Download PDF
Optimizing Manufacturing Process and Design in Investment Casting: A Case Study of Wisconsin Precision Casting Corporation
Technology Category
- Analytics & Modeling - Digital Twin / Simulation
- Sensors - Flow Meters
Applicable Industries
- Buildings
- Equipment & Machinery
Applicable Functions
- Procurement
- Product Research & Development
Use Cases
- Manufacturing Process Simulation
- Time Sensitive Networking
The Challenge
Wisconsin Precision Casting Corporation (WPC), a precision manufacturer of investment castings, was faced with the challenge of reducing costs of regenerative turbine pump cover investment castings. The challenge was to optimize the structural design and manufacturing process to achieve this goal. The regenerative turbine pump cover was a critical component that required high pressure and close tolerances to perform efficiently. The goals for the redesign were to reduce material usage in the pump’s cover, maintain original strength and performance, and improve casting efficiency. The challenge was further compounded by the need to adapt to evolving trends in casting to meet the demands of various industries and customers.
About The Customer
Wisconsin Precision Casting Corporation (WPC) is a primarily family-owned corporation founded in 1964. It is a precision manufacturer of investment castings and services several industries including medical equipment, food and dairy equipment, heavy machinery, industrial pumps, and metal fabrication. WPC has seen significant growth over recent years, especially with the 2015 acquisition of Northern Precision Casting. With the acquisition and increased demand for their products and services, WPC has expanded and now operates in two Wisconsin-based facilities to better serve their customer base. WPC provides customers with solutions to save time, money, and stress, offering support throughout the entire casting process.
The Solution
WPC employed solidThinking Inspire for shape optimization and solidThinking Click2Cast® for filling analysis and detailed solidification results. The redesign process was divided into three phases. In the first phase, WPC inherited the original design from its customer and quickly recognized the need for a more efficient pouring process. WPC reduced the number of ingates and changed the part orientation on the sprue to allow for more parts per pour. The second phase focused on the optimization of the pump cover structure. Using solidThinking Inspire, loads and critical features for casting were identified and a baseline analysis on the proven design was completed. The pump cover was then optimized in Inspire, resulting in an 8% mass reduction and increased strength. In the final phase, Inspire was used to redesign the geometry of the pump cover with PolyNURB wraps over the optimized geometry. A casting analysis was conducted in Click2Cast to verify that the cavity and sprue design were suitable for pouring.
Operational Impact
Quantitative Benefit
Related Case Studies.
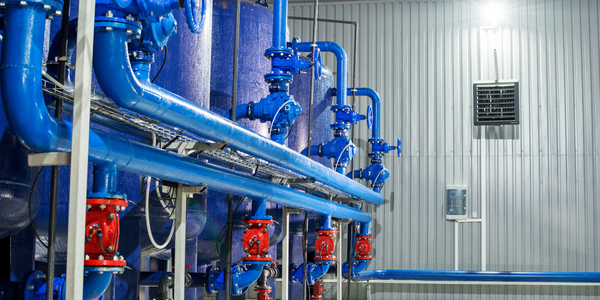
Case Study
Smart Water Filtration Systems
Before working with Ayla Networks, Ozner was already using cloud connectivity to identify and solve water-filtration system malfunctions as well as to monitor filter cartridges for replacements.But, in June 2015, Ozner executives talked with Ayla about how the company might further improve its water systems with IoT technology. They liked what they heard from Ayla, but the executives needed to be sure that Ayla’s Agile IoT Platform provided the security and reliability Ozner required.
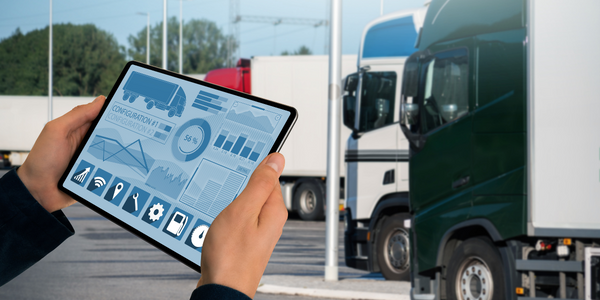
Case Study
IoT enabled Fleet Management with MindSphere
In view of growing competition, Gämmerler had a strong need to remain competitive via process optimization, reliability and gentle handling of printed products, even at highest press speeds. In addition, a digitalization initiative also included developing a key differentiation via data-driven services offers.
