Download PDF
Manufacturing Industry Excellence Award Winner SAMTEC
Technology Category
- Functional Applications - Enterprise Resource Planning Systems (ERP)
- Functional Applications - Inventory Management Systems
Applicable Industries
- Electronics
Applicable Functions
- Discrete Manufacturing
- Quality Assurance
Use Cases
- Inventory Management
- Regulatory Compliance Monitoring
Services
- Software Design & Engineering Services
- System Integration
The Challenge
SAMTEC, a manufacturer of specialized electronic components, was facing challenges in managing and monitoring its chemical materials due to the growth of the company and the expansion into new product lines. The company needed to ensure compliance with regulations from the U.S. Environmental Protection Agency (EPA) and the Department of Homeland Security (DHS), which required constant monitoring of certain chemicals used in their manufacturing processes. The DHS provides companies with a list of thresholds for quantities of selected chemicals that they are permitted to have on site at their facilities at any one time. If the aggregated amount of a restricted chemical reaches thresholds specified on the “Chemicals of Interest” list, then the company must report the variance to DHS. EPA’s Tier II inventory reporting for EPCRA is another threshold-based regulation that provides a limit (in pounds) of specified chemicals that may be managed over a reporting year. If a business operation exceeds that threshold, then the company must provide an annual report to EPA. SAMTEC was committed to ensuring compliance with these and other regulations by constantly monitoring and managing all of its chemical materials but the job was getting more difficult.
About The Customer
SAMTEC Inc. is a privately-held firm that manufactures a variety of highly specialized electronic components for sale around the world. The company's products range from high-speed interconnects to flex circuitry to RF components and cables. After over 30 years of business, SAMTEC has grown to achieve sales approaching $500 million annually and employs more than 2,000 people in the United States, China, Costa Rica, Malaysia, and Panama. The company is headquartered in southern Indiana. SAMTEC actively supports industry standards for best practices in environmental management such as ISO 14000. However, its electronics manufacturing processes require the use of certain chemicals that are closely watched by not only the U.S. Environmental Protection Agency (EPA) but also the Department of Homeland Security (DHS).
The Solution
To address these challenges, SAMTEC implemented the ComplyPlus software from Sphera. This comprehensive SDS management system and services provider met their specialized needs. The system allowed SAMTEC to automate scheduled threshold reporting and inventory integration, which became a critical business management need. The ComplyPlus software not only houses the company’s SDSs but also allows users to inventory, track and report materials. It provides a direct link between production materials and products, giving the environmental management team the in-depth analysis capabilities that they need to fulfill their reporting obligations across a variety of national, state and local jurisdictions. The system has been translated into Spanish and Chinese to support SAMTEC’s global operations. The system is very customizable and integrated with SAMTEC’s own hazardous material inventory, providing a tool that was very flexible for their needs.
Operational Impact
Quantitative Benefit
Related Case Studies.
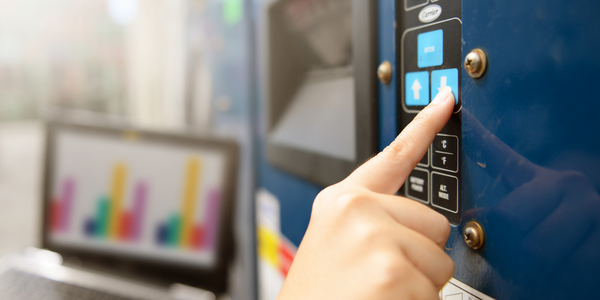
Case Study
Remote Temperature Monitoring of Perishable Goods Saves Money
RMONI was facing temperature monitoring challenges in a cold chain business. A cold chain must be established and maintained to ensure goods have been properly refrigerated during every step of the process, making temperature monitoring a critical business function. Manual registration practice can be very costly, labor intensive and prone to mistakes.
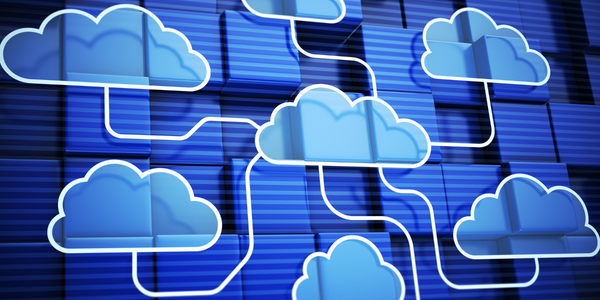
Case Study
Cloud Solution for Energy Management Platform-Schneider Electric
Schneider Electric required a cloud solution for its energy management platform to manage high computational operations, which were essential for catering to client requirements. As the business involves storage and analysis of huge amounts of data, the company also needed a convenient and scalable storage solution to facilitate operations efficiently.
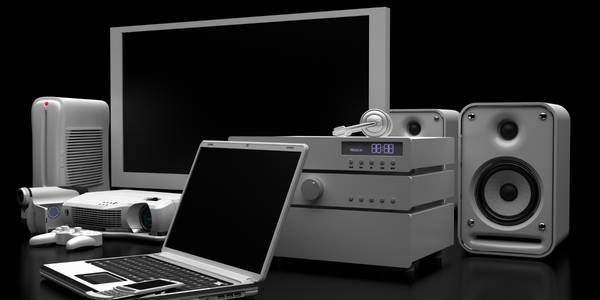
Case Study
Leveraging the IoT to Gain a Competitive Edge in International Competition
Many large manufacturers in and outside Japan are competing for larger market share in the same space, expecting a growing demand for projectors in the areas of entertainment, which requires glamor and strong visual performance as well as digital signage that can attract people’s attention. “It is becoming more and more difficult to differentiate ourselves with stand-alone hardware products,” says Kazuyuki Kitagawa, Director of Service & Support at Panasonic AVC Networks. “In order for Panasonic to grow market share and overall business, it is essential for us to develop solutions that deliver significant added value.” Panasonic believes projection failure and quality deterioration should never happen. This is what and has driven them to make their projectors IoT-enabled. More specifically, Panasonic has developed a system that collects data from projectors, visualizes detailed operational statuses, and predicts issues and address them before failure occurs. Their projectors are embedded with a variety of sensors that measure power supply, voltage, video input/ output signals, intake/exhaust air temperatures, cooling fan operations, and light bulb operating time. These sensors have been used to make the projector more intelligent, automatically suspending operation when the temperature rises excessively, and automatically switching light bulbs. Although this was a great first step, Panasonic projectors were still not equipped with any capability to send the data over a network.