Download PDF
Oil and Gas Solutions Provider Attains ISO 9001 Certification with Intelex Quality Management
Applicable Industries
- Oil & Gas
Applicable Functions
- Quality Assurance
Services
- System Integration
- Training
The Challenge
In 2011, Versabar decided to expand their ability to serve their market by pursuing ISO 9001 certification for their business. However, managing the complexities of ISO certification was proving difficult, particularly because Versabar was managing information from multiple locations. They initially started the process with a paper-based system. They required a software solution to streamline both tracking and reporting of nonconformances and corrective actions across the enterprise for both their products and their processes. They further expanded these requirements to include supplier management capabilities, which was a natural extension of the original requirements that had been identified.
About The Customer
Versabar is a global provider of heavy lifting solutions for the Oil and Gas industry, located in New Orleans and Texas. Founded in 1981 by University of Illinois Civil Engineering Graduate Jon Khachaturian, Versabar began with just the reusable spreader bar. Today, Versabar is registered for 56 foreign and domestic patents and known as a global leader in the development and application of heavy lifting solutions.
The Solution
Versabar required a flexible solution to help them attain ISO certification, while allowing them the independence to tailor the solution to their specific needs. After some initial help from the Intelex team, the project moved from conception to implementation smoothly. Users underwent basic training with Intelex and now all members of the organization have the ability and know-how to log a nonconformance in the system. The central file repository alleviated employee difficulty with finding necessary information and users can now readily access the documents they require. The system was then rolled out to employees who would be interacting with the applications and were trained on six key user tasks: Logging In & Dashboard Navigation, Responding to Assigned Tasks, Logging QNCRs, Document Control (finding, attaching, uploading), Printing Reports, and Reporting Safety Incidents. These six key tasks transitioned employees and migrated these processes and data to a centralized management system.
Operational Impact
Quantitative Benefit
Related Case Studies.
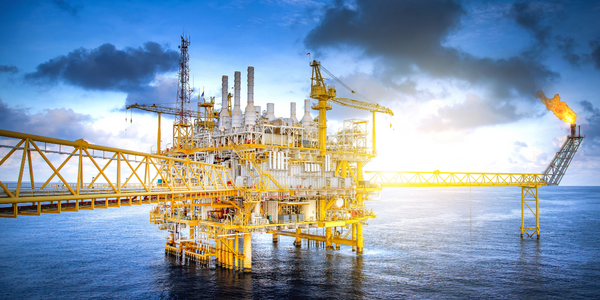
Case Study
Taking Oil and Gas Exploration to the Next Level
DownUnder GeoSolutions (DUG) wanted to increase computing performance by 5 to 10 times to improve seismic processing. The solution must build on current architecture software investments without sacrificing existing software and scale computing without scaling IT infrastructure costs.
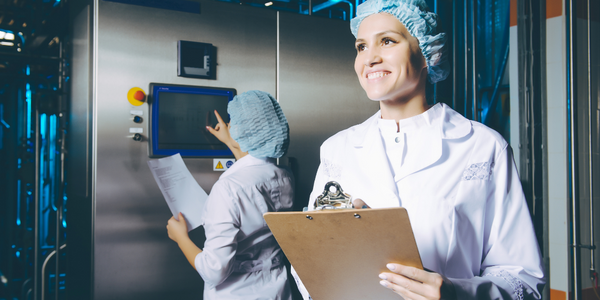
Case Study
Remote Wellhead Monitoring
Each wellhead was equipped with various sensors and meters that needed to be monitored and controlled from a central HMI, often miles away from the assets in the field. Redundant solar and wind generators were installed at each wellhead to support the electrical needs of the pumpstations, temperature meters, cameras, and cellular modules. In addition to asset management and remote control capabilities, data logging for remote surveillance and alarm notifications was a key demand from the customer. Terra Ferma’s solution needed to be power efficient, reliable, and capable of supporting high-bandwidth data-feeds. They needed a multi-link cellular connection to a central server that sustained reliable and redundant monitoring and control of flow meters, temperature sensors, power supply, and event-logging; including video and image files. This open-standard network needed to interface with the existing SCADA and proprietary network management software.
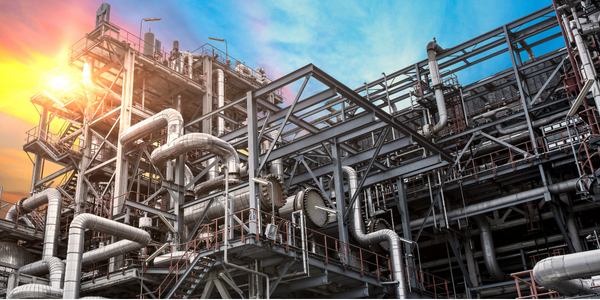
Case Study
Refinery Saves Over $700,000 with Smart Wireless
One of the largest petroleum refineries in the world is equipped to refine various types of crude oil and manufacture various grades of fuel from motor gasoline to Aviation Turbine Fuel. Due to wear and tear, eight hydrogen valves in each refinery were leaking, and each cost $1800 per ton of hydrogen vented. The plant also had leakage on nearly 30 flare control hydrocarbon valves. The refinery wanted a continuous, online monitoring system that could catch leaks early, minimize hydrogen and hydrocarbon production losses, and improve safety for maintenance.