Download PDF
Rapid Design and Collaboration: The Ford Focus STREET Case Study
Technology Category
- Robots - Autonomous Guided Vehicles (AGV)
- Sensors - Autonomous Driving Sensors
Applicable Industries
- Automotive
- Glass
Applicable Functions
- Facility Management
- Product Research & Development
Use Cases
- Smart Lighting
- Vehicle Performance Monitoring
The Challenge
The Ford Focus STREET collaborative team faced a significant challenge: they had only six weeks to complete a design for a specialty vehicle based on the Ford Focus platform. The project was a collaboration between Ford Racing, Altair Engineering, Bayer MaterialScience LLC, and PPG Industries. The design had to be unique and stylish, particularly above the belt line of the vehicle, which was critical for the Specialty Equipment Market Association (SEMA) show. The team also had to overcome logistical challenges such as sourcing the right materials in the appropriate color and developing inexpensive tooling for the molding of the parts. PPG had to check its inventory for the raw stock of Solextra, a blue glass that imparts a distinctive look, and adjust its manufacturing processes to fabricate the specialty glass. They also had to formulate and deliver a complementary color for the vehicle’s exterior finish within the tight timeframe.
About The Customer
The customer in this case is Ford Racing, a division of Ford Motor Company that is responsible for its racing operations. Ford Racing sought to develop an aftermarket body kit for distribution through its own channels, marking the first time it had done so. The body kit was to be based on the Ford Focus platform, and Ford Racing supplied Altair with several components as well as proprietary design data to facilitate the design process. The goal was to deliver a specialty vehicle in time for the SEMA show, demonstrating the collaborative efforts and technology of Altair Engineering, Ford Racing, Bayer MaterialScience LLC, and PPG Industries.
The Solution
The team overcame these challenges through effective collaboration and the use of innovative technologies. Bayer MaterialScience utilized its polycarbonate glazing technology to replace traditional glass on the vehicle with a polycarbonate that is injection-moldable. This allowed for unique designs and styling for automotive glazing applications. The polycarbonate and polycarbonate glazing technology, along with Bayer’s processing expertise, enabled Altair to include a highly stylized roof and liftgate/backlight on the vehicle. This resulted in an approximate 40% to 50% reduction in mass relative to glass. PPG managed to deliver both its Solextra glass and automotive paint within the tight timeframe. Ford supplied Altair with several components as well as proprietary design data so that they could design the body kit for the vehicle.
Operational Impact
Quantitative Benefit
Related Case Studies.
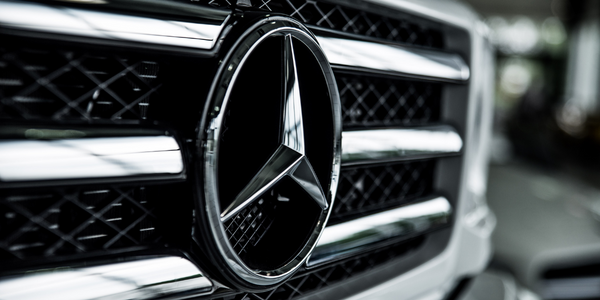
Case Study
Integral Plant Maintenance
Mercedes-Benz and his partner GAZ chose Siemens to be its maintenance partner at a new engine plant in Yaroslavl, Russia. The new plant offers a capacity to manufacture diesel engines for the Russian market, for locally produced Sprinter Classic. In addition to engines for the local market, the Yaroslavl plant will also produce spare parts. Mercedes-Benz Russia and his partner needed a service partner in order to ensure the operation of these lines in a maintenance partnership arrangement. The challenges included coordinating the entire maintenance management operation, in particular inspections, corrective and predictive maintenance activities, and the optimizing spare parts management. Siemens developed a customized maintenance solution that includes all electronic and mechanical maintenance activities (Integral Plant Maintenance).
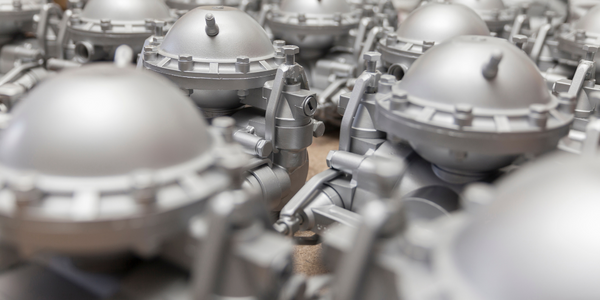
Case Study
Monitoring of Pressure Pumps in Automotive Industry
A large German/American producer of auto parts uses high-pressure pumps to deburr machined parts as a part of its production and quality check process. They decided to monitor these pumps to make sure they work properly and that they can see any indications leading to a potential failure before it affects their process.