Download PDF
Qlikview’s Unique User Driven & Intuitive Tools Allow Herotsc Staff to Control Their Individual Data & Has Revolutionised the Way They Now Measure Staff Performance
Technology Category
- Analytics & Modeling - Real Time Analytics
- Application Infrastructure & Middleware - Data Exchange & Integration
Applicable Functions
- Human Resources
- Business Operation
- Sales & Marketing
Use Cases
- Predictive Maintenance
- Personnel Tracking & Monitoring
- Real-Time Location System (RTLS)
Services
- Data Science Services
- System Integration
The Challenge
HEROtsc, a leading Business Process Outsourcing company in the UK, was facing challenges in managing large volumes of data spread over 10 different UK offices. The company needed to radically overhaul the way its data was used to add value to both their clients and their own business. They were looking for an efficient and cost-effective way of uniting, presenting, and communicating complex business data throughout the enterprise without the wide range of challenges associated with manual collation using Excel spreadsheets.
About The Customer
HEROtsc was formed in 1994 with a vision to provide best-in-class contact centre services and technology solutions. Since then, HEROtsc has expanded to create ten contact centres throughout the UK. As one of the UK’s leading Business Process Outsourcing companies, HEROtsc employs over 5,000 front line staff in the UK and India, and is responsible for serving global blue-chip including BskyB and Vodafone. With large volumes of staff and huge amounts of data spread over 10 different UK offices, HEROtsc recognised a need to radically overhaul the way its data was used to add value to both their clients and their own business.
The Solution
In 2006, HEROtsc successfully deployed their first QlikView application to allow multiple streams of qualitative and quantitive data to be accessed, viewed and analysed, in one place by staff nationwide. As an early adopter of QlikView, HEROtsc quickly saw the long term benefits that the business discovery solution could bring to their business in the speed of deployment; significant reduction in administration costs; and uniformity of views - creating a single version of the truth. In 2008, the company further identified how QlikView could be used as a tool to measure employees’ performance, by allowing staff to see their own Key Performance Indicator’s (KPI’s). To achieve this, QlikView’s usage was refined to enable business data to be mapped against the business organisational structure so that managers could readily compare the overall performance of different teams as well as the individual performance of team members.
Operational Impact
Quantitative Benefit
Related Case Studies.
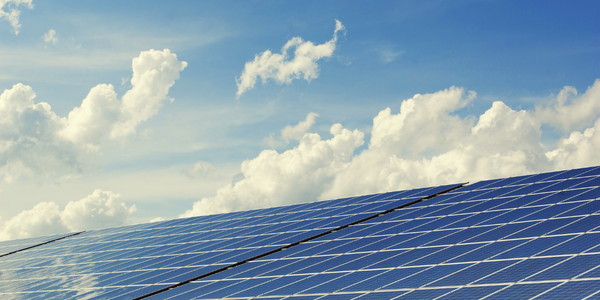
Case Study
Remote Monitoring & Predictive Maintenance App for a Solar Energy System
The maintenance & tracking of various modules was an overhead for the customer due to the huge labor costs involved. Being an advanced solar solutions provider, they wanted to ensure early detection of issues and provide the best-in-class customer experience. Hence they wanted to automate the whole process.
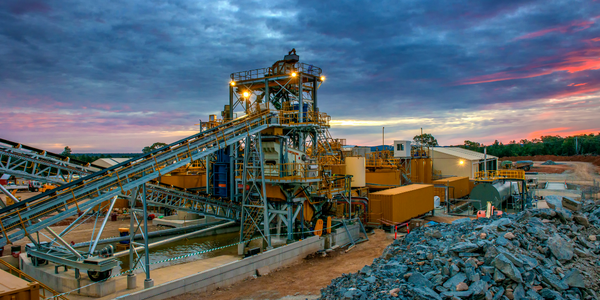
Case Study
Goldcorp: Internet of Things Enables the Mine of the Future
Goldcorp is committed to responsible mining practices and maintaining maximum safety for its workers. At the same time, the firm is constantly exploring ways to improve the efficiency of its operations, extend the life of its assets, and control costs. Goldcorp needed technology that can maximize production efficiency by tracking all mining operations, keep employees safe with remote operations and monitoring of hazardous work areas and control production costs through better asset and site management.
