Download PDF
NSE Composites: Energy, Process and Utilities Case Study
Technology Category
- Analytics & Modeling - Digital Twin / Simulation
Applicable Industries
- Renewable Energy
Applicable Functions
- Product Research & Development
Use Cases
- Digital Twin
- Predictive Maintenance
Services
- Software Design & Engineering Services
The Challenge
NSE Composites was tasked with analyzing loads, stresses, and fatigue for an innovative, sweep-twist wind turbine blade design that is targeted to capture significantly more energy on light-windspeed sites. The basic physics and economics of wind turbine blades are relatively simple. Their power output is roughly proportional to the square of blade length. This relationship pushes designers to create increasingly longer blades for harvesting additional kilowatts. Secondly, as blades get longer, weight increases—by approximately the cube of the length—leading to higher raw material costs. This correlation sends designers in search of weight-efficient geometries that are strong and rigid enough to weather the increased loading inherent in longer blades.
About The Customer
NSE Composites is a Seattle-based company that has been providing composite engineering solutions to a variety of aerospace, wind, and other customers since 1996. NSE’s engineering team has broad experience with composite materials in aerospace structures, which enables it to bring an applied, results-oriented approach to a wide variety of composite product development projects. In addition, NSE is actively involved in composite structures R&D and the development of analysis software tools. The company offers services in the areas of design, analysis, testing, and structural certification.
The Solution
NSE Composites used SIMULIA’s Abaqus finite element analysis (FEA) to validate the overall blade twisting behavior as well as buckling and fatigue. The software’s ongoing developments in simulating composites, crack generation, and fracture kept pace with the projects as they moved toward larger and more complex models. The software was able to handle composite properties and control material orientation. It could calculate blade-tip deflection (to avoid “tower strike”) and accurately predict both torsional response (including twist angle, which is key to load-shedding) and shear-compression buckling stability (associated with sweep-twist) of composite sandwich structures. An additional capability key to wind blade analysis is the extraction of accurate equivalent beam properties directly from a solid 3D FEM.
Operational Impact
Quantitative Benefit
Related Case Studies.
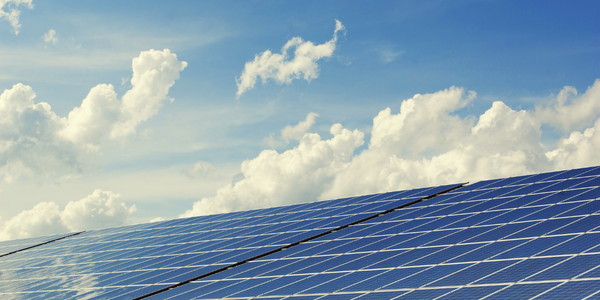
Case Study
Remote Monitoring & Predictive Maintenance App for a Solar Energy System
The maintenance & tracking of various modules was an overhead for the customer due to the huge labor costs involved. Being an advanced solar solutions provider, they wanted to ensure early detection of issues and provide the best-in-class customer experience. Hence they wanted to automate the whole process.
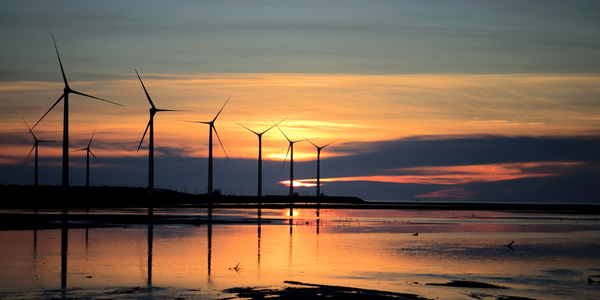
Case Study
Vestas: Turning Climate into Capital with Big Data
Making wind a reliable source of energy depends greatly on the placement of the wind turbines used to produce electricity. Turbulence is a significant factor as it strains turbine components, making them more likely to fail. Vestas wanted to pinpoint the optimal location for wind turbines to maximize power generation and reduce energy costs.
