Download PDF
Lower costs and higher productivity through new truck trailer design
Applicable Industries
- Oil & Gas
Applicable Functions
- Logistics & Transportation
- Maintenance
Use Cases
- Fleet Management
- Predictive Maintenance
The Challenge
The customer was seeking third-party expertise to enhance their in-house garage operations. Element’s truck consulting team conducted a field study at several of the customer’s in-house garage shops and identified several issues. These included an excess of inventory parts, the absence of a tire policy, inconsistent use of the maintenance software system, varied training provided to mechanics, lack of centralized purchasing programs, absence of a preventive maintenance checklist leading to numerous errors, and discrepancies in safety practices.
About The Customer
The customer operates in the Oil & Gas industry, utilizing light and medium trucks, tractors, and trailers for service and delivery purposes. They were seeking ways to improve their in-house garage operations and were open to third-party expertise. The customer's fleet is spread across 34 locations, with a total of 700 vehicles in operation. The services they utilized included fuel, leasing, maintenance, and title, licensing & registration.
The Solution
Element’s truck consultants presented the customer with several recommendations to reduce costs and gain efficiencies. These included keeping only repetitive parts on hand, routinely checking tire pressure, consolidating vendors, enforcing the use of the current software system, ensuring consistent and required training for all mechanics, negotiating with vendors at the corporate level and mandating use in the field, implementing preventive maintenance checklists, and incorporating monthly safety meetings tied to OSHA.
Operational Impact
Quantitative Benefit
Related Case Studies.
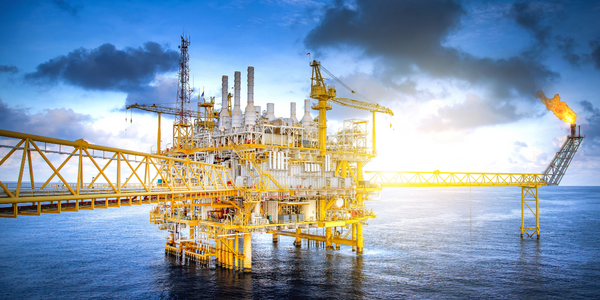
Case Study
Taking Oil and Gas Exploration to the Next Level
DownUnder GeoSolutions (DUG) wanted to increase computing performance by 5 to 10 times to improve seismic processing. The solution must build on current architecture software investments without sacrificing existing software and scale computing without scaling IT infrastructure costs.
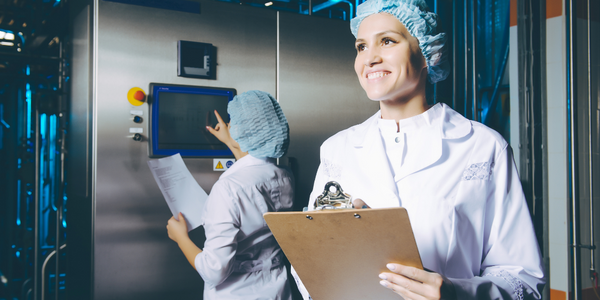
Case Study
Remote Wellhead Monitoring
Each wellhead was equipped with various sensors and meters that needed to be monitored and controlled from a central HMI, often miles away from the assets in the field. Redundant solar and wind generators were installed at each wellhead to support the electrical needs of the pumpstations, temperature meters, cameras, and cellular modules. In addition to asset management and remote control capabilities, data logging for remote surveillance and alarm notifications was a key demand from the customer. Terra Ferma’s solution needed to be power efficient, reliable, and capable of supporting high-bandwidth data-feeds. They needed a multi-link cellular connection to a central server that sustained reliable and redundant monitoring and control of flow meters, temperature sensors, power supply, and event-logging; including video and image files. This open-standard network needed to interface with the existing SCADA and proprietary network management software.
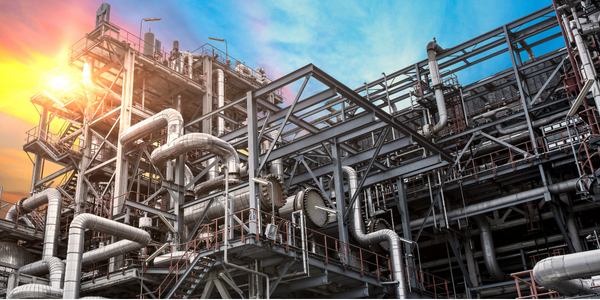
Case Study
Refinery Saves Over $700,000 with Smart Wireless
One of the largest petroleum refineries in the world is equipped to refine various types of crude oil and manufacture various grades of fuel from motor gasoline to Aviation Turbine Fuel. Due to wear and tear, eight hydrogen valves in each refinery were leaking, and each cost $1800 per ton of hydrogen vented. The plant also had leakage on nearly 30 flare control hydrocarbon valves. The refinery wanted a continuous, online monitoring system that could catch leaks early, minimize hydrogen and hydrocarbon production losses, and improve safety for maintenance.