Download PDF
PLM Speeds Development to Transform Solar Power Tracker Technology
Technology Category
- Application Infrastructure & Middleware - Data Exchange & Integration
- Functional Applications - Product Lifecycle Management Systems (PLM)
- Platform as a Service (PaaS) - Data Management Platforms
Applicable Industries
- Renewable Energy
- Utilities
Applicable Functions
- Product Research & Development
- Quality Assurance
Services
- Cloud Planning, Design & Implementation Services
- System Integration
The Challenge
As the number one solar tracker supplier worldwide, Nextracker has doubled its global manufacturing capacity to 300 megawatts per week to serve expanding customer demand. Rapid growth, coupled with the need to collaborate with a global team, meant Nextracker needed to modify its product development practices. The company did not have a single source to track and manage its engineering design and development processes. Product information was tracked manually in workbooks, spreadsheets, and personal file folders, requiring too much reliance on tribal knowledge. With normal employee turnover, process and design information would be lost. “We had to be able to iterate quickly on designs, track changes, and link related product information to scale and speed marketability,” stated Ratana Lee, NPI Archivist for Nextracker.
About The Customer
Nextracker, a Flex Company, is one of the fastest-growing cleantech companies in solar today. Nextracker leads on technology development of next-generation solar power plants with smart solar trackers, energy storage solutions, and TrueCapture™ advanced control software that yields additional energy, optimizes performance, and reduces costs for project and plant owners. Nextracker is globally recognized for delivering intelligent and connected energy systems for over a thousand solar power plants worldwide. Its breakthrough technologies enable plant owners to harvest the sun more efficiently, at lower costs, and with more flexibility.
The Solution
Nextracker was searching for a better way to manage product information with distributed teams, enable automated approvals, and provide better tracking and accountability. In addition, the company needed the ability to integrate to its design and enterprise resource planning (ERP) systems. Arena’s cloud-based product lifecycle management (PLM) solution checked all the boxes. It made internal and external team collaboration simple while providing seamless integration. Lee was hired to drive adoption of PLM. “Using Arena’s cloud-based PLM system to centralize product information and automate design and development processes has accelerated innovation,” said Lee. Nextracker has been able to automatically push the necessary product information to Oracle® NetSuite immediately upon release to support the sales, purchase order (PO), and manufacturing processes. Information flows from their engineering design systems, SOLIDWORKS® and OrCAD®, into Arena to minimize wasted cycle times and improve accuracy of information. Nextracker’s contract manufacturing (CM) partners are scattered throughout the U.S. and India. “Our CMs can go into Arena PLM and securely access the exact information they need. Arena enables us to synchronize product information in ERP, so our teams in India can service customers in their region and the U.S. location can service customers in their region,” noted Lee. “We always get positive feedback from our suppliers on the ability to check drawings, revisions, compare against POs or sales orders, and start work without delay.”
Operational Impact
Quantitative Benefit
Related Case Studies.
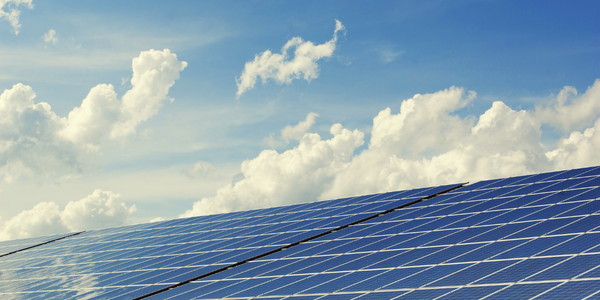
Case Study
Remote Monitoring & Predictive Maintenance App for a Solar Energy System
The maintenance & tracking of various modules was an overhead for the customer due to the huge labor costs involved. Being an advanced solar solutions provider, they wanted to ensure early detection of issues and provide the best-in-class customer experience. Hence they wanted to automate the whole process.

Case Study
IoT Solutions for Smart City | Internet of Things Case Study
There were several challenges faced: It is challenging to build an appliance that can withstand a wide range of voltage fluctuations from as low at 90v to as high as 320v. Since the device would be installed in remote locations, its resilience was of paramount importance. The device would have to deal with poor network coverage and have the ability to store and re-transmit data if networks were not available, which is often the case in rural India. The device could store up to 30 days of data.
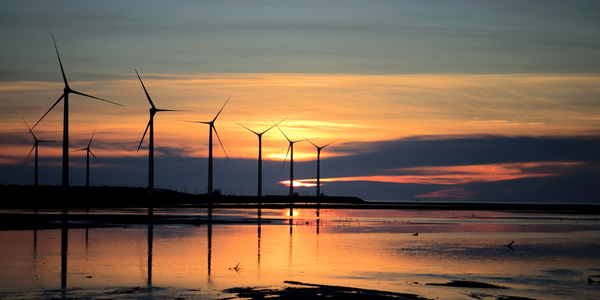
Case Study
Vestas: Turning Climate into Capital with Big Data
Making wind a reliable source of energy depends greatly on the placement of the wind turbines used to produce electricity. Turbulence is a significant factor as it strains turbine components, making them more likely to fail. Vestas wanted to pinpoint the optimal location for wind turbines to maximize power generation and reduce energy costs.
