Download PDF
Real-time Data Visibility Across the Recycling Enterprise
Technology Category
- Analytics & Modeling - Real Time Analytics
- Functional Applications - Enterprise Resource Planning Systems (ERP)
- Platform as a Service (PaaS) - Data Management Platforms
Applicable Industries
- Recycling & Waste Management
Applicable Functions
- Business Operation
- Quality Assurance
Use Cases
- Predictive Quality Analytics
- Process Control & Optimization
- Remote Asset Management
Services
- Cloud Planning, Design & Implementation Services
- System Integration
The Challenge
For Strategic Materials, quality was a primary measure of success, but sharing quality data between plants was a significant challenge. Each plant collected information using its own methods and nomenclature, leading to disparate data that was exported into Excel spreadsheets. This made cross-site comparisons nearly impossible. Brad Bell, Director of Quality & Continuous Improvement, needed a quality system that could quickly and easily unite data from all plants.
About The Customer
Founded in 1896, Strategic Materials is the largest recycler of glass in North America. With nearly 50 plants, the company supplies recycled glass to manufacturers of glass containers, fiberglass insulation, highway beads, decorative glass, glass fillers, and other specialty glass. Quality is a primary measure of success for Strategic Materials, and they faced challenges in standardizing quality data across their numerous plants.
The Solution
Brad Bell selected InfinityQS Enact to address the data unification challenge. Within three months, Enact was collecting and analyzing data across 12 plants, and it is now used in 31 plants. Enact provides a centralized data repository, eliminating the need for manual data entry and Excel spreadsheets. The system offers real-time data visibility, enabling quick process corrections and continuous improvement. Enact's flexibility allows differentiation between plants while maintaining standardized data collection and reporting.
Operational Impact
Quantitative Benefit
Related Case Studies.
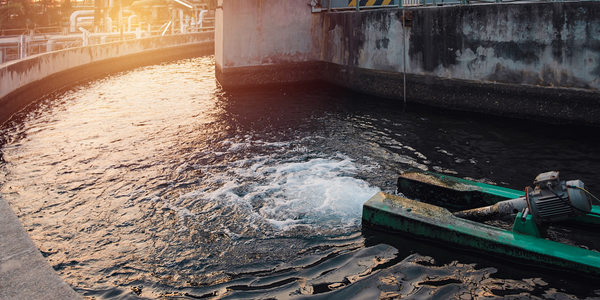
Case Study
Water Treatment Energy Management
Water pumping, treatment and conveyance are among the largest energy and cost outlays for many local and regional municipalities. Electricity time-of-use rates and peak pricing tariffs are driving those costs even higher. This case study describes how Monterey Regional Water Pollution Control Agency (MRWPCA) implemented a process data monitoring and control solution in order to analyze and optimize energy use, reduce deployment costs and save operational expenses.
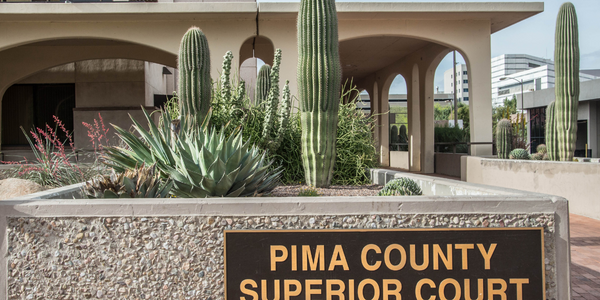
Case Study
Pima County takes significant steps in preserving water source
Pima County is facing the following challenges: - Management of more than 60 million gallons of sewage each day to support the region’s population of more than 1 million people. - To take immediate action when alarms sound alerting operators to issues within the plant The solution should be able to enable the following feature: - To ensure capture of institutional knowledge of current workforce for effective training of future operators - To employ an effective Situational Awareness strategy enabling personnel to effectively understand and address operations of the facility - With assets spread out over more than 700 miles, operational management is difficult
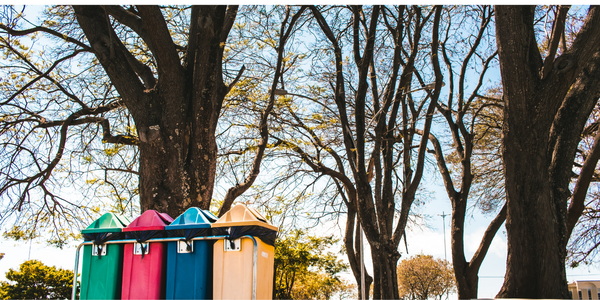
Case Study
A SMART SOLUTION FOR A CIRCULAR ECONOMY
A detailed study conducted by a student from Universidad Pontificia Comillas ICAI in Spain highlighted the need for ecologically safe and sustainable products. While recycling plays an important role in the circular economy, many consumers don’t recycle for a variety of reasons, including lack of space, inconveniently located recycling centers and collection containers, or distrust and/or disbelief in the recycling process. Organizations needed a model that made recycling easier and more accessible for everyone.
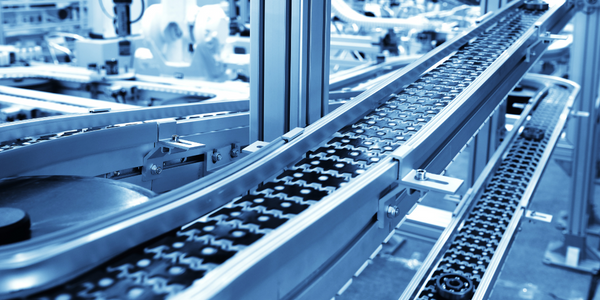
Case Study
Conveyor Belt Monitoring
In a smart environment of management, control and industrial automation, one of the key elements to anticipate failures and increase productivity is to be able to monitor the status and use of conveyor belts of any kind of sector, whether it is for logistics or manufacturing.