Download PDF
Panasonic Ecology Systems Enhances Product Development with Virtual Validation
Technology Category
- Automation & Control - Human Machine Interface (HMI)
- Sensors - Utility Meters
Applicable Industries
- Electronics
- Packaging
Applicable Functions
- Maintenance
- Product Research & Development
Use Cases
- Tank Level Monitoring
- Virtual Prototyping & Product Testing
Services
- Hardware Design & Engineering Services
- Testing & Certification
The Challenge
Panasonic Ecology Systems Co., Ltd. was faced with the challenge of making product drop tests more reliable. The company, which plays a key role in the sales of Indoor Air Quality (IAQ) products and solutions globally, understood the importance of evaluating designs through drop-testing before completion to reduce losses. However, the traditional methods of drop-testing were not providing the desired level of reliability. The company was already using RADIOSS, a leading structural analysis solver for highly non-linear problems under dynamic loadings such as impact analysis, as part of their computer-aided engineering tools. The challenge was to make effective use of these resources without the need for new investment, and apply this analysis to product development in other product fields.
About The Customer
Panasonic Ecology Systems Co., Ltd. is a subsidiary of the Eco Solutions Company of Panasonic Corporation. The company plays a pivotal role within the Panasonic Group, being responsible for the global sales of Indoor Air Quality (IAQ) products and solutions. Their mission is to provide comfortable living spaces for people around the world while minimizing the impact on the environment. The company is committed to the development and manufacturing of high-quality products, and as such, they are constantly seeking ways to improve their product development processes, reduce costs, and shorten design and development cycles.
The Solution
The solution involved developing a multi-step plan to analyze a product at each stage of its development. The team began by drop-testing a single component, then moved on to a combination of several components, an assembled product, and a packaged product. At each step, Altair’s RADIOSS solver was employed to calculate the drop-test impact. The team investigated drop analysis for a single component, for example, setting up a drop-test of the front panel of a ventilator installed on a ceiling. The panel was made of ABS resin and was dropped from a height of 1 meter. The team then analyzed the front panel with its two wire attachments and two 20 cm.–long wires that were designed to prevent it from falling off. The strength of the wire attachment was important, as this preventive measure would be meaningless if the attachments broke from the shock when the wires stretched after the panel drops.
Operational Impact
Quantitative Benefit
Related Case Studies.
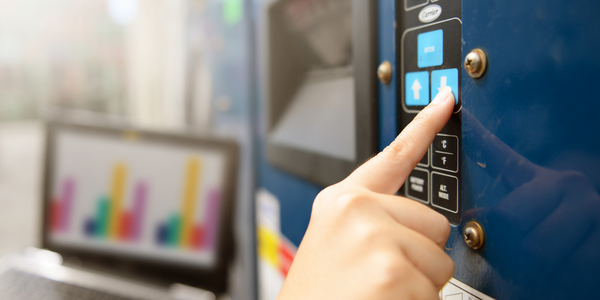
Case Study
Remote Temperature Monitoring of Perishable Goods Saves Money
RMONI was facing temperature monitoring challenges in a cold chain business. A cold chain must be established and maintained to ensure goods have been properly refrigerated during every step of the process, making temperature monitoring a critical business function. Manual registration practice can be very costly, labor intensive and prone to mistakes.
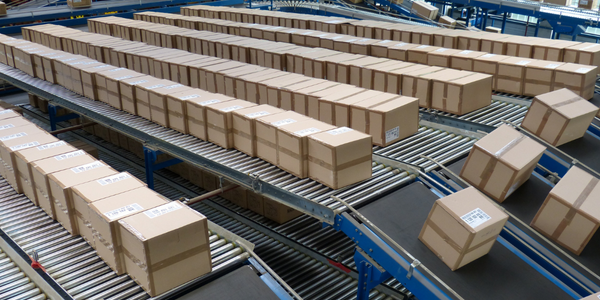
Case Study
IoT Data Analytics Case Study - Packaging Films Manufacturer
The company manufactures packaging films on made to order or configure to order basis. Every order has a different set of requirements from the product characteristics perspective and hence requires machine’s settings to be adjusted accordingly. If the film quality does not meet the required standards, the degraded quality impacts customer delivery causes customer dissatisfaction and results in lower margins. The biggest challenge was to identify the real root cause and devise a remedy for that.
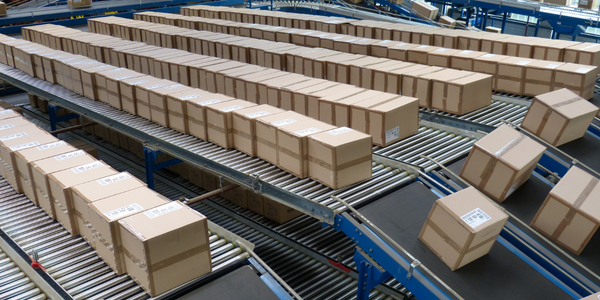
Case Study
Zenon the Ideal Basis for An Ergonomic HMI
KHS develops and produces machines and equipment for filling and packaging in the drinks industry. Because drinks manufacturing, filling and packaging consist of a number of highly complex processes, the user-friendly and intuitive operation of equipment is increasingly gaining in significance. In order to design these processes as simple as possible for the user, KHS decided to introduce a uniform, transparent and standardized solution to the company. The HMI interface should meet the requirement for people with different qualifications and enable them to work on a standard platform.
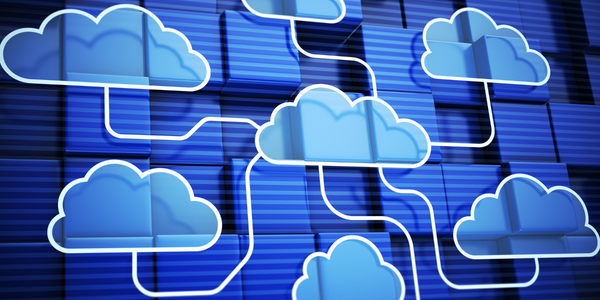
Case Study
Cloud Solution for Energy Management Platform-Schneider Electric
Schneider Electric required a cloud solution for its energy management platform to manage high computational operations, which were essential for catering to client requirements. As the business involves storage and analysis of huge amounts of data, the company also needed a convenient and scalable storage solution to facilitate operations efficiently.