Download PDF
Optimization of Washing Machine Component by Samsung Using OptiStruct
Applicable Industries
- Electronics
- Life Sciences
Applicable Functions
- Logistics & Transportation
- Product Research & Development
Use Cases
- Last Mile Delivery
The Challenge
Suzhou Samsung Electronics Co., a joint venture between Korean and Chinese companies, has been focusing on optimizing the design of a belt pulley for one of its washing machines. The belt pulley, an essential component of a drum washing machine, was traditionally constructed from cast aluminum. However, with increasing cost pressures, the company sought to reduce the pulley’s weight by optimizing its design and/or using new materials for its production. The challenge was to consider alternative materials, taking into account both their performance and cost. To meet these challenges, Suzhou Samsung decided to employ topology optimization.
About The Customer
Suzhou Samsung Electronics Co. is a joint venture between Korean and Chinese companies that develops and produces major home appliances. Over the past 17 years, the company has introduced many new types of refrigerators and washing machines, each carefully engineered to provide the greatest value through optimization that reduces product weight while maintaining top-quality performance. Every component is designed to contribute to this goal, and the company has been focusing on ways to optimize the design of a belt pulley for one of its washing machines.
The Solution
To optimize the pulley, Suzhou Samsung chose OptiStruct, a key component of Altair’s HyperWorks suite of computer-aided engineering tools. OptiStruct provided important optimization features such as topology, size, and shape optimization. The company used the variable-density method of topology optimization, which uses the relative density of the elements as the design variable to determine the optimized material distribution. The process began with a static analysis of the original pulley model, followed by defining the topology optimization model. After solving the optimization problem, the model was rebuilt based on the results and size and shape optimization was conducted on the new model. The process concluded with a static analysis of the optimized structure, comparing results before and after optimization. The company also evaluated the potential benefits of switching from aluminum to a nylon-based belt pulley.
Operational Impact
Quantitative Benefit
Related Case Studies.
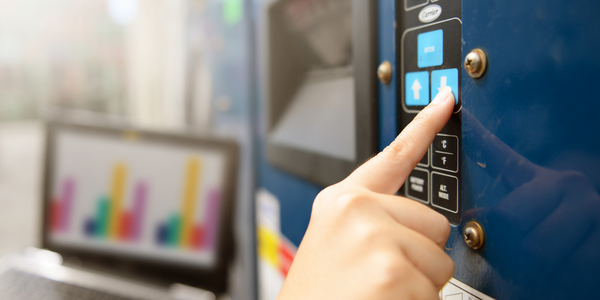
Case Study
Remote Temperature Monitoring of Perishable Goods Saves Money
RMONI was facing temperature monitoring challenges in a cold chain business. A cold chain must be established and maintained to ensure goods have been properly refrigerated during every step of the process, making temperature monitoring a critical business function. Manual registration practice can be very costly, labor intensive and prone to mistakes.
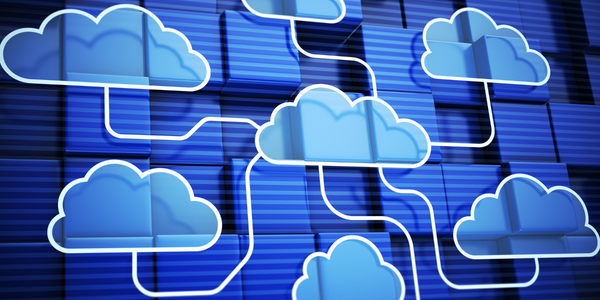
Case Study
Cloud Solution for Energy Management Platform-Schneider Electric
Schneider Electric required a cloud solution for its energy management platform to manage high computational operations, which were essential for catering to client requirements. As the business involves storage and analysis of huge amounts of data, the company also needed a convenient and scalable storage solution to facilitate operations efficiently.
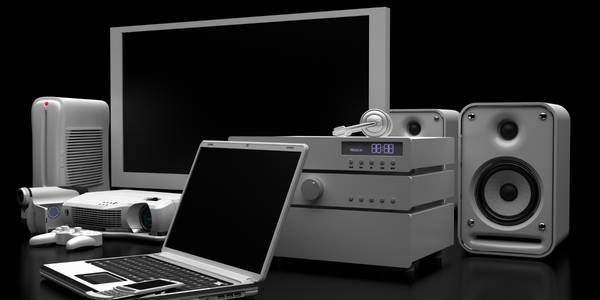
Case Study
Leveraging the IoT to Gain a Competitive Edge in International Competition
Many large manufacturers in and outside Japan are competing for larger market share in the same space, expecting a growing demand for projectors in the areas of entertainment, which requires glamor and strong visual performance as well as digital signage that can attract people’s attention. “It is becoming more and more difficult to differentiate ourselves with stand-alone hardware products,” says Kazuyuki Kitagawa, Director of Service & Support at Panasonic AVC Networks. “In order for Panasonic to grow market share and overall business, it is essential for us to develop solutions that deliver significant added value.” Panasonic believes projection failure and quality deterioration should never happen. This is what and has driven them to make their projectors IoT-enabled. More specifically, Panasonic has developed a system that collects data from projectors, visualizes detailed operational statuses, and predicts issues and address them before failure occurs. Their projectors are embedded with a variety of sensors that measure power supply, voltage, video input/ output signals, intake/exhaust air temperatures, cooling fan operations, and light bulb operating time. These sensors have been used to make the projector more intelligent, automatically suspending operation when the temperature rises excessively, and automatically switching light bulbs. Although this was a great first step, Panasonic projectors were still not equipped with any capability to send the data over a network.