Download PDF
Optimizing 3D Printing Techniques with Simulation Apps
Technology Category
- Analytics & Modeling - Predictive Analytics
- Functional Applications - Manufacturing Execution Systems (MES)
Applicable Industries
- Aerospace
Applicable Functions
- Product Research & Development
- Quality Assurance
Use Cases
- Digital Twin
- Manufacturing System Automation
- Predictive Maintenance
Services
- Software Design & Engineering Services
- System Integration
The Challenge
One of the challenges of shaped metal deposition (SMD) is that thermal expansion of the molten metal can deform the cladding as it cools, resulting in a final product that is different than what was anticipated. To predict the outcome of a proposed design, it is necessary to either minimize the deformations or alter the design to account for them. This requires solving a time-dependent coupled thermomechanical analysis that predicts residual thermal stresses and deformation, which arise from SMD thermal cycles.
About The Customer
The Manufacturing Technology Centre (MTC) in Coventry, UK, provides a unique environment for developing cutting-edge technologies into manufacturing processes. By bringing together the UK's leading academics, engineers, and industry professionals, the MTC helps bridge the gap between concept and industry. Their members include over 80 organizations, such as BAE Systems, GKN, HP, GM, Airbus, and Rolls Royce. The MTC allows clients to develop new manufacturing processes in a safe, neutral industrial setting without the constraints of a commercial production environment.
The Solution
The MTC has leveraged the Application Builder to more efficiently communicate complex design ideas across multiple simulation and process departments. This allows app users to easily explore the outcome of proposed designs. The app includes predefined parametric geometries and allows for custom geometry imports. It enables users to experiment with various geometries, heat sources, deposition paths, and materials without concern for the underlying model complexities. The app is currently being used by team members at the MTC who do not have the simulation experience to independently explore different parts and projects for their customers. This has freed up skilled resources and increased the availability of simulation experts.
Operational Impact
Related Case Studies.
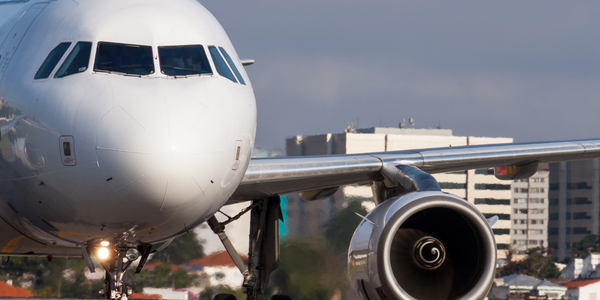
Case Study
Airbus Soars with Wearable Technology
Building an Airbus aircraft involves complex manufacturing processes consisting of thousands of moving parts. Speed and accuracy are critical to business and competitive advantage. Improvements in both would have high impact on Airbus’ bottom line. Airbus wanted to help operators reduce the complexity of assembling cabin seats and decrease the time required to complete this task.
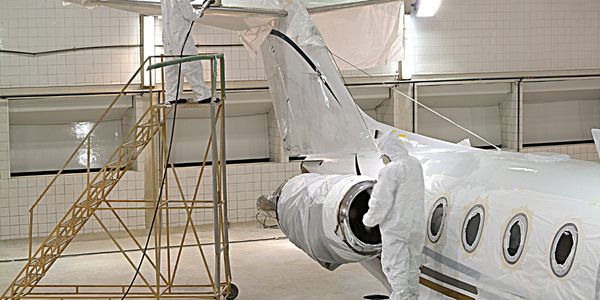
Case Study
Aircraft Predictive Maintenance and Workflow Optimization
First, aircraft manufacturer have trouble monitoring the health of aircraft systems with health prognostics and deliver predictive maintenance insights. Second, aircraft manufacturer wants a solution that can provide an in-context advisory and align job assignments to match technician experience and expertise.
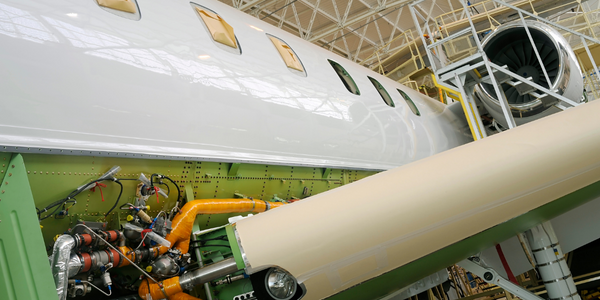
Case Study
Aerospace & Defense Case Study Airbus
For the development of its new wide-body aircraft, Airbus needed to ensure quality and consistency across all internal and external stakeholders. Airbus had many challenges including a very aggressive development schedule and the need to ramp up production quickly to satisfy their delivery commitments. The lack of communication extended design time and introduced errors that drove up costs.
