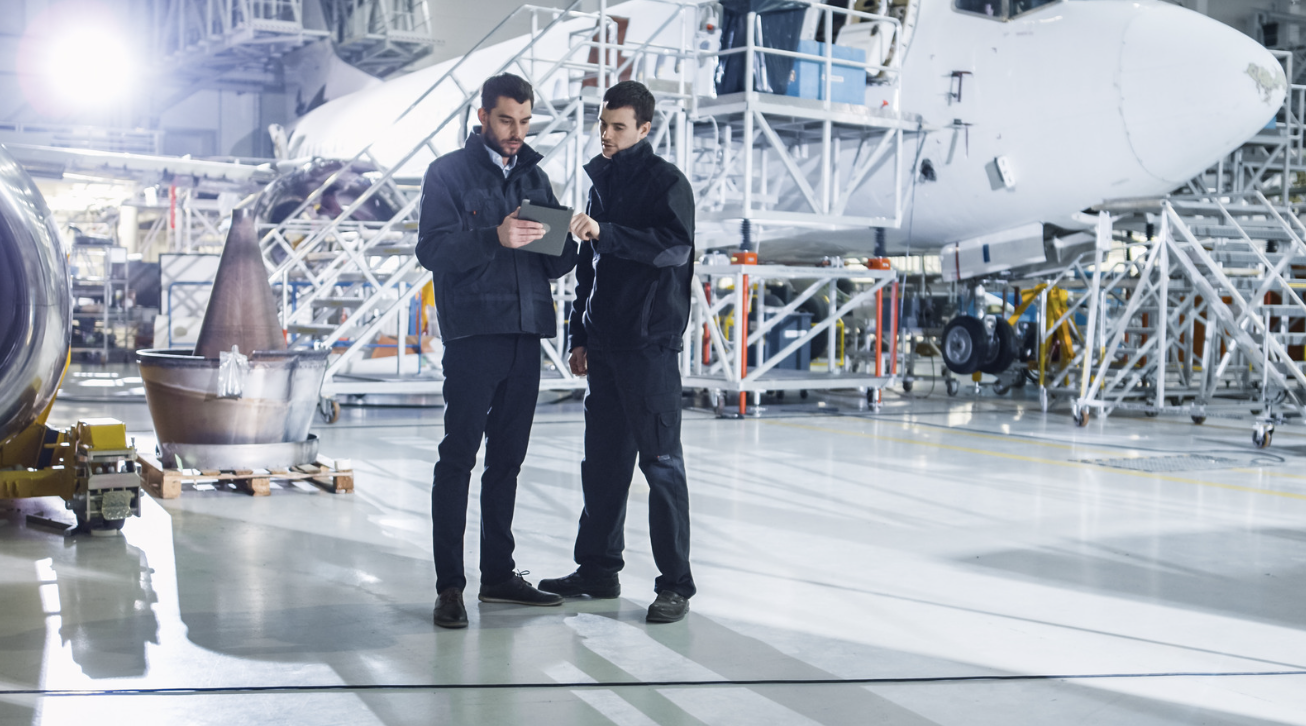
Case Study
Developing Smart Tools for the Airbus Factory
Manufacturing and assembly of aircraft, which involves tens of thousands of steps that must be followed by the operators, and a single mistake in the process could cost hundreds of thousands of dollars to fix, makes the room for error very small.
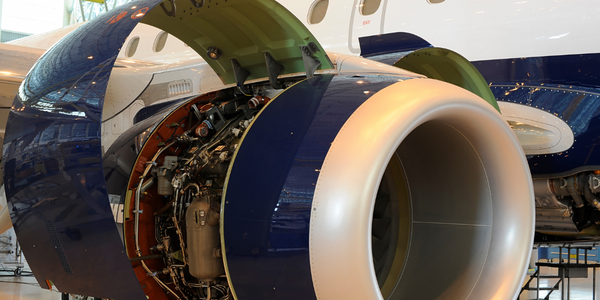
Case Study
Accelerate Production for Spirit AeroSystems
The manufacture and assembly of massive fuselage assemblies and other large structures generates a river of data. In fact, the bill of materials for a single fuselage alone can be millions of rows of data. In-house production processes and testing, as well as other manufacturers and customers created data flows that overwhelmed previous processes and information systems. Spirit’s customer base had grown substantially since their 2005 divestiture from Boeing, resulting in a $41 billion backlog of orders to fill. To address this backlog, meet increased customer demands and minimize additional capital investment, the company needed a way to improve throughput in the existing operational footprint. Spirit had a requirement from customers to increase fuselage production by 30%. To accomplish this goal, Spirit needed real-time information on its value chain and workflow. However, the two terabytes of data being pulled from their SAP ECC was unmanageable and overloaded their business warehouse. It had become time-consuming and difficult to pull aggregate data, disaggregate it for the needed information and then reassemble to create a report. During the 6-8 hours it took to build a report, another work shift (they run three per day) would have already taken place, thus the report content was out-of-date before it was ever delivered. As a result, supervisors often had to rely on manual efforts to provide charts, reports and analysis.