Download PDF
Ready for 510(k) in 90 days
Technology Category
- Functional Applications - Computerized Maintenance Management Systems (CMMS)
- Functional Applications - Enterprise Resource Planning Systems (ERP)
Applicable Industries
- Healthcare & Hospitals
- Life Sciences
Applicable Functions
- Business Operation
- Quality Assurance
Use Cases
- Regulatory Compliance Monitoring
Services
- System Integration
- Training
The Challenge
SimBioSys faced the typical challenge faced by any life science start-up: the blank slate. The company in its fledgling state had no internal regulatory expertise or a functioning quality management system. Besides a handful of documents in a OneDrive folder, the company lacked a real quality structure or documented basics like a quality manual. When VP of Regulatory & Quality Hilary Baldwin joined the team, she brought some valuable eQMS experience with her and recognised the powerful business benefits of going straight to a digital eQMS and sidestepping paper altogether. The remote, software-focused and pro-digital culture of the business supported this decision. Hilary's first task was therefore to position the company for success by implementing a suitable, trusted eQMS platform to build the company's digitized quality system into. Along with VP of Software & IT Michael Hallock, she began the search.
About The Customer
SimBioSys is developing a Class II software as medical device (SaMD) platform to revolutionize 'computational oncology'. By digitally modelling cancer behavior, including tumor growth and medicinal impact, SimBioSys' device will unlock precise, pre-simulated cancer care that saves lives. The company is in its early stages and faced the typical challenges of a life science start-up, including a lack of internal regulatory expertise and a functioning quality management system. The company had a handful of documents in a OneDrive folder but lacked a real quality structure or documented basics like a quality manual. The remote, software-focused, and pro-digital culture of the business supported the decision to go straight to a digital eQMS and sidestep paper altogether.
The Solution
Hilary had implemented MasterControl in a previous role and hadn't enjoyed the experience. It was critical she found a system that was easy to use, could be quickly validated, and would accelerate SimBioSys' journey to market. A colleague from a previous role, Becki, had implemented Qualio at her own company Synthego and passed their first ever FDA submission with flying colors. After a glowing endorsement of Qualio and its ease of use, Hilary wanted to try the system herself. The fast, easy eQMS set-up Hilary needed was delivered by Qualio. Hilary worked with Sumatha in the Qualio+ team for targeted QA/RA support that accelerated SimBioSys' quality and compliance preparations. Sumatha used her 20 years of medical device industry expertise to help populate SimBioSys' shiny new eQMS with templated content, and to advise Hilary and the team on their 510(k) and ISO 13485 journey. As VP of Software & IT at an SaMD technology company, Michael was keen to make efficient, digital work as widespread as possible. After widespread frustration within the team caused by Excel-driven design control work, Qualio provided an integrated, built-for-purpose eQMS platform that provided 'the missing piece of the puzzle' and makes quality and compliance natural, enjoyable and automatic.
Operational Impact
Quantitative Benefit
Related Case Studies.
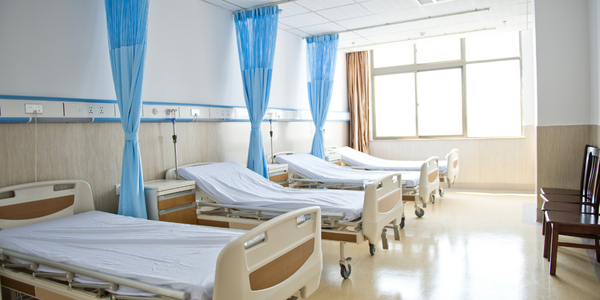
Case Study
Hospital Inventory Management
The hospital supply chain team is responsible for ensuring that the right medical supplies are readily available to clinicians when and where needed, and to do so in the most efficient manner possible. However, many of the systems and processes in use at the cancer center for supply chain management were not best suited to support these goals. Barcoding technology, a commonly used method for inventory management of medical supplies, is labor intensive, time consuming, does not provide real-time visibility into inventory levels and can be prone to error. Consequently, the lack of accurate and real-time visibility into inventory levels across multiple supply rooms in multiple hospital facilities creates additional inefficiency in the system causing over-ordering, hoarding, and wasted supplies. Other sources of waste and cost were also identified as candidates for improvement. Existing systems and processes did not provide adequate security for high-cost inventory within the hospital, which was another driver of cost. A lack of visibility into expiration dates for supplies resulted in supplies being wasted due to past expiry dates. Storage of supplies was also a key consideration given the location of the cancer center’s facilities in a dense urban setting, where space is always at a premium. In order to address the challenges outlined above, the hospital sought a solution that would provide real-time inventory information with high levels of accuracy, reduce the level of manual effort required and enable data driven decision making to ensure that the right supplies were readily available to clinicians in the right location at the right time.
