Download PDF
Optimizing Robotic Car Storage Service: A Stanley Robotics Case Study
Technology Category
- Robots - Autonomous Guided Vehicles (AGV)
- Sensors - Autonomous Driving Sensors
Applicable Industries
- Automotive
- Transportation
Applicable Functions
- Logistics & Transportation
- Maintenance
Use Cases
- Autonomous Robots
- Digital Twin
The Challenge
Stanley Robotics, a deep tech company, aimed to revolutionize the vehicle logistics industry by introducing autonomous robots to move cars in storage compounds. The challenge was to develop a robot that was fast, reliable, and efficient to meet the demands of the car logistics industry. The robot needed to be designed with mechanical optimization in mind to compete effectively with traditional car logistics companies. Stanley Robotics needed to prove that its robotic vehicle could achieve a significant number of moves per year and demonstrate its durability. To achieve this, the company needed a partner to help develop a digital twin of their robot to calculate all the demands placed upon it and validate their product through durability calculations.
About The Customer
Stanley Robotics is a deep tech company founded in 2015 by Clement Boussard and Aurélien Cord. The company's original idea was to move cars via an intelligent robot instead of automating the cars and giving them the ability to park themselves. After analyzing the market for long-duration parking in airports, Stanley Robotics realized its product was perfect for the car logistics industry. Their outdoor robots can move cars up to 2600kg and deposit them to their parking slot with the help of a central intelligence hub that manages the fleet, cars, and parking activities.
The Solution
Stanley Robotics partnered with Altair, an engineering simulation software supplier. They used Altair's Inspire Motion to enable the robot multi-body model to be used for pre-sizing. The model was further enhanced with Altair's MotionSolve to enable advanced functions, including performing 3D road definition, longitudinal and lateral tire forces (to simulate handling and durability), and dedicated simulation scenarios. The Stanley team refined the model by representing key components as flexible bodies to capture the deformations and vibrations of the robot’s chassis when exposed to standardized vehicle durability events. With the complete CAE process in place, it became possible to investigate the robot’s sensitivity and robustness, and to identify optimal design characteristics.
Operational Impact
Quantitative Benefit
Related Case Studies.
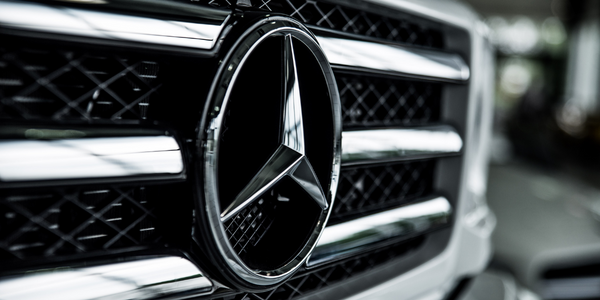
Case Study
Integral Plant Maintenance
Mercedes-Benz and his partner GAZ chose Siemens to be its maintenance partner at a new engine plant in Yaroslavl, Russia. The new plant offers a capacity to manufacture diesel engines for the Russian market, for locally produced Sprinter Classic. In addition to engines for the local market, the Yaroslavl plant will also produce spare parts. Mercedes-Benz Russia and his partner needed a service partner in order to ensure the operation of these lines in a maintenance partnership arrangement. The challenges included coordinating the entire maintenance management operation, in particular inspections, corrective and predictive maintenance activities, and the optimizing spare parts management. Siemens developed a customized maintenance solution that includes all electronic and mechanical maintenance activities (Integral Plant Maintenance).
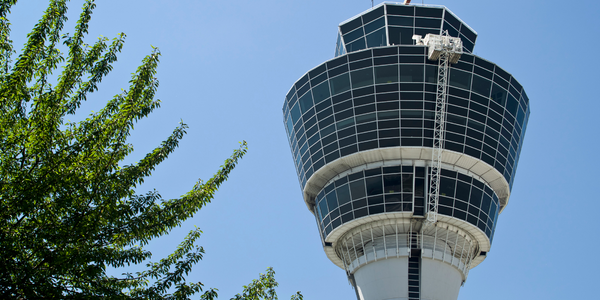
Case Study
Airport SCADA Systems Improve Service Levels
Modern airports are one of the busiest environments on Earth and rely on process automation equipment to ensure service operators achieve their KPIs. Increasingly airport SCADA systems are being used to control all aspects of the operation and associated facilities. This is because unplanned system downtime can cost dearly, both in terms of reduced revenues and the associated loss of customer satisfaction due to inevitable travel inconvenience and disruption.
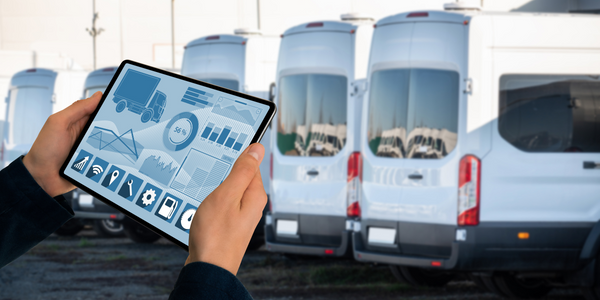
Case Study
IoT-based Fleet Intelligence Innovation
Speed to market is precious for DRVR, a rapidly growing start-up company. With a business model dependent on reliable mobile data, managers were spending their lives trying to negotiate data roaming deals with mobile network operators in different countries. And, even then, service quality was a constant concern.
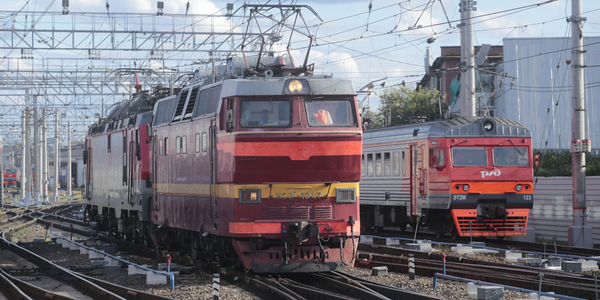
Case Study
Digitize Railway with Deutsche Bahn
To reduce maintenance costs and delay-causing failures for Deutsche Bahn. They need manual measurements by a position measurement system based on custom-made MEMS sensor clusters, which allow autonomous and continuous monitoring with wireless data transmission and long battery. They were looking for data pre-processing solution in the sensor and machine learning algorithms in the cloud so as to detect critical wear.