Download PDF
Michelin Drives Innovation and Collaboration
Technology Category
- Platform as a Service (PaaS) - Data Management Platforms
Applicable Industries
- Automotive
Use Cases
- Demand Planning & Forecasting
- Supply Chain Visibility
Services
- Cloud Planning, Design & Implementation Services
The Challenge
Michelin, a leading tire manufacturer, faced increased supply chain complexity due to scarce capacity, a growing portfolio of tire types, and a significant increase in parts resulting from the company’s innovation efforts. The market in which the company operates had also become increasingly volatile and competitive, as well as impacted by seasonal demand. After analyzing its existing S&OP decision-making process, several potential improvements were identified including undetected opportunities, risks, and constraints. Legacy tools and processes used by the Michelin business units were heterogeneous and didn’t have the flexibility necessary to support its S&OP transformation.
About The Customer
Michelin is a leading tire manufacturer, headquartered in ClermontFerrand in the Auvergne region of France. Michelin is present in more than 170 countries and operates 68 production plants in 17 different countries. In addition to the Michelin brand, the company owns a strong brand portfolio, including BFGoodrich, Kleber, Tigar, Riken, Kormoran, and the Uniroyal brand for the North American market, among others. Michelin’s supply chain complexity increased substantially and had become more difficult to manage due to scarce capacity, a growing portfolio of tire types and a significant increase in parts resulting from the company’s innovation efforts.
The Solution
Michelin deployed Blue Yonder’s agile implementation approach, which includes a sequence of three-week sprints of designing, constructing, testing, and validating the solution. This rapid prototyping methodology enabled the team to learn and mature quickly in their use of the solution while achieving results through each phase of the project, ensuring adoption by the business. A key enabler of this approach was the use of Blue Yonder cloud launch to support rapid deployment and performance testing. In addition to the organizational and technology rollout, Michelin conducted a gap analysis of its S&OP processes and its position on the S&OP maturity curve. The teams identified process gaps and data consistency issues and built an action plan to close those gaps.
Operational Impact
Quantitative Benefit
Related Case Studies.
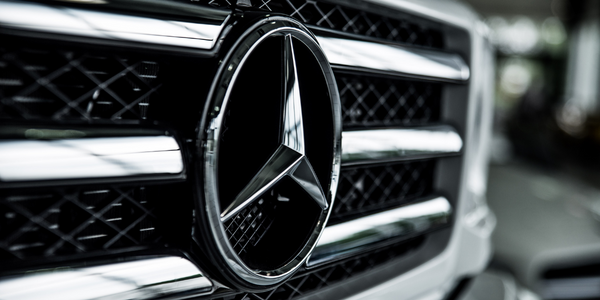
Case Study
Integral Plant Maintenance
Mercedes-Benz and his partner GAZ chose Siemens to be its maintenance partner at a new engine plant in Yaroslavl, Russia. The new plant offers a capacity to manufacture diesel engines for the Russian market, for locally produced Sprinter Classic. In addition to engines for the local market, the Yaroslavl plant will also produce spare parts. Mercedes-Benz Russia and his partner needed a service partner in order to ensure the operation of these lines in a maintenance partnership arrangement. The challenges included coordinating the entire maintenance management operation, in particular inspections, corrective and predictive maintenance activities, and the optimizing spare parts management. Siemens developed a customized maintenance solution that includes all electronic and mechanical maintenance activities (Integral Plant Maintenance).
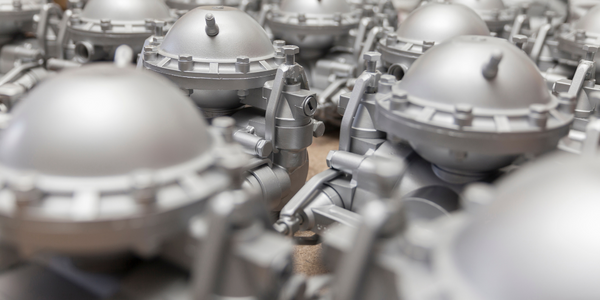
Case Study
Monitoring of Pressure Pumps in Automotive Industry
A large German/American producer of auto parts uses high-pressure pumps to deburr machined parts as a part of its production and quality check process. They decided to monitor these pumps to make sure they work properly and that they can see any indications leading to a potential failure before it affects their process.