Download PDF
Optimizing Heavy Hauler Manufacturing with IoT: A Case Study on Hitachi Truck Manufacturing
Technology Category
- Cybersecurity & Privacy - Intrusion Detection
- Functional Applications - Manufacturing Execution Systems (MES)
Applicable Industries
- Automotive
- Mining
Applicable Functions
- Product Research & Development
Use Cases
- Additive Manufacturing
- Manufacturing Process Simulation
Services
- System Integration
The Challenge
Hitachi Truck Manufacturing was faced with the challenge of reducing material costs for their large mining trucks while adhering to standard specifications. The trucks, designed and built at their Guelph, Ontario plant, are massive rigid-body vehicles used for surface mining in various parts of the world. These trucks can be up to 30 feet wide and carry a payload of 316 tons. Given their size, they must be shipped in sections and assembled on site. The design engineers at Hitachi Truck Manufacturing (HTM) were tasked with reducing materials costs, meeting ISO specifications, and maintaining payload performance. The main challenge was predicting the behavior of the truck's structure, particularly the welded steel cab structure, to ensure it met ISO 3471 ROPS (rollover protection system) and FOPS (falling object protection system) specifications.
About The Customer
Hitachi Truck Manufacturing is a company that designs and builds large, rigid-body mining trucks. These trucks are used for surface mining in various parts of the world, including China, Colombia, and Indonesia. The trucks are massive, with some being up to 30 feet wide and capable of carrying a payload of 316 tons. Given their size, these trucks must be shipped in sections and assembled on site. The company is part of a family of heavy equipment manufacturers, producing everything from excavators to boring machines. The company's main challenge was to reduce material costs while adhering to standard specifications and maintaining payload performance.
The Solution
The solution to HTM's challenge came in the form of HyperWorks, a comprehensive open-architecture simulation platform. Harry Tempelman, a HyperWorks expert, joined HTM as technical analysis manager in 2005 and introduced the use of HyperWorks. His focus was on reducing the mass of the welded steel cab structure while still meeting ISO specifications. Tempelman used HyperWorks to design the structure and run a finite-element analysis (FEA) to verify that it would meet ISO 3471 specification. After a few days and multiple iterations, HTM had a structure that exceeded the ISO specification in calculation. The required physical tests on the prototype confirmed that all the nonlinear behaviors of the structure had been correctly predicted using HyperWorks tools. HTM also used Altair HyperView, a visualization environment for simulation and test data, to share analysis results with managers. Altair MotionView and MotionSolve were used for multibody analysis of the entire truck.
Operational Impact
Quantitative Benefit
Related Case Studies.
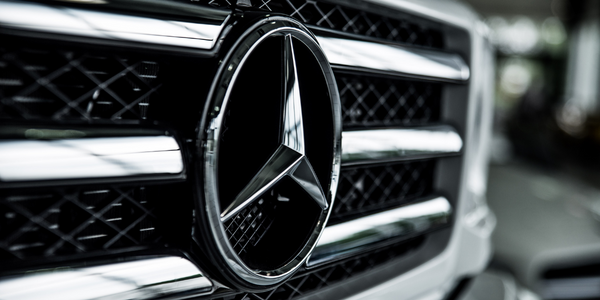
Case Study
Integral Plant Maintenance
Mercedes-Benz and his partner GAZ chose Siemens to be its maintenance partner at a new engine plant in Yaroslavl, Russia. The new plant offers a capacity to manufacture diesel engines for the Russian market, for locally produced Sprinter Classic. In addition to engines for the local market, the Yaroslavl plant will also produce spare parts. Mercedes-Benz Russia and his partner needed a service partner in order to ensure the operation of these lines in a maintenance partnership arrangement. The challenges included coordinating the entire maintenance management operation, in particular inspections, corrective and predictive maintenance activities, and the optimizing spare parts management. Siemens developed a customized maintenance solution that includes all electronic and mechanical maintenance activities (Integral Plant Maintenance).
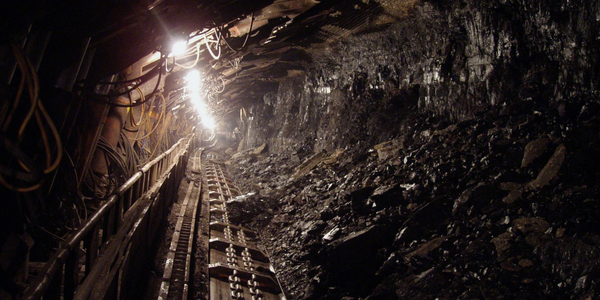
Case Study
Underground Mining Safety
The goal was to produce a safety system to monitor and support underground mining operations; existing systems were either too simple (i.e. phone line) or overly complex and expensive, inhibiting deployment, and providing little-to-no support in event of an accident. Given the dangerous nature of the mining work environment and the strict regulations placed on the industry, the solution would have to comply with Mine Safety and Health Administration (MSHA) regulations. Yet the product needed to allow for simple deployment to truly be a groundbreaking solution - increasing miner safety and changing daily operations for the better.
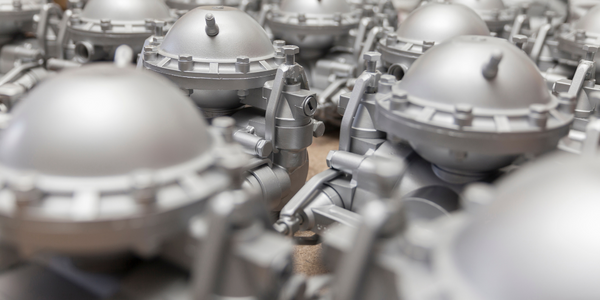
Case Study
Monitoring of Pressure Pumps in Automotive Industry
A large German/American producer of auto parts uses high-pressure pumps to deburr machined parts as a part of its production and quality check process. They decided to monitor these pumps to make sure they work properly and that they can see any indications leading to a potential failure before it affects their process.