Download PDF
Optimizing Production Process with NovaFlow&Solid at Automotive Components Floby AB
Technology Category
- Analytics & Modeling - Digital Twin / Simulation
- Sensors - Voltage Sensors
Applicable Industries
- Automotive
- Equipment & Machinery
Use Cases
- Manufacturing Process Simulation
- Time Sensitive Networking
The Challenge
Automotive Components Floby AB (AC Floby), a Swedish company with over 60 years of experience in manufacturing products for the automotive industry, was facing a significant challenge. The company was losing critical production time while constructing brake components for cars. This inefficiency was affecting their overall productivity and profitability. The company was in search of a solution that could stabilize and optimize their production process. Initially, they hired NovaCast for simulations on a consulting basis. However, as the need for professional simulations increased, they realized the need for a more permanent and efficient solution.
About The Customer
Automotive Components Floby AB (AC Floby) is a Swedish company that has been in operation for over 60 years. The company is based in the town of Floby, which has a population of just over 1500 inhabitants. AC Floby specializes in manufacturing products for the automotive industry, including brake discs, wheel hubs, and connecting rods. The company serves manufacturers throughout Europe and beyond, adhering to the highest industry standards of quality, precision, and environmental impact. AC Floby has a workforce of 510 employees and generates a revenue of 2,057 MSEK.
The Solution
In response to the challenge, AC Floby decided to invest in NovaCast's process simulation tool, NovaFlow&Solid, for in-house use. This tool simulates mold filling and solidification, which are critical steps in the production of brake components. The tool is designed to save crucial time in production and make the process more cost-efficient. The time-saving aspect of the tool comes from its ability to switch mesh in the simulation and during filling in several steps. Depending on the section of the component being worked on, the tool can use a bigger mesh resolution for thick-walled sections and a finer mesh for sensitive areas. In addition to NovaFlow&Solid, AC Floby also chose NovaCast's Technology Partner Agreement (TPA). This agreement not only guarantees support but also provides software updates, invitations to webinars, and discounted user meetings.
Operational Impact
Related Case Studies.
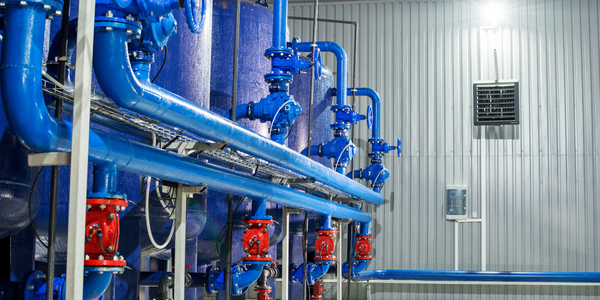
Case Study
Smart Water Filtration Systems
Before working with Ayla Networks, Ozner was already using cloud connectivity to identify and solve water-filtration system malfunctions as well as to monitor filter cartridges for replacements.But, in June 2015, Ozner executives talked with Ayla about how the company might further improve its water systems with IoT technology. They liked what they heard from Ayla, but the executives needed to be sure that Ayla’s Agile IoT Platform provided the security and reliability Ozner required.
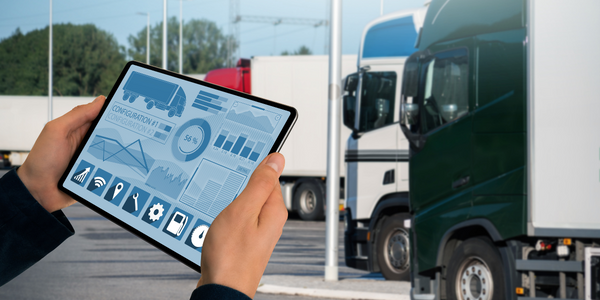
Case Study
IoT enabled Fleet Management with MindSphere
In view of growing competition, Gämmerler had a strong need to remain competitive via process optimization, reliability and gentle handling of printed products, even at highest press speeds. In addition, a digitalization initiative also included developing a key differentiation via data-driven services offers.
