Download PDF
Ocean Spray & SPC: Growing Together
Technology Category
- Analytics & Modeling - Predictive Analytics
- Functional Applications - Manufacturing Execution Systems (MES)
Applicable Industries
- Food & Beverage
Applicable Functions
- Process Manufacturing
- Quality Assurance
Use Cases
- Factory Operations Visibility & Intelligence
- Predictive Quality Analytics
- Process Control & Optimization
Services
- Software Design & Engineering Services
- System Integration
- Training
The Challenge
Ocean Spray's Markham, WA Craisins® dried cranberries manufacturing facility began using InfinityQS in 2006 to display and analyze its manufacturing data visually. The quality team wanted to move away from paper-based records and access real-time data for immediate process improvements. Before implementing SPC tools, operators were trained not to tweak in-spec processes, which led to inefficiencies and higher costs. The challenge was to shift the mindset to drive towards target using SPC, ensuring consistency in quality and consumer experience across multiple plants.
About The Customer
Ocean Spray Cranberries® Inc. is a farmer-owned cooperative founded in 1930 and a world leader in cranberries. The cooperative distributes over 1,000 unique products worldwide, including juices, cranberry sauce, cranberry supplements, fresh fruit, and Craisins® dried cranberries. Ocean Spray operates five global dried cranberry plants, all of which use InfinityQS Statistical Process Control (SPC) tools to track every step in the production lifecycle. The cooperative is committed to customer satisfaction and continuous improvement, leveraging hard work, innovation, and ingenuity to deliver healthy and delicious products.
The Solution
Ocean Spray implemented InfinityQS SPC tools across its five global dried cranberry plants to enhance process visibility and enable real-time data access. The Markham, WA plant switched on SPC rules for a specific Craisins® dried cranberries quality process in January 2019, significantly improving process capability. The SPC tools allowed Ocean Spray to standardize data collection, simplify reporting, and make instant, impactful improvements. The Quality team used creative methods like the SPC Golf Challenge to demonstrate the benefits of SPC and ensure employee buy-in. The flexibility of InfinityQS allowed for custom suites of limits and rules for each process, reducing unnecessary alarms and empowering operators to make critical process decisions.
Operational Impact
Quantitative Benefit
Related Case Studies.
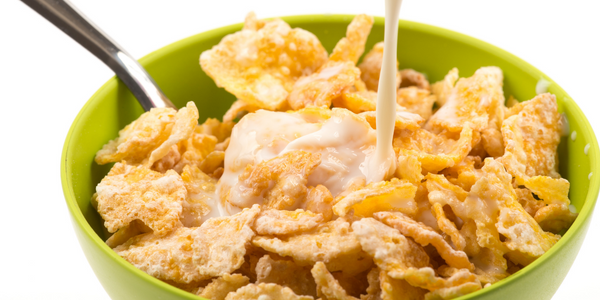
Case Study
The Kellogg Company
Kellogg keeps a close eye on its trade spend, analyzing large volumes of data and running complex simulations to predict which promotional activities will be the most effective. Kellogg needed to decrease the trade spend but its traditional relational database on premises could not keep up with the pace of demand.
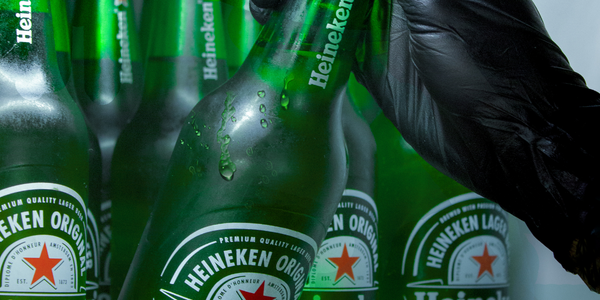
Case Study
HEINEKEN Uses the Cloud to Reach 10.5 Million Consumers
For 2012 campaign, the Bond promotion, it planned to launch the campaign at the same time everywhere on the planet. That created unprecedented challenges for HEINEKEN—nowhere more so than in its technology operation. The primary digital content for the campaign was a 100-megabyte movie that had to play flawlessly for millions of viewers worldwide. After all, Bond never fails. No one was going to tolerate a technology failure that might bruise his brand.Previously, HEINEKEN had supported digital media at its outsourced datacenter. But that datacenter lacked the computing resources HEINEKEN needed, and building them—especially to support peak traffic that would total millions of simultaneous hits—would have been both time-consuming and expensive. Nor would it have provided the geographic reach that HEINEKEN needed to minimize latency worldwide.