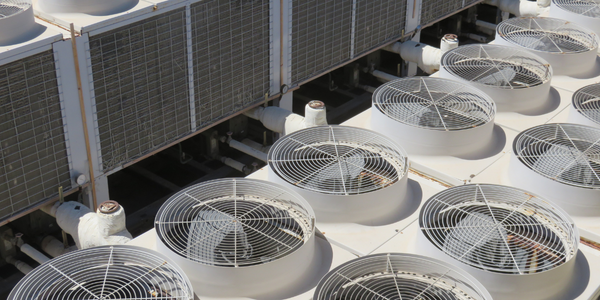
Case Study
Predictive Maintenance for Industrial Chillers
For global leaders in the industrial chiller manufacturing, reliability of the entire production process is of the utmost importance. Chillers are refrigeration systems that produce ice water to provide cooling for a process or industrial application. One of those leaders sought a way to respond to asset performance issues, even before they occur. The intelligence to guarantee maximum reliability of cooling devices is embedded (pre-alarming). A pre-alarming phase means that the cooling device still works, but symptoms may appear, telling manufacturers that a failure is likely to occur in the near future. Chillers who are not internet connected at that moment, provide little insight in this pre-alarming phase.
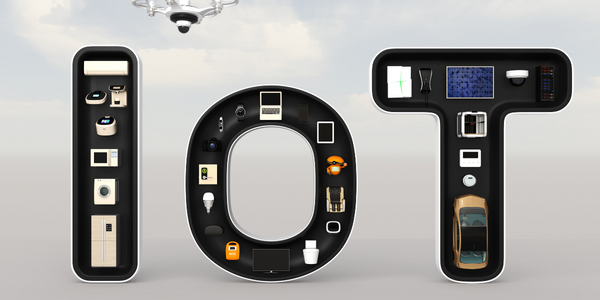
Case Study
Premium Appliance Producer Innovates with Internet of Everything
Sub-Zero faced the largest product launch in the company’s history:It wanted to launch 60 new products as scheduled while simultaneously opening a new “greenfield” production facility, yet still adhering to stringent quality requirements and manage issues from new supply-chain partners. A the same time, it wanted to increase staff productivity time and collaboration while reducing travel and costs.
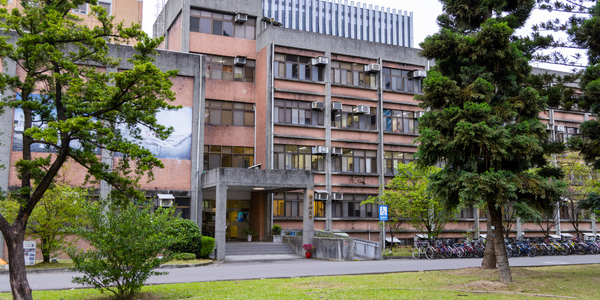
Case Study
Energy Saving & Power Monitoring System
Recently a university in Taiwan was experiencing dramatic power usage increases due to its growing number of campus buildings and students. Aiming to analyze their power consumption and increase their power efficiency across 52 buildings, the university wanted to build a power management system utilizing web-based hardware and software. With these goals in mind, they contacted Advantech to help them develop their system and provide them with the means to save energy in the years to come.
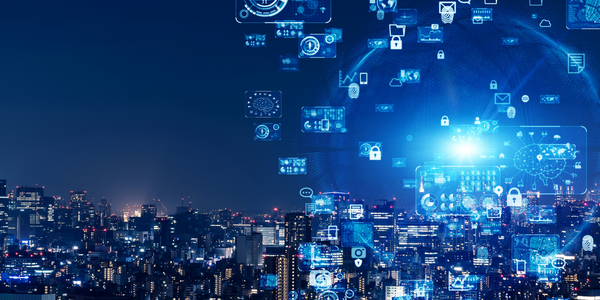
Case Study
Integration of PLC with IoT for Bosch Rexroth
The application arises from the need to monitor and anticipate the problems of one or more machines managed by a PLC. These problems, often resulting from the accumulation over time of small discrepancies, require, when they occur, ex post technical operations maintenance.