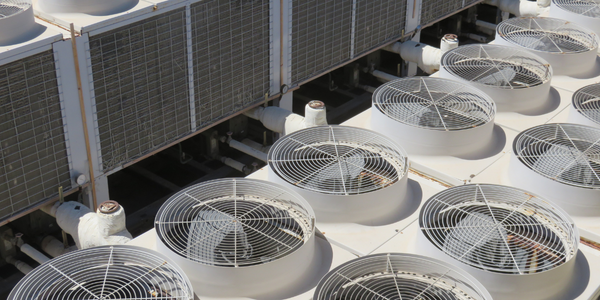
Case Study
Predictive Maintenance for Industrial Chillers
For global leaders in the industrial chiller manufacturing, reliability of the entire production process is of the utmost importance. Chillers are refrigeration systems that produce ice water to provide cooling for a process or industrial application. One of those leaders sought a way to respond to asset performance issues, even before they occur. The intelligence to guarantee maximum reliability of cooling devices is embedded (pre-alarming). A pre-alarming phase means that the cooling device still works, but symptoms may appear, telling manufacturers that a failure is likely to occur in the near future. Chillers who are not internet connected at that moment, provide little insight in this pre-alarming phase.
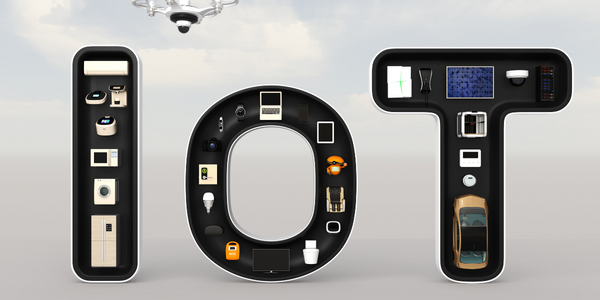
Case Study
Premium Appliance Producer Innovates with Internet of Everything
Sub-Zero faced the largest product launch in the company’s history:It wanted to launch 60 new products as scheduled while simultaneously opening a new “greenfield” production facility, yet still adhering to stringent quality requirements and manage issues from new supply-chain partners. A the same time, it wanted to increase staff productivity time and collaboration while reducing travel and costs.
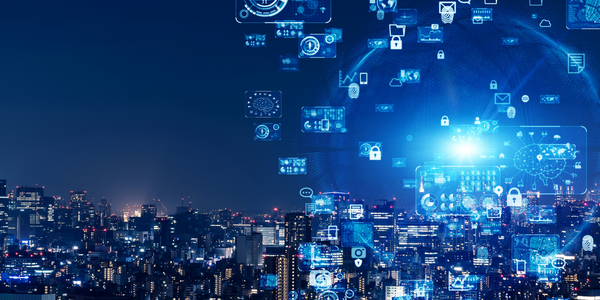
Case Study
Integration of PLC with IoT for Bosch Rexroth
The application arises from the need to monitor and anticipate the problems of one or more machines managed by a PLC. These problems, often resulting from the accumulation over time of small discrepancies, require, when they occur, ex post technical operations maintenance.
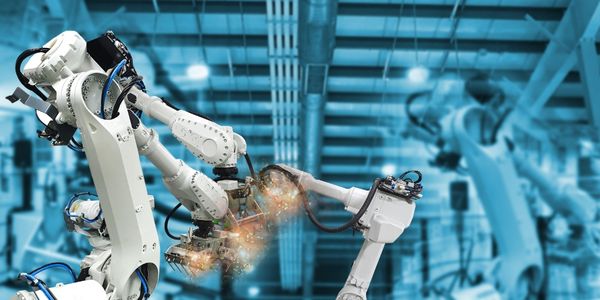
Case Study
Robot Saves Money and Time for US Custom Molding Company
Injection Technology (Itech) is a custom molder for a variety of clients that require precision plastic parts for such products as electric meter covers, dental appliance cases and spools. With 95 employees operating 23 molding machines in a 30,000 square foot plant, Itech wanted to reduce man hours and increase efficiency.