Download PDF
Miniature Precision Components, Inc. Shifts into Real Time with IQMS
Technology Category
- Functional Applications - Enterprise Asset Management Systems (EAM)
- Functional Applications - Enterprise Resource Planning Systems (ERP)
- Functional Applications - Warehouse Management Systems (WMS)
Applicable Industries
- Automotive
Applicable Functions
- Discrete Manufacturing
- Logistics & Transportation
- Quality Assurance
Use Cases
- Inventory Management
- Manufacturing System Automation
- Predictive Maintenance
Services
- Software Design & Engineering Services
- System Integration
The Challenge
Miniature Precision Components, Inc. (MPC), a leading tier-one supplier for major automotive manufacturers, was facing challenges due to its outdated enterprise resource planning (ERP) system. The system had been heavily modified over the years to accommodate the company's specific requirements and add third-party functionality. However, these modifications hindered easy and cost-effective updates, leaving MPC's system about three years behind current technology, even as the company paid for regular system updates. The system was also restrictive and disjointed, making it difficult to reconcile and manage data. MPC needed a new ERP system that could support its mission of delivering top-tier quality to the major automotive manufacturers, provide real-time data, and integrate all segments of the business.
About The Customer
Miniature Precision Components, Inc. (MPC) is a leading tier-one supplier for the major automotive manufacturers. Founded in 1972, MPC operates under the premise that its customers' success is its own. This belief has driven MPC to invest in equipment, technology, and human resources to meet and exceed its customers' expectations. The company is committed to providing quality, superior design, reliability, and execution in everything it does, and has established effective quality disciplines to ensure conformance across its enterprise. Headquartered in Walworth, Wisconsin, MPC has 1,900 employees and operates manufacturing plants in Wisconsin and Mexico.
The Solution
MPC decided to implement the EnterpriseIQ ERP software system with RealTime Production Monitoring from IQMS. This system was chosen for its strong production environment, ease-of-use, comprehensive reporting capabilities, and total visibility across the entire enterprise. The RealTime Production Monitoring module allowed MPC to shift from batch to real-time processing, providing immediate visibility into what machines were running and at what level of quality and productivity. The EnterpriseIQ system operates all within one database, guaranteeing interoperability between modules and centralizing the company's business data and activity in one easy-to-access location. This increased data reliability and provided better visibility across the entire enterprise. The system also allowed MPC to examine its production processes with an eye for outliers and poor performance, targeting specific areas for improvement.
Operational Impact
Quantitative Benefit
Related Case Studies.
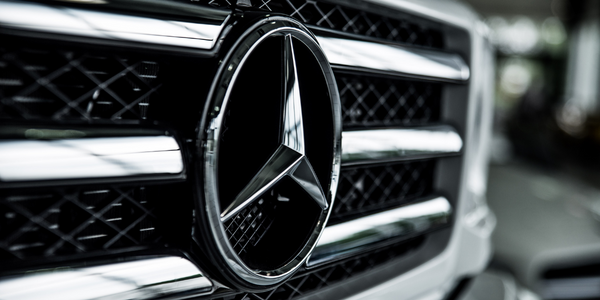
Case Study
Integral Plant Maintenance
Mercedes-Benz and his partner GAZ chose Siemens to be its maintenance partner at a new engine plant in Yaroslavl, Russia. The new plant offers a capacity to manufacture diesel engines for the Russian market, for locally produced Sprinter Classic. In addition to engines for the local market, the Yaroslavl plant will also produce spare parts. Mercedes-Benz Russia and his partner needed a service partner in order to ensure the operation of these lines in a maintenance partnership arrangement. The challenges included coordinating the entire maintenance management operation, in particular inspections, corrective and predictive maintenance activities, and the optimizing spare parts management. Siemens developed a customized maintenance solution that includes all electronic and mechanical maintenance activities (Integral Plant Maintenance).
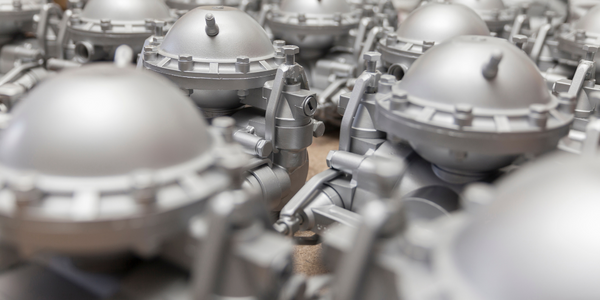
Case Study
Monitoring of Pressure Pumps in Automotive Industry
A large German/American producer of auto parts uses high-pressure pumps to deburr machined parts as a part of its production and quality check process. They decided to monitor these pumps to make sure they work properly and that they can see any indications leading to a potential failure before it affects their process.