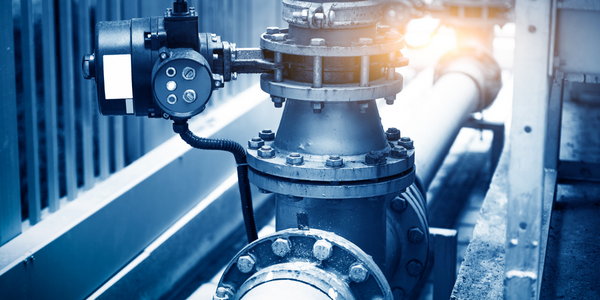
Case Study
Automation of the Oguz-Gabala-Baku water pipeline, Azerbaijan
The Oguz-Gabala-Baku water pipeline project dates back to plans from the 1970’s. Baku’s growth was historically driven by the booming oil industry and required the import of drinking water from outside of the city. Before the construction of the pipeline, some 60 percent of the city’s households received water for only a few hours daily. After completion of the project, 75 percent of the two million Baku residents are now served around the clock with potable water, based on World Health Organization (WHO) standards. The 262-kilometer pipeline requires no pumping station, but uses the altitude differences between the Caucasian mountains and the capital to supply 432,000 m³/d to the Ceyranbatan water reservoir. To the people of Baku, the pipeline is “the most important project not only in 2010, but of the last 20 years.”
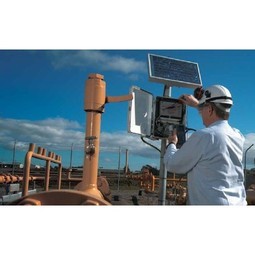
Case Study
GPRS Mobile Network for Smart Metering
Around the world, the electricity supply industry is turning to ‘smart’ meters to lower costs, reduce emissions and improve the management of customer supplies. Smart meters collect detailed consumption information and using this feedback consumers can better understand their energy usage which in turn enables them to modify their consumption to save money and help to cut carbon emissions. A smart meter can be defined in many ways, but generally includes an element of two-way communication between the household meter and the utility provider to efficiently collect detailed energy usage data. Some implementations include consumer feedback beyond the energy bill to include online web data, SMS text messages or an information display in consumers’ premises. Providing a cost-effective, reliable communications mechanism is one of the most challenging aspects of a smart meter implementation. In New Zealand, the utilities have embraced smart metering and designed cost effective ways for it to be implemented. The New Zealand government has encouraged such a move to smart metering by ensuring the energy legislation is consistent with the delivery of benefits to the consumer while allowing innovation in this area. On the ground, AMS is a leader in the deployment of smart metering and associated services. Several of New Zealand’s energy retailers were looking for smart metering services for their residential and small business customers which will eventually account for over 500,000 meters when the multi-year national deployment program is concluded. To respond to these requirements, AMS needed to put together a solution that included data communications between each meter and the central data collection point and the solution proposed by Vodafone satisfied that requirement.
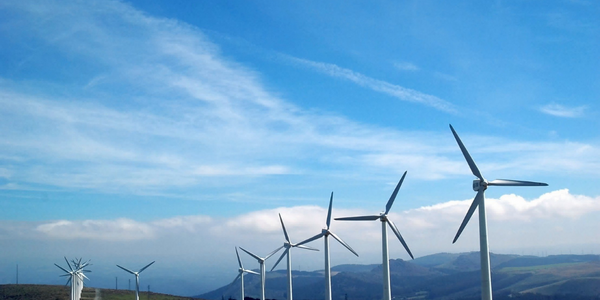
Case Study
Siemens Wind Power
Wind provides clean, renewable energy. The core concept is simple: wind turbines spin blades to generate power. However, today's systems are anything but simple. Modern wind turbines have blades that sweep a 120 meter circle, cost more than 1 million dollars and generate multiple megawatts of power. Each turbine may include up to 1,000 sensors and actuators – integrating strain gages, bearing monitors and power conditioning technology. The turbine can control blade speed and power generation by altering the blade pitch and power extraction. Controlling the turbine is a sophisticated job requiring many cooperating processors closing high-speed loops and implementing intelligent monitoring and optimization algorithms. But the real challenge is integrating these turbines so that they work together. A wind farm may include hundreds of turbines. They are often installed in difficult-to-access locations at sea. The farm must implement a fundamentally and truly distributed control system. Like all power systems, the goal of the farm is to match generation to load. A farm with hundreds of turbines must optimize that load by balancing the loading and generation across a wide geography. Wind, of course, is dynamic. Almost every picture of a wind farm shows a calm sea and a setting sun. But things get challenging when a storm goes through the wind farm. In a storm, the control system must decide how to take energy out of gusts to generate constant power. It must intelligently balance load across many turbines. And a critical consideration is the loading and potential damage to a half-billion-dollar installed asset. This is no environment for a slow or undependable control system. Reliability and performance are crucial.