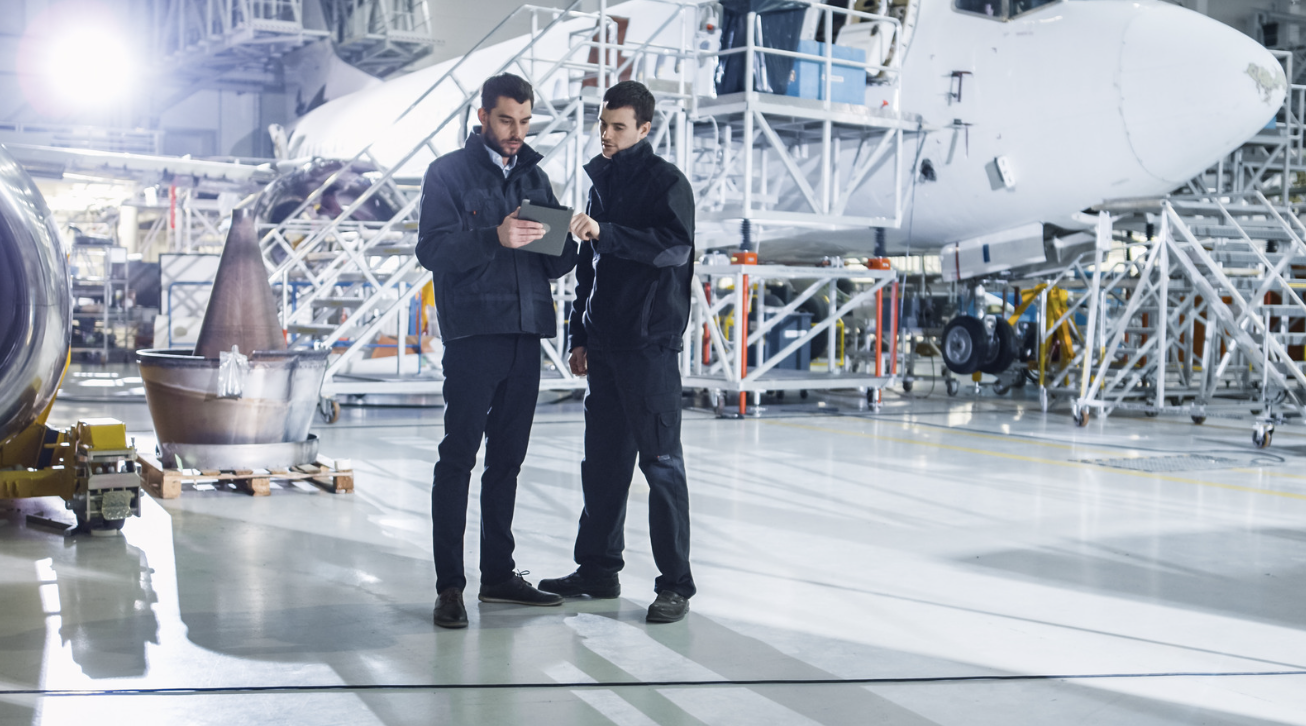
Case Study
Developing Smart Tools for the Airbus Factory
Manufacturing and assembly of aircraft, which involves tens of thousands of steps that must be followed by the operators, and a single mistake in the process could cost hundreds of thousands of dollars to fix, makes the room for error very small.
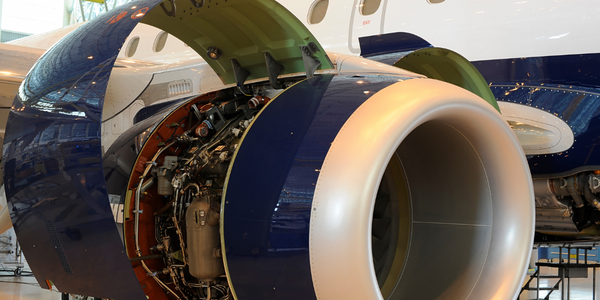
Case Study
Accelerate Production for Spirit AeroSystems
The manufacture and assembly of massive fuselage assemblies and other large structures generates a river of data. In fact, the bill of materials for a single fuselage alone can be millions of rows of data. In-house production processes and testing, as well as other manufacturers and customers created data flows that overwhelmed previous processes and information systems. Spirit’s customer base had grown substantially since their 2005 divestiture from Boeing, resulting in a $41 billion backlog of orders to fill. To address this backlog, meet increased customer demands and minimize additional capital investment, the company needed a way to improve throughput in the existing operational footprint. Spirit had a requirement from customers to increase fuselage production by 30%. To accomplish this goal, Spirit needed real-time information on its value chain and workflow. However, the two terabytes of data being pulled from their SAP ECC was unmanageable and overloaded their business warehouse. It had become time-consuming and difficult to pull aggregate data, disaggregate it for the needed information and then reassemble to create a report. During the 6-8 hours it took to build a report, another work shift (they run three per day) would have already taken place, thus the report content was out-of-date before it was ever delivered. As a result, supervisors often had to rely on manual efforts to provide charts, reports and analysis.