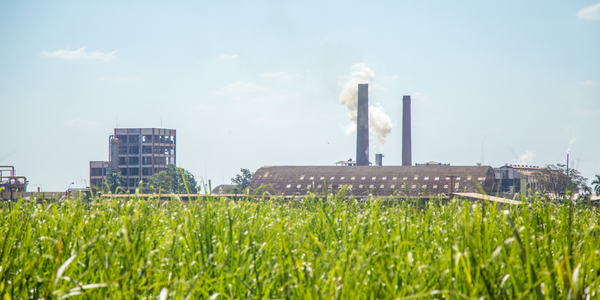
Case Study
Energy Management System at Sugar Industry
The company wanted to use the information from the system to claim under the renewable energy certificate scheme. The benefit to the company under the renewable energy certificates is Rs 75 million a year. To enable the above, an end-to-end solution for load monitoring, consumption monitoring, online data monitoring, automatic meter data acquisition which can be exported to SAP and other applications is required.
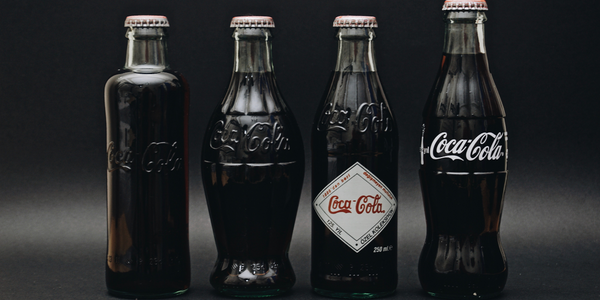
Case Study
Coca Cola Swaziland Conco Case Study
Coco Cola Swaziland, South Africa would like to find a solution that would enable the following results: - Reduce energy consumption by 20% in one year. - Formulate a series of strategic initiatives that would enlist the commitment of corporate management and create employee awareness while helping meet departmental targets and investing in tools that assist with energy management. - Formulate a series of tactical initiatives that would optimize energy usage on the shop floor. These would include charging forklifts and running cold rooms only during off-peak periods, running the dust extractors only during working hours and basing lights and air-conditioning on someone’s presence. - Increase visibility into the factory and other processes. - Enable limited, non-intrusive control functions for certain processes.
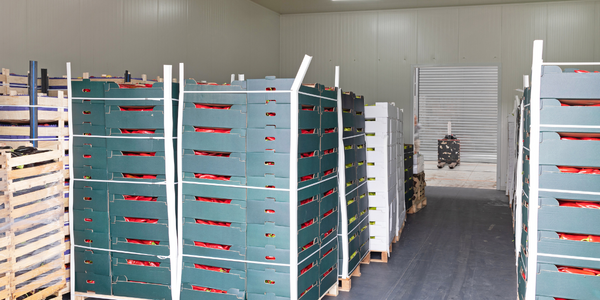
Case Study
Temperature Monitoring for Restaurant Food Storage
When it came to implementing a solution, Mr. Nesbitt had an idea of what functionality that he wanted. Although not mandated by Health Canada, Mr. Nesbitt wanted to ensure quality control issues met the highest possible standards as part of his commitment to top-of-class food services. This wish list included an easy-to use temperature-monitoring system that could provide a visible display of the temperatures of all of his refrigerators and freezers, including historical information so that he could review the performance of his equipment. It also had to provide alert notification (but email alerts and SMS text message alerts) to alert key staff in the event that a cooling system was exceeding pre-set warning limits.
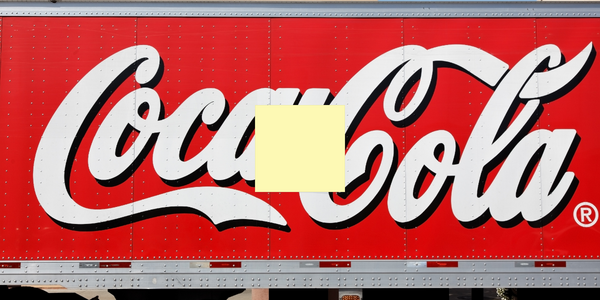
Case Study
Coca-Cola Refreshments, U.S.
Coca-Cola Refreshments owns and manages Coca-Cola branded refrigerators in retail establishments. Legacy systems were used to locate equipment information by logging onto multiple servers which took up to 8 hours to update information on 30-40 units. The company had no overall visibility into equipment status or maintenance history.