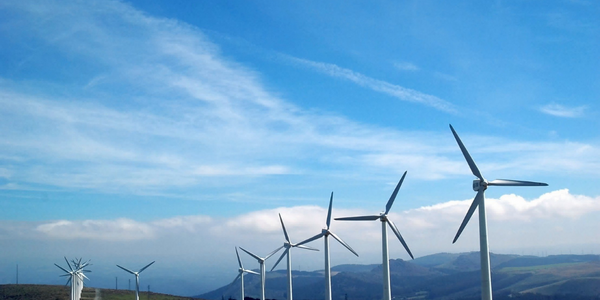
Case Study
Siemens Wind Power
Wind provides clean, renewable energy. The core concept is simple: wind turbines spin blades to generate power. However, today's systems are anything but simple. Modern wind turbines have blades that sweep a 120 meter circle, cost more than 1 million dollars and generate multiple megawatts of power. Each turbine may include up to 1,000 sensors and actuators – integrating strain gages, bearing monitors and power conditioning technology. The turbine can control blade speed and power generation by altering the blade pitch and power extraction. Controlling the turbine is a sophisticated job requiring many cooperating processors closing high-speed loops and implementing intelligent monitoring and optimization algorithms. But the real challenge is integrating these turbines so that they work together. A wind farm may include hundreds of turbines. They are often installed in difficult-to-access locations at sea. The farm must implement a fundamentally and truly distributed control system. Like all power systems, the goal of the farm is to match generation to load. A farm with hundreds of turbines must optimize that load by balancing the loading and generation across a wide geography. Wind, of course, is dynamic. Almost every picture of a wind farm shows a calm sea and a setting sun. But things get challenging when a storm goes through the wind farm. In a storm, the control system must decide how to take energy out of gusts to generate constant power. It must intelligently balance load across many turbines. And a critical consideration is the loading and potential damage to a half-billion-dollar installed asset. This is no environment for a slow or undependable control system. Reliability and performance are crucial.
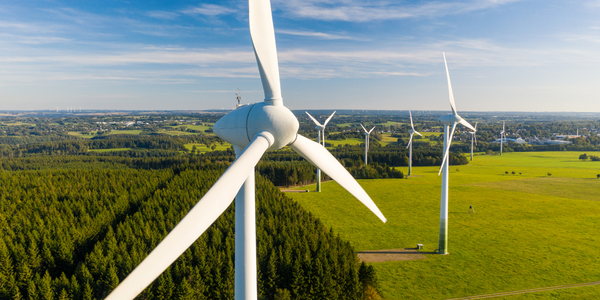
Case Study
Remote Monitoring and Control for a Windmill Generator
As concerns over global warming continue to grow, green technologies are becoming increasingly popular. Wind turbine companies provide an excellent alternative to burning fossil fuels by harnessing kinetic energy from the wind and converting it into electricity. A typical wind farm may include over 80 wind turbines so efficient and reliable networks to manage and control these installations are imperative. Each wind turbine includes a generator and a variety of serial components such as a water cooler, high voltage transformer, ultrasonic wind sensors, yaw gear, blade bearing, pitch cylinder, and hub controller. All of these components are controlled by a PLC and communicate with the ground host. Due to the total integration of these devices into an Ethernet network, one of our customers in the wind turbine industry needed a serial-to-Ethernet solution that can operate reliably for years without interruption.
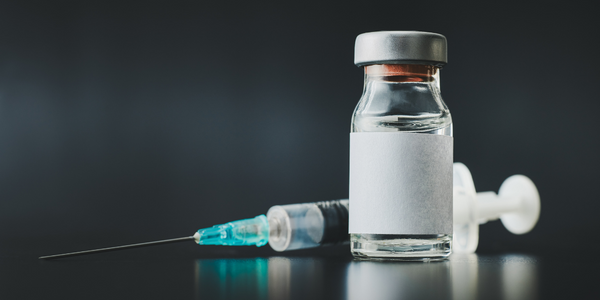
Case Study
Temperature monitoring for vaccine fridges
Dulas wanted a way to improve the reliability of the cold chain, facilitating maintenance and ensuring fewer vaccines are spoiled. Dulas wanted an M2M solution which would enable them to record and report the temperature inside vaccine refrigerators.
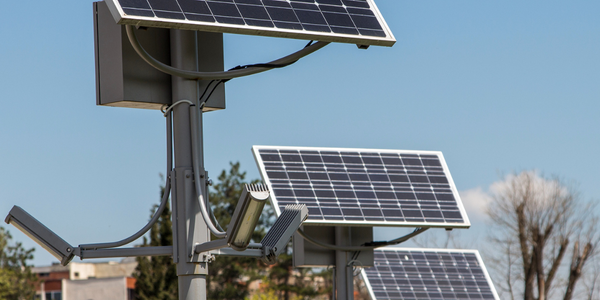
Case Study
IoT Powering A New Way to Light Streets with Bifacial Solar Panels
When James Meringer’s commercial contracting business experienced a rapid increase in solar projects, he also saw an opportunity to extend the benefits of solar by using the bifacial solar panels he’d become familiar with in new ways. Bifacial solar panels enable sunlight from both sides of the panel, making it a more efficient harvest of solar power. Seeing the panel’s power, James and his team set out to use the same technology for street lighting. Until now, solar street lights have served as utilitarian solutions that force designers to choose between form and function. The Mira Bella Energy team has changed that.