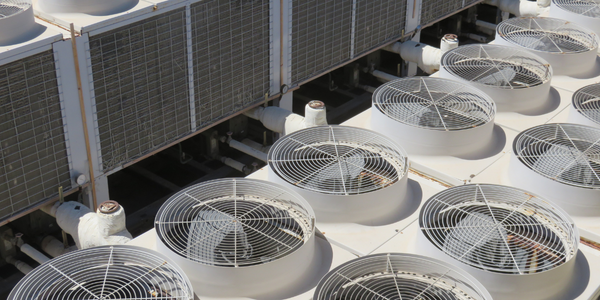
Case Study
Predictive Maintenance for Industrial Chillers
For global leaders in the industrial chiller manufacturing, reliability of the entire production process is of the utmost importance. Chillers are refrigeration systems that produce ice water to provide cooling for a process or industrial application. One of those leaders sought a way to respond to asset performance issues, even before they occur. The intelligence to guarantee maximum reliability of cooling devices is embedded (pre-alarming). A pre-alarming phase means that the cooling device still works, but symptoms may appear, telling manufacturers that a failure is likely to occur in the near future. Chillers who are not internet connected at that moment, provide little insight in this pre-alarming phase.
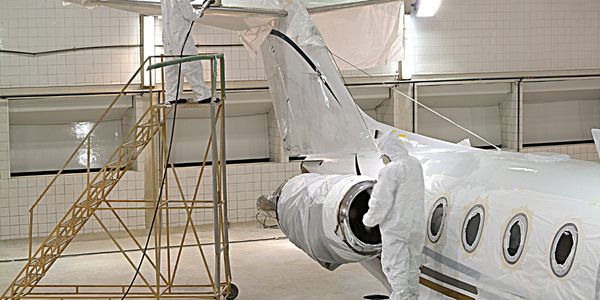
Case Study
Aircraft Predictive Maintenance and Workflow Optimization
First, aircraft manufacturer have trouble monitoring the health of aircraft systems with health prognostics and deliver predictive maintenance insights. Second, aircraft manufacturer wants a solution that can provide an in-context advisory and align job assignments to match technician experience and expertise.
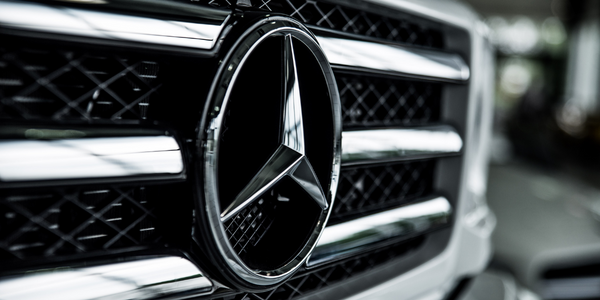
Case Study
Integral Plant Maintenance
Mercedes-Benz and his partner GAZ chose Siemens to be its maintenance partner at a new engine plant in Yaroslavl, Russia. The new plant offers a capacity to manufacture diesel engines for the Russian market, for locally produced Sprinter Classic. In addition to engines for the local market, the Yaroslavl plant will also produce spare parts. Mercedes-Benz Russia and his partner needed a service partner in order to ensure the operation of these lines in a maintenance partnership arrangement. The challenges included coordinating the entire maintenance management operation, in particular inspections, corrective and predictive maintenance activities, and the optimizing spare parts management. Siemens developed a customized maintenance solution that includes all electronic and mechanical maintenance activities (Integral Plant Maintenance).
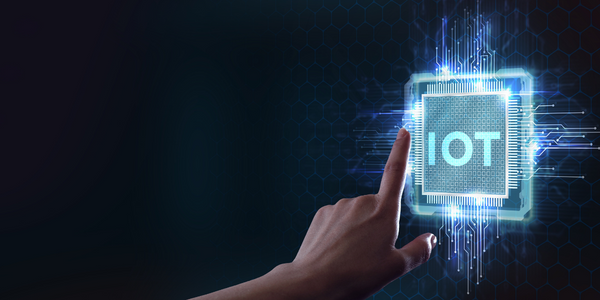
Case Study
Leading Tools Manufacturer Transforms Operations with IoT
Stanley Black & Decker required transparency of real-time overall equipment effectiveness and line productivity to reduce production line change over time.The goal was to to improve production to schedule, reduce actual labor costs and understanding the effects of shift changes and resource shifts from line to line.