Download PDF
PETRONAS Refinery Unlocks $8.5 Million USD Per Year in Profit with Scheduling Automation Solution
Technology Category
- Functional Applications - Enterprise Resource Planning Systems (ERP)
Applicable Industries
- Oil & Gas
Applicable Functions
- Process Manufacturing
Use Cases
- Demand Planning & Forecasting
- Process Control & Optimization
Services
- System Integration
The Challenge
PETRONAS Melaka Refineries faced the challenge of creating an integrated refinery scheduling model to eliminate many standalone spreadsheets and leverage multi-user interaction under a single network. The process was long and tedious, and led to different versions of the same schedule — which increased the likelihood for errors and resulted in less than optimal crude production.
About The Customer
PETRONAS is the national oil company of Malaysia and holds ownership and control of the petroleum resources for the entire country. It has grown from being the manager and regulator of Malaysia’s upstream sector into an oil and gas corporation, ranking among the FORTUNE Global 500. Recently, PETRONAS Melaka Refineries faced the challenge of creating an integrated refinery scheduling model to eliminate many standalone spreadsheets and leverage multi-user interaction under a single network. Any petroleum scheduling software considered had to be compatible with their current planning tool.
The Solution
To reduce error and improve collaboration, PETRONAS implemented Aspen Petroleum Scheduler and Aspen Refinery Multi-Blend Optimizer to automate the scheduling model under a single database. To better align planning and scheduling, AspenTech helped develop a customized template to integrate both Aspen Petroleum Scheduler and Aspen Refinery Multi-Blend Optimizer with PETRONAS’ current planning tool. The software allowed greater visibility and agility into the refinery model, yielding higher margins and lower production costs. Now schedulers can plot planned, scheduled and actual targets, while seeing variances as they occur and make necessary changes in a single network for better scheduler collaboration. As schedulers make changes, automated alerts notify the other schedulers of the changes, making it easier to adjust the schedule.
Operational Impact
Quantitative Benefit
Related Case Studies.
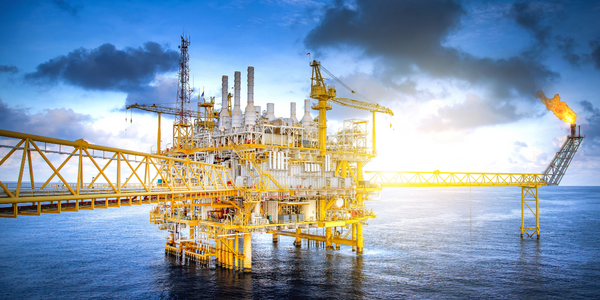
Case Study
Taking Oil and Gas Exploration to the Next Level
DownUnder GeoSolutions (DUG) wanted to increase computing performance by 5 to 10 times to improve seismic processing. The solution must build on current architecture software investments without sacrificing existing software and scale computing without scaling IT infrastructure costs.
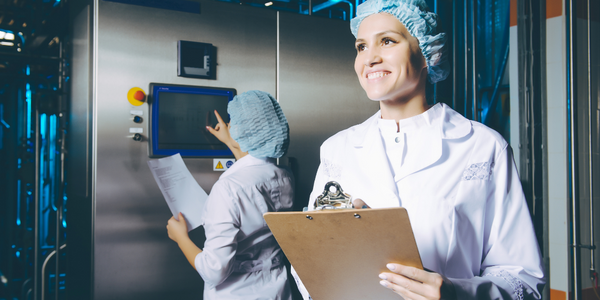
Case Study
Remote Wellhead Monitoring
Each wellhead was equipped with various sensors and meters that needed to be monitored and controlled from a central HMI, often miles away from the assets in the field. Redundant solar and wind generators were installed at each wellhead to support the electrical needs of the pumpstations, temperature meters, cameras, and cellular modules. In addition to asset management and remote control capabilities, data logging for remote surveillance and alarm notifications was a key demand from the customer. Terra Ferma’s solution needed to be power efficient, reliable, and capable of supporting high-bandwidth data-feeds. They needed a multi-link cellular connection to a central server that sustained reliable and redundant monitoring and control of flow meters, temperature sensors, power supply, and event-logging; including video and image files. This open-standard network needed to interface with the existing SCADA and proprietary network management software.
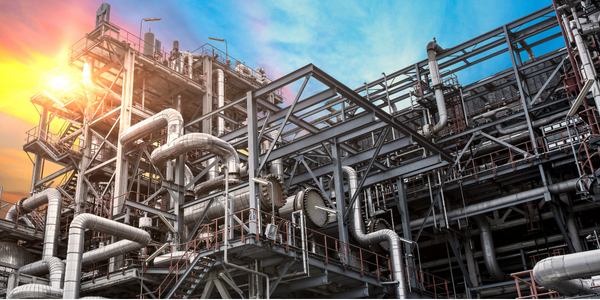
Case Study
Refinery Saves Over $700,000 with Smart Wireless
One of the largest petroleum refineries in the world is equipped to refine various types of crude oil and manufacture various grades of fuel from motor gasoline to Aviation Turbine Fuel. Due to wear and tear, eight hydrogen valves in each refinery were leaking, and each cost $1800 per ton of hydrogen vented. The plant also had leakage on nearly 30 flare control hydrocarbon valves. The refinery wanted a continuous, online monitoring system that could catch leaks early, minimize hydrogen and hydrocarbon production losses, and improve safety for maintenance.