Download PDF
Rapidmade/Portland State University Advancing Injection-Mold Technology Research with Solidworks Solutions
Technology Category
- Analytics & Modeling - Predictive Analytics
- Analytics & Modeling - Real Time Analytics
- Functional Applications - Manufacturing Execution Systems (MES)
Applicable Industries
- Plastics
Applicable Functions
- Product Research & Development
- Quality Assurance
Use Cases
- Manufacturing System Automation
- Predictive Maintenance
- Process Control & Optimization
Services
- Software Design & Engineering Services
- System Integration
The Challenge
Conformal cooling channels, which uniformly cool injection molds and the plastic parts inside, have long represented the ultimate productivity goal in injection-molding manufacturing. Cooling channels that conform exactly to the geometry of the injection-molded part would make quick, uniform cooling of the molded plastic possible, resulting in better quality parts, faster cycle times, decreased part waste, and reduced energy consumption. To date, conformal cooling channels have remained just a research idea because the traditional techniques used to machine molds, such as milling and drilling, are incapable of producing all of the geometric shapes required. However, a team of researchers from Portland State University (PSU) and RapidMade, a 3D printing, manufacturing, and engineering company based in Portland, Oregon, have secured a federal grant to conduct research and development aimed at determining how to bring conformal cooling channels to the injection-molding industry.
About The Customer
RapidMade is a 3D printing, manufacturing, and engineering company based in Portland, Oregon. The company specializes in leveraging advanced manufacturing technologies to create innovative solutions for various industries. In collaboration with Portland State University (PSU), RapidMade is working on a federally funded research project to develop methods for implementing conformal cooling channels in plastic injection mold cores using additive manufacturing tooling. The research team includes PSU student and Team Lead Christopher Mullens, PSU Computer Science Associate Professor Bart Massey, and RapidMade Engineering Director David Shapiro. Their goal is to advance the injection-molding industry by creating molds with conformal cooling channels, which would result in better quality parts, faster cycle times, decreased part waste, and reduced energy consumption.
The Solution
The research team chose SOLIDWORKS® injection-molding solutions, including SOLIDWORKS Professional design, SOLIDWORKS Simulation Premium analysis, SOLIDWORKS Flow Simulation computational fluid dynamics (CFD) analysis, and SOLIDWORKS Plastics Premium injection-molding simulation and analysis software. These tools were selected for their adaptability and comprehensive capabilities in CAD, simulation, and plastics injection-molding. The process begins with the creation of a plastic part, from which the mold and cooling channels are modeled using SOLIDWORKS Professional software. The design is then taken into SOLIDWORKS Plastics Premium to evaluate how molten plastic flows into the mold and to optimize the mold design with respect to material flow and cooling channel placement. SOLIDWORKS Flow Simulation is used to analyze how effectively the flow of liquid coolant in the cooling channels cools surrounding walls, and SOLIDWORKS Simulation Premium software supports analyses of the thermal effects of the cooling channels throughout the mold. Simulation findings help guide modifications and support design iterations. The combination of SOLIDWORKS Plastics Premium, SOLIDWORKS Simulation Premium, and SOLIDWORKS Flow Simulation software enables the team to more efficiently and effectively study the interaction of molten plastic and cooling channels in virtual molds.
Operational Impact
Quantitative Benefit
Related Case Studies.
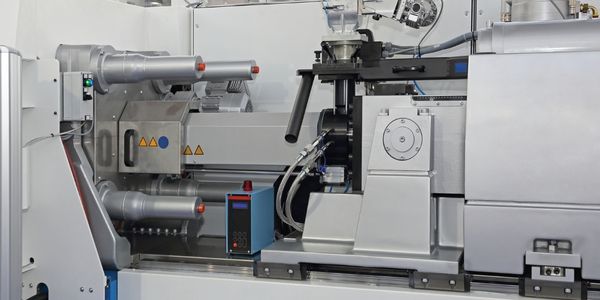
Case Study
Plastic Spoons Case study: Injection Moulding
In order to meet customer expectations by supplying a wide variety of packaging units, from 36 to 1000 spoons per package, a new production and packaging line needed to be built. DeSter wanted to achieve higher production capacity, lower cycle time and a high degree of operator friendliness with this new production line.
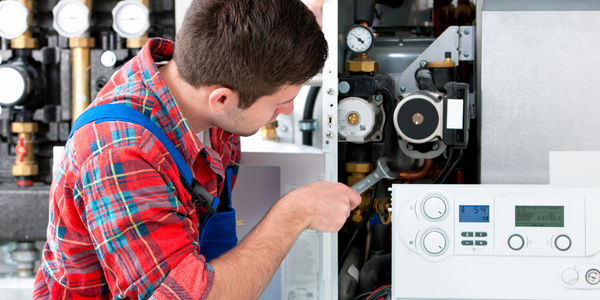
Case Study
Boiler Control System for Plastic Manufacturing Applications
Factory automation applications must be equipped to handle and monitor the myriads of information from attached devices. For plastic manufacturing applications, the boiler control system plays a critical role by gathering and regulating information to ensure production is accurate and smooth. In this particular case, the customer combines eight subsystems that include power meters, water meters, alarm output, displays, and I/O status to be controlled by several intelligent controllers with Modbus RTU interface. The Modbus TCP protocol is used for this application due to the distance. System Requirements: • Modbus serial to Modbus TCP translation • Multiple slaves/masters support • Automatic Modbus TCP response time detection
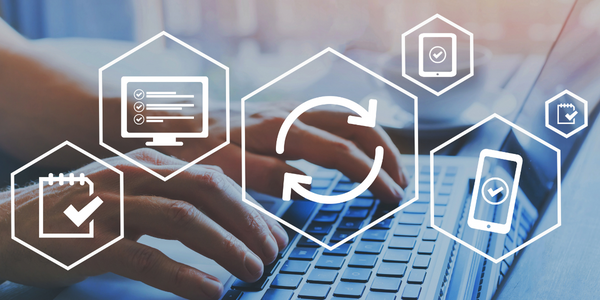
Case Study
Ascend Performance Materials Case Study
Ascend operations must access multiple software systems to manage day-to-day operations in an effective and secure manner. These systems generate large sets of data which contain critical information pertaining to management systems, planning and cost information in business systems and energy consumption. As a result, Ascend management was challenged with creating relevant reports reflecting performance measures in overall context of their operational process. The company’s previous process entailed collecting and analyzing data manually which was not effective, since the information collected was generated after the fact, and was too complex for collaborative use across the organization.
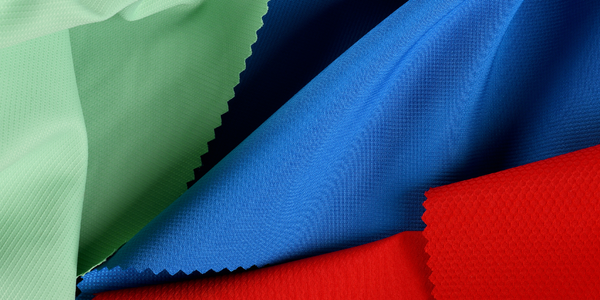
Case Study
Remake Enterprise-to-production System
The client was running a legacy material flow tracking system and wanted to replace the system with a more effective one as the system was increasingly expensive to maintain and support and also was not extendable. The client's IT landscape was filled with modern applications and it was difficult to interface the material flow tracking system with modern applications.