Download PDF
Oil & Gas Industry Excellence Award Winner - Repsol
Applicable Industries
- Oil & Gas
Applicable Functions
- Quality Assurance
- Business Operation
Use Cases
- Process Control & Optimization
Services
- System Integration
The Challenge
A decade ago, Repsol executives realized that increasing pressure from local regulators and rigorous European emissions legislation as well as from ESG investors meant that their company needed to establish more reliable and credible environmental management processes. Repsol’s legacy processes for calculating air emissions were disparate, labor intensive and time consuming. Each facility had its own process to create the required regulatory reports and documentation. Many consisted of a series of steps to copy information from source systems – such as PI, laboratory information management systems (LIMS) and production systems – then create and maintain hundreds of spreadsheets with all the necessary calculations and reports. Each process required a host of manual tasks, which had to be performed repeatedly by Health, Safety and Environmental (HSE) staff. As a result, these facility-specific processes left room for human error and provided only limited visibility across the company.
About The Customer
Repsol is one of the world’s leading integrated energy companies, with a broad footprint that extends across more than 40 countries on five continents. Repsol is the major Oil and Gas Company in Spain, based on its extensive upstream and downstream operations, including exploration and production, refining, distribution and marketing, petrochemicals and power generation. Among its key core values, Repsol is committed to maintaining compliance with legal and regulatory requirements and aiming for a neutral environmental impact.
The Solution
Repsol launched a major project called EMISphere that would centralize compliance by implementing an enterprise-level Environmental Information Management System (EMIS). After weighing several options, the company chose the Sphera® Essential™ solution. Repsol launched the EMISphere project in 2012 with implementations at two facilities in Spain. The system was designed to streamline processes for monitoring and measuring compliance with air, water and hazardous waste permit limits at the company’s refineries while delivering full visibility into its HSE performance. Repsol’s team used the Sphera Process Data Manager module to seamlessly move data from their PI, LIMS and production systems directly into the EMIS. Furthermore, the system enabled a superior level of automation in terms of scheduling, validating and applying rules and calculations to process data in an auditable, transparent way.
Operational Impact
Quantitative Benefit
Related Case Studies.
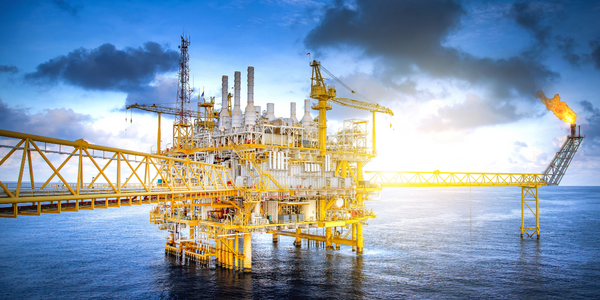
Case Study
Taking Oil and Gas Exploration to the Next Level
DownUnder GeoSolutions (DUG) wanted to increase computing performance by 5 to 10 times to improve seismic processing. The solution must build on current architecture software investments without sacrificing existing software and scale computing without scaling IT infrastructure costs.
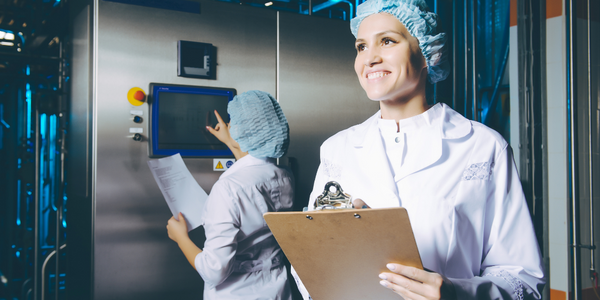
Case Study
Remote Wellhead Monitoring
Each wellhead was equipped with various sensors and meters that needed to be monitored and controlled from a central HMI, often miles away from the assets in the field. Redundant solar and wind generators were installed at each wellhead to support the electrical needs of the pumpstations, temperature meters, cameras, and cellular modules. In addition to asset management and remote control capabilities, data logging for remote surveillance and alarm notifications was a key demand from the customer. Terra Ferma’s solution needed to be power efficient, reliable, and capable of supporting high-bandwidth data-feeds. They needed a multi-link cellular connection to a central server that sustained reliable and redundant monitoring and control of flow meters, temperature sensors, power supply, and event-logging; including video and image files. This open-standard network needed to interface with the existing SCADA and proprietary network management software.
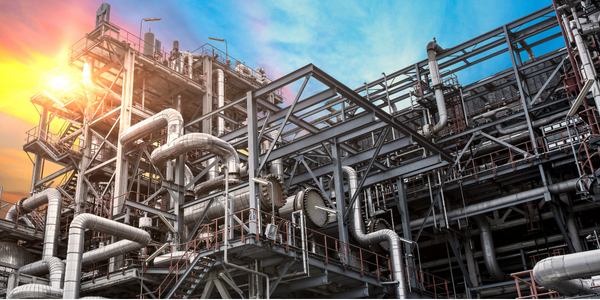
Case Study
Refinery Saves Over $700,000 with Smart Wireless
One of the largest petroleum refineries in the world is equipped to refine various types of crude oil and manufacture various grades of fuel from motor gasoline to Aviation Turbine Fuel. Due to wear and tear, eight hydrogen valves in each refinery were leaking, and each cost $1800 per ton of hydrogen vented. The plant also had leakage on nearly 30 flare control hydrocarbon valves. The refinery wanted a continuous, online monitoring system that could catch leaks early, minimize hydrogen and hydrocarbon production losses, and improve safety for maintenance.