Download PDF
Managed Services Model Supports 500+ Products
Technology Category
- Analytics & Modeling - Predictive Analytics
- Application Infrastructure & Middleware - Data Exchange & Integration
- Functional Applications - Enterprise Resource Planning Systems (ERP)
Applicable Industries
- Electronics
- Software
Applicable Functions
- Product Research & Development
- Quality Assurance
Use Cases
- Predictive Maintenance
- Process Control & Optimization
- Remote Asset Management
Services
- Software Design & Engineering Services
- System Integration
- Testing & Certification
The Challenge
The company experienced global growth for both its enterprise and personal technology products and support services. That same growth brought new pressures to the QA/testing systems, products groups, and their supporting vendors. Volatility in workloads, workflows, and resources led to increased product defect rates, inconsistent quality, and a talent gap. Based on history, quality, and capability, Lionbridge was selected to lead a process transformation that would help the company increase quality and reduce cost on a global scale.
About The Customer
This technology company is the global leader in printers and PCs. The company maintains its position and reputation for quality with a keen focus on innovation and excellence in engineering, design, and manufacturing. With over 60% of the annual revenue coming from outside of the US, including emerging markets, quality localization is critical to the global customer experience. In 1997, as the digital transformation began, the company chose Lionbridge to help reduce the cost of global testing services. With just 50 onsite testers, Lionbridge began a two-decade partnership that has grown to include hardware, firmware, and software testing needs as well as content development and localization.
The Solution
To meet the company’s targets, key aspects of QA/testing --resource management, processes, and technologies—needed to be optimized. Based on a deep understanding of the client, the Lionbridge team developed and implemented a managed services model designed to leverage the company’s global footprint, eliminate inefficiencies and improve productivity. The Blended Test Services Model combines onshore resource management, managed test services, dedicated near-site QA centers, and offshore delivery to deliver quality improvements, cost savings, and increased efficiencies via: Dedicated resources: contingent staffing model replaced with global full-time resource model that retains key personnel with annual attrition rate of less than 5%; cross-training program for fast ramp-up and productivity. Global QA centers: global support from multi-site, multi-shore facilities including China, Taiwan, Singapore, India, Ireland, and the United States; onshore Testing Center of Excellence. Standardization: single quality management system (VeriTest QMS) deployed across 50 product teams; framework for test metrics analysis and dashboards established. Automation: accelerated transition and conversion of manual test cases using internal toolsets. Knowledge sharing: development of SharePoint portal and wikis to capture institutional, project, and product knowledge. In-market testing: in-country network enables faster releases to international markets.
Operational Impact
Quantitative Benefit
Related Case Studies.
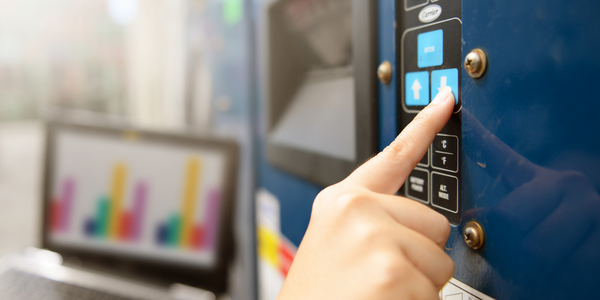
Case Study
Remote Temperature Monitoring of Perishable Goods Saves Money
RMONI was facing temperature monitoring challenges in a cold chain business. A cold chain must be established and maintained to ensure goods have been properly refrigerated during every step of the process, making temperature monitoring a critical business function. Manual registration practice can be very costly, labor intensive and prone to mistakes.
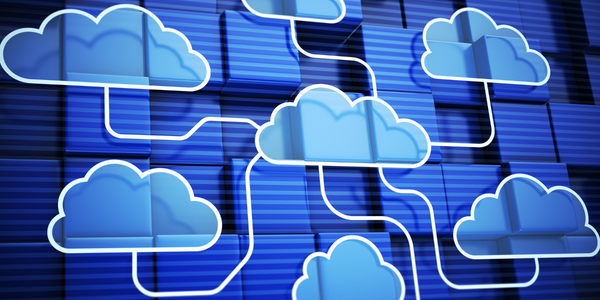
Case Study
Cloud Solution for Energy Management Platform-Schneider Electric
Schneider Electric required a cloud solution for its energy management platform to manage high computational operations, which were essential for catering to client requirements. As the business involves storage and analysis of huge amounts of data, the company also needed a convenient and scalable storage solution to facilitate operations efficiently.
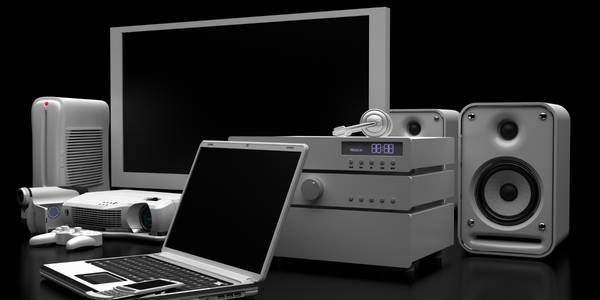
Case Study
Leveraging the IoT to Gain a Competitive Edge in International Competition
Many large manufacturers in and outside Japan are competing for larger market share in the same space, expecting a growing demand for projectors in the areas of entertainment, which requires glamor and strong visual performance as well as digital signage that can attract people’s attention. “It is becoming more and more difficult to differentiate ourselves with stand-alone hardware products,” says Kazuyuki Kitagawa, Director of Service & Support at Panasonic AVC Networks. “In order for Panasonic to grow market share and overall business, it is essential for us to develop solutions that deliver significant added value.” Panasonic believes projection failure and quality deterioration should never happen. This is what and has driven them to make their projectors IoT-enabled. More specifically, Panasonic has developed a system that collects data from projectors, visualizes detailed operational statuses, and predicts issues and address them before failure occurs. Their projectors are embedded with a variety of sensors that measure power supply, voltage, video input/ output signals, intake/exhaust air temperatures, cooling fan operations, and light bulb operating time. These sensors have been used to make the projector more intelligent, automatically suspending operation when the temperature rises excessively, and automatically switching light bulbs. Although this was a great first step, Panasonic projectors were still not equipped with any capability to send the data over a network.