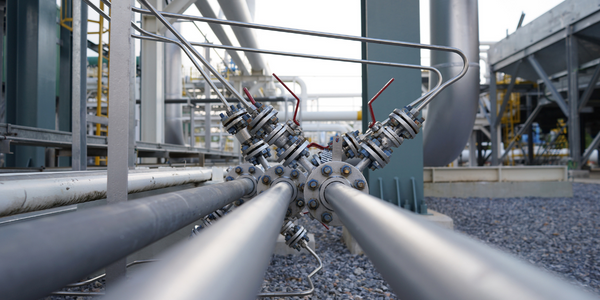
Case Study
Gas Pipeline Monitoring System for Hospitals
This system integrator focuses on providing centralized gas pipeline monitoring systems for hospitals. The service they provide makes it possible for hospitals to reduce both maintenance and labor costs. Since hospitals may not have an existing network suitable for this type of system, GPRS communication provides an easy and ready-to-use solution for remote, distributed monitoring systems System Requirements - GPRS communication - Seamless connection with SCADA software - Simple, front-end control capability - Expandable I/O channels - Combine AI, DI, and DO channels
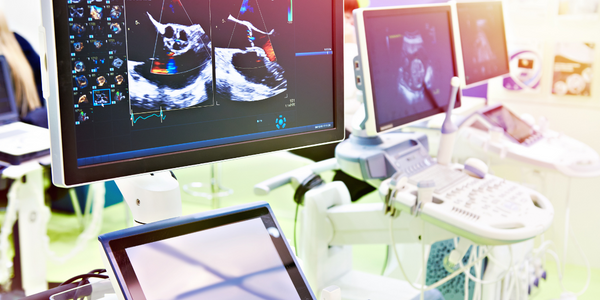
Case Study
Driving Digital Transformations for Vitro Diagnostic Medical Devices
Diagnostic devices play a vital role in helping to improve healthcare delivery. In fact, an estimated 60 percent of the world’s medical decisions are made with support from in vitrodiagnostics (IVD) solutions, such as those provided by Roche Diagnostics, an industry leader. As the demand for medical diagnostic services grows rapidly in hospitals and clinics across China, so does the market for IVD solutions. In addition, the typically high cost of these diagnostic devices means that comprehensive post-sales services are needed. Wanteed to improve three portions of thr IVD:1. Remotely monitor and manage IVD devices as fixed assets.2. Optimizing device availability with predictive maintenance.3. Recommending the best IVD solution for a customer’s needs.
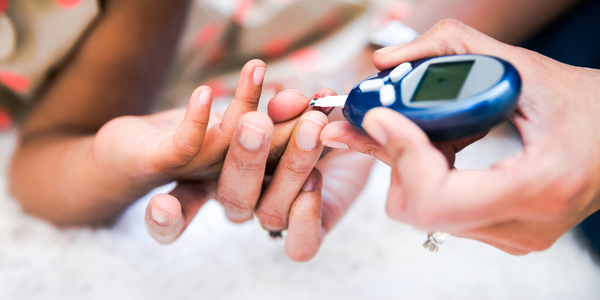
Case Study
HaemoCloud Global Blood Management System
1) Deliver a connected digital product system to protect and increase the differentiated value of Haemonetics blood and plasma solutions. 2) Improve patient outcomes by increasing the efficiency of blood supply flows. 3) Navigate and satisfy a complex web of global regulatory compliance requirements. 4) Reduce costly and labor-intensive maintenance procedures.
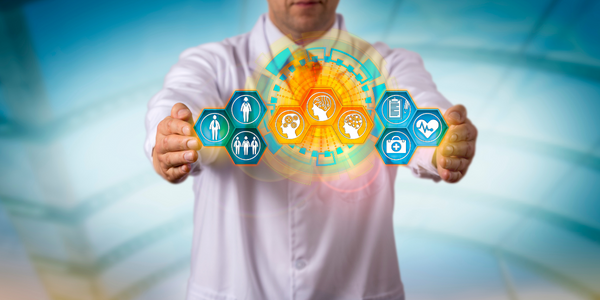
Case Study
Harnessing real-time data to give a holistic picture of patient health
Every day, vast quantities of data are collected about patients as they pass through health service organizations—from operational data such as treatment history and medications to physiological data captured by medical devices. The insights hidden within this treasure trove of data can be used to support more personalized treatments, more accurate diagnosis and more advanced preparative care. But since the information is generated faster than most organizations can consume it, unlocking the power of this big data can be a struggle. This type of predictive approach not only improves patient care—it also helps to reduce costs, because in the healthcare industry, prevention is almost always more cost-effective than treatment. However, collecting, analyzing and presenting these data-streams in a way that clinicians can easily understand can pose a significant technical challenge.