Download PDF
Optimizing Fleet Management: A Case Study of City of Las Cruces
Technology Category
- Functional Applications - Fleet Management Systems (FMS)
Applicable Industries
- Automotive
- Cities & Municipalities
Applicable Functions
- Logistics & Transportation
Use Cases
- Fleet Management
- Smart City Operations
The Challenge
The City of Las Cruces, the second-largest city in New Mexico, was facing challenges in managing its extensive fleet of over 900 vehicles and 700 pieces of equipment. The existing management system was not specifically designed for fleet management, making it difficult to efficiently manage and maintain the city's large and diverse fleet. The system lacked the necessary features and functionalities required for effective fleet management, such as specific drop-downs related to vehicles. This resulted in inefficiencies and difficulties in managing the fleet, from routine maintenance to dealing with crash cars and outsourcing for the Department of Transport.
About The Customer
The City of Las Cruces is the second-largest city in the U.S. state of New Mexico and the seat of Doña Ana County. The city government is responsible for managing a large and diverse fleet of over 900 vehicles and 700 pieces of equipment. This includes a wide range of tasks, from routine maintenance to dealing with crash cars and outsourcing for the Department of Transport. The city government has been using the FleetWave fleet management system since 2019 to manage its fleet more effectively.
The Solution
The City of Las Cruces adopted FleetWave, a fleet management system, in 2019. FleetWave is specifically designed for fleet management, providing features and functionalities that are tailored to the needs of managing a large and diverse fleet. The system allows for the creation of work orders, setting up outsourcing for vehicles, and managing crash cars, among other tasks. FleetWave also offers the flexibility to remove unnecessary features, ensuring that the system is optimized for the specific needs of the City of Las Cruces. The system is used by various roles within the organization, including service writers, technicians, and foremen, to manage the fleet effectively.
Operational Impact
Related Case Studies.
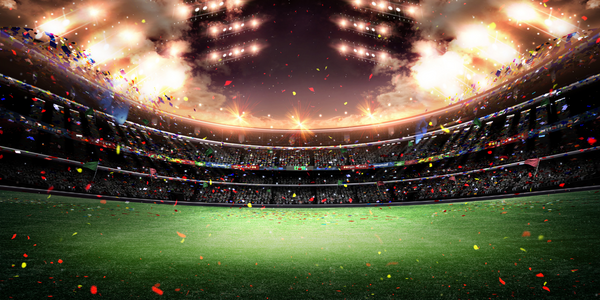
Case Study
Turning A Stadium Into A Smart Building
Honeywell created what it called the “intelligent system” for the National Stadium in Beijing, China, turning the venue for the opening and closing events at the 2008 Summer Olympics into a “smart building.” Designed by highly controversial artist Ai Weiwei, the “Bird’s Nest” remains one of the most impressive feats of stadium architecture in the world. The 250,000 square meter structure housed more than 100,000 athletes and spectators at a time. To accommodate such capacity, China turned to Honeywell’s EBI Integrated Building Management System to create an integrated “intelligent system” for improved building security, safety and energy efficiency.
.png)
Case Study
Smart Street Light Network (Copenhagen)
Key stakeholders are taking a comprehensive approach to rethinking smart city innovation. City leaders have collaborated through partnerships involving government, research institutions and solution providers. The Copenhagen Solutions Lab is one of the leading organizations at the forefront of this movement. By bringing together manufacturers with municipal buyers, the Copenhagen Solutions Lab has catalyzed the development and deployment of next-generation smart city innovations. Copenhagen is leveraging this unique approach to accelerate the implementation of smart city solutions. One of the primary focus areas is LED street lighting.
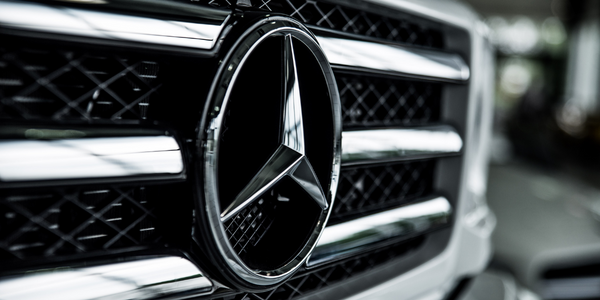
Case Study
Integral Plant Maintenance
Mercedes-Benz and his partner GAZ chose Siemens to be its maintenance partner at a new engine plant in Yaroslavl, Russia. The new plant offers a capacity to manufacture diesel engines for the Russian market, for locally produced Sprinter Classic. In addition to engines for the local market, the Yaroslavl plant will also produce spare parts. Mercedes-Benz Russia and his partner needed a service partner in order to ensure the operation of these lines in a maintenance partnership arrangement. The challenges included coordinating the entire maintenance management operation, in particular inspections, corrective and predictive maintenance activities, and the optimizing spare parts management. Siemens developed a customized maintenance solution that includes all electronic and mechanical maintenance activities (Integral Plant Maintenance).
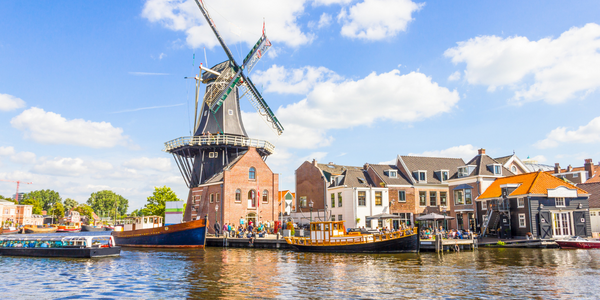
Case Study
Buoy Status Monitoring with LoRa
The Netherlands are well-known for their inland waterways, canals, sluices and of course port activities. The Dutch Ministry of Infrastructure indicates that there are thousands of buoys and fixed items in and near water environments that would profit from IoT monitoring. One of the problems with buoys for example, is that they get hit by ships and the anchor cable breaks. Without connectivity, it takes quite some time to find out that something has happened with that buoy. Not to mention the costs of renting a boat to go to the buoy to fix it. Another important issue, is that there is no real-time monitoring of the buoys at this moment. Only by physically visiting the object on the water, one gains insight in its status.