Download PDF
Nashville Wire Products Drives Efficiency With Sage 500 ERP
Technology Category
- Functional Applications - Enterprise Resource Planning Systems (ERP)
Applicable Functions
- Discrete Manufacturing
- Procurement
Use Cases
- Inventory Management
- Manufacturing System Automation
Services
- System Integration
The Challenge
Nashville Wire Products was using a highly customized version of ProfitKey, an ERP and manufacturing application. The system proved to be costly to maintain and support, and it was difficult to obtain data and operating metrics from it. The technology was old and cumbersome and not nimble enough to support their fast-paced operation. An internal project team analyzed available options, including Sage 500 ERP, Microsoft Dynamics AX, and Microsoft Dynamics NV. They selected Sage 500 ERP for many reasons, including the more intuitive interface and strong business partner support it offered.
About The Customer
For more than 75 years, Nashville Wire Products has been designing and fabricating welded wire products. Throughout its history, the company has continually expanded and diversified its operations, moving into multiple markets and serving thousands of customers. Today, the company has revenues in excess of $90 million, and its three divisions ship millions of units annually. Cutting-edge technology, quality products, and unparalleled service have earned Nashville Wire Products a leadership position in all of the markets that it serves. The family-owned company always has embraced technology as a tool to drive efficiency and build its business and now trusts its operations to Sage 500 ERP.
The Solution
Sage 500 ERP was selected as the backbone of the operation, with Sage SalesLogix, Sage HRMS, and Sage Sales Tax as companion solutions. A significant benefit for the company was the industry-standard SQL database utilized by Sage 500 ERP and the companion products. They were able to move from seven or eight separate databases holding manufacturing, customer, and financial data to a single integrated database that is accessible, stable, and easy to administer. The Business Insights Explorer module helps make the data accessible by providing the ability to perform quick queries of data across the entire enterprise.
Operational Impact
Quantitative Benefit
Related Case Studies.
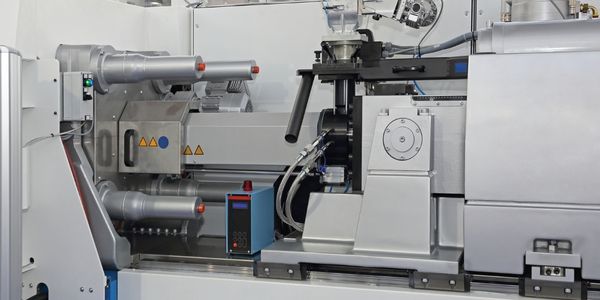
Case Study
Plastic Spoons Case study: Injection Moulding
In order to meet customer expectations by supplying a wide variety of packaging units, from 36 to 1000 spoons per package, a new production and packaging line needed to be built. DeSter wanted to achieve higher production capacity, lower cycle time and a high degree of operator friendliness with this new production line.
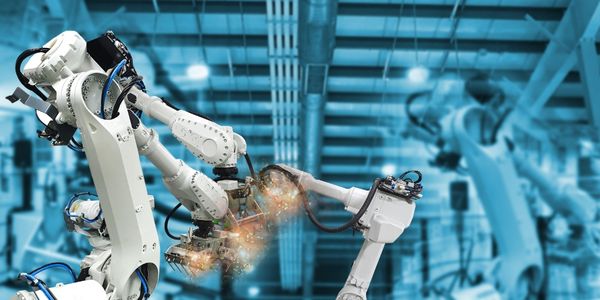
Case Study
Robot Saves Money and Time for US Custom Molding Company
Injection Technology (Itech) is a custom molder for a variety of clients that require precision plastic parts for such products as electric meter covers, dental appliance cases and spools. With 95 employees operating 23 molding machines in a 30,000 square foot plant, Itech wanted to reduce man hours and increase efficiency.
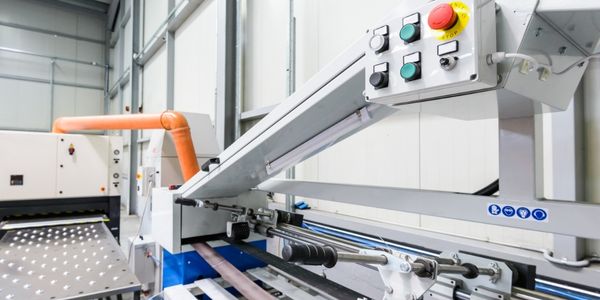
Case Study
Fully Automated Visual Inspection System
Tofflon has developed a fully automatic machine that uses light to inspect vials, medicine bottles, or infusion containers for glass fragments, aluminum particles, rubber grains, hairs, fibers, or other contaminants. It also detects damaged containers with cracks or inclusions (microscopic imperfections), automatically removing faulty or contaminated products. In order to cover all production processes for freeze-dried pharmaceuticals, Tofflon needed to create an open, consistent, and module-based automation concept.
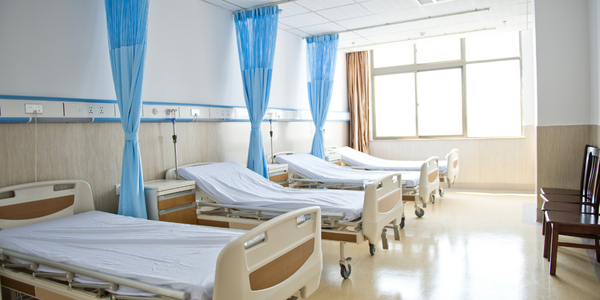
Case Study
Hospital Inventory Management
The hospital supply chain team is responsible for ensuring that the right medical supplies are readily available to clinicians when and where needed, and to do so in the most efficient manner possible. However, many of the systems and processes in use at the cancer center for supply chain management were not best suited to support these goals. Barcoding technology, a commonly used method for inventory management of medical supplies, is labor intensive, time consuming, does not provide real-time visibility into inventory levels and can be prone to error. Consequently, the lack of accurate and real-time visibility into inventory levels across multiple supply rooms in multiple hospital facilities creates additional inefficiency in the system causing over-ordering, hoarding, and wasted supplies. Other sources of waste and cost were also identified as candidates for improvement. Existing systems and processes did not provide adequate security for high-cost inventory within the hospital, which was another driver of cost. A lack of visibility into expiration dates for supplies resulted in supplies being wasted due to past expiry dates. Storage of supplies was also a key consideration given the location of the cancer center’s facilities in a dense urban setting, where space is always at a premium. In order to address the challenges outlined above, the hospital sought a solution that would provide real-time inventory information with high levels of accuracy, reduce the level of manual effort required and enable data driven decision making to ensure that the right supplies were readily available to clinicians in the right location at the right time.
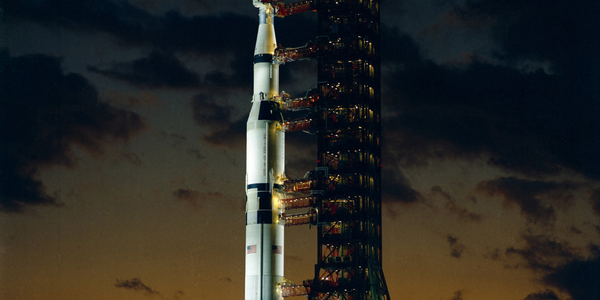
Case Study
SAP Leonardo Enabling Rocket Science
At times, ULA has as many as 15 different operating systems dedicated to overlapping processes, such as rocket design, testing, and launch. Multiple systems created unnecessary costs and unwanted confusion among workers at offices, factories, and launch sites in different location. In order to improve collaboration and transparency during vital activities that directly influence mission success, ULA wanted to improve data sharing and streamline manufacturing processes.