Download PDF
Reducing Truck Load Body Costs: A Case Study on VR Steel
Technology Category
- Analytics & Modeling - Virtual & Augmented Reality Software
- Wearables - Virtual Reality Glasses, Headsets & Controllers
Applicable Industries
- Metals
- Mining
Applicable Functions
- Product Research & Development
- Quality Assurance
Use Cases
- Virtual Prototyping & Product Testing
- Virtual Reality
Services
- Hardware Design & Engineering Services
- Testing & Certification
The Challenge
VR Steel (Pty) Ltd, a company that designs, builds, and repairs fabricated mining equipment attachments, including truck load bodies, was faced with a significant challenge. The company aimed to reduce the mass of a truck load body while maintaining its structural integrity and increasing its performance. The challenge was not only to streamline the design process but also to reduce prototyping costs. VR Steel needed a simulation tool that could help them achieve these goals. Their customers also demanded proof that the new design would unload more quickly, lower operating costs, and withstand heavy use. The challenge was to find a solution that could meet all these requirements while also providing a competitive edge in the market.
About The Customer
VR Steel (Pty) Ltd is a company that specializes in designing, building, and repairing fabricated mining equipment attachments, including truck load bodies. The company is committed to innovation and continuously seeks ways to improve its products and services. VR Steel values efficiency and cost-effectiveness, striving to reduce prototyping costs and streamline the design process. The company also places a high priority on customer satisfaction, aiming to provide products that not only meet but exceed customer expectations in terms of performance, durability, and operating costs.
The Solution
VR Steel turned to Altair EDEM™ virtual prototypes to address their challenge. The engineers at VR Steel imported 3D CAD models of the new load body design and generated EDEM material models of various media for testing. Using EDEM simulations as virtual prototypes, they were able to simulate the loading and unloading patterns of both the conventional load body and their new, lighter design. EDEM provided a virtual environment for conducting 100% repeatable tests with a variety of materials, all at a fraction of traditional physical prototyping and testing costs. This solution not only helped VR Steel meet their design goals but also gave them a distinct market advantage by enabling them to quickly design and test a new load body that outperforms competitor designs.
Operational Impact
Quantitative Benefit
Related Case Studies.
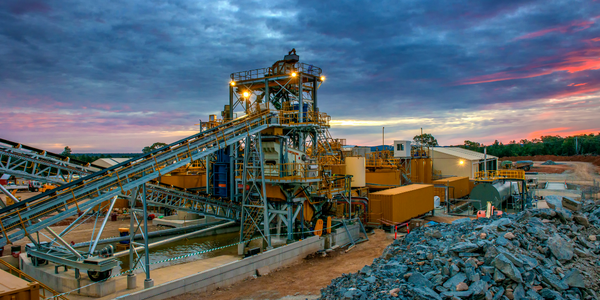
Case Study
Goldcorp: Internet of Things Enables the Mine of the Future
Goldcorp is committed to responsible mining practices and maintaining maximum safety for its workers. At the same time, the firm is constantly exploring ways to improve the efficiency of its operations, extend the life of its assets, and control costs. Goldcorp needed technology that can maximize production efficiency by tracking all mining operations, keep employees safe with remote operations and monitoring of hazardous work areas and control production costs through better asset and site management.
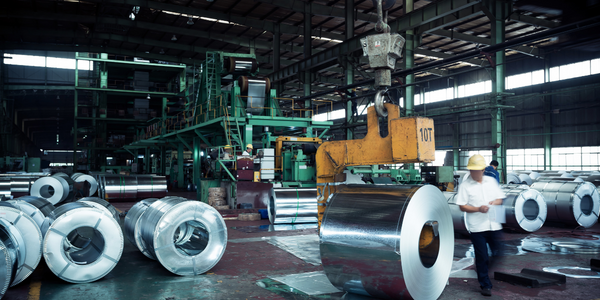
Case Study
KSP Steel Decentralized Control Room
While on-site in Pavlodar, Kazakhstan, the DAQRI team of Business Development and Solutions Architecture personnel worked closely with KSP Steel’s production leadership to understand the steel production process, operational challenges, and worker pain points.
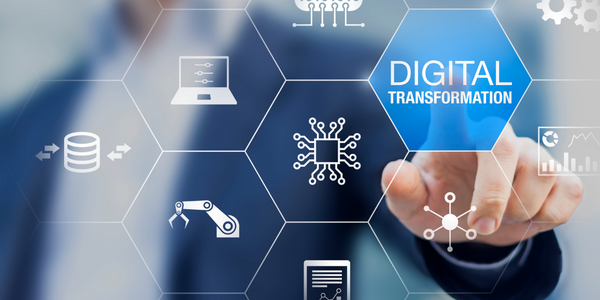
Case Study
Bluescope Steel on Path to Digitally Transform Operations and IT
Increasing competition and fluctuations in the construction market prompted BlueScope Steel to look toward digital transformation of its four businesses, including modern core applications and IT infrastructure. BlueScope needed to modernize its infrastructure and adopt new technologies to improve operations and supply chain efficiency while maintaining and updating an aging application portfolio.
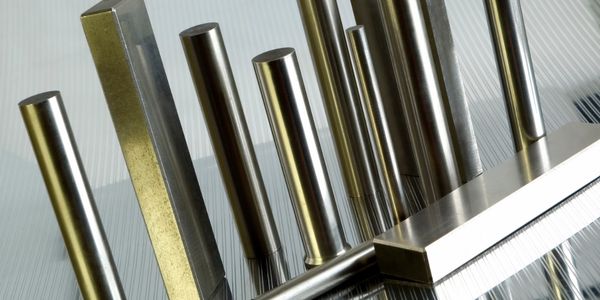
Case Study
RobotStudio Case Study: Benteler Automobiltechnik
Benteler has a small pipe business area for which they produce fuel lines and coolant lines made of aluminum for Porsche and other car manufacturers. One of the problems in production was that when Benteler added new products, production had too much downtime.
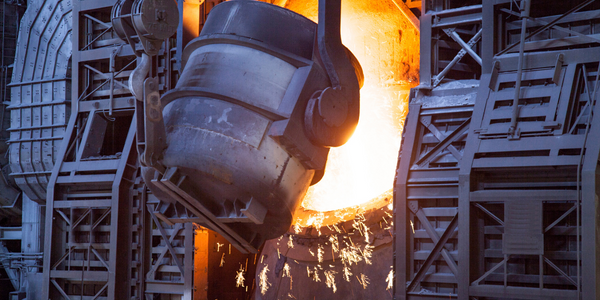
Case Study
Continuous Casting Machines in a Steel Factory
With a very broad range of applications, steel is an important material and has been developed into the most extensive alloy in the engineering world. Since delivering high quality is absolutely crucial for steel plants, ensuring maximum productivity and the best quality production are the keys to competitiveness in the steel industry. Additionally, working conditions in steel factories are not suitable for workers to stay in for long periods of time, so manufactures usually adopt various machines to complete the steel production processes. However, the precision of these machines is often overestimated and the lack of flexibility also makes supervisors unable to adjust operating procedures. A renowned steel factory in Asia planned to improve its Distributed Control System (DCS) of furnaces as well as addressing the problem of insufficient accuracy. However, most well-known international equipment suppliers can not provide a satisfactory solution and local maintenance because the project needed new technologies to more accurately control equipment operations. By implementing Advantech’s automated monitoring and control solution, steel factories can not only improve the manufacturing processes but can also allow users to add additional functions to the existing system so as to make sure the operation runs at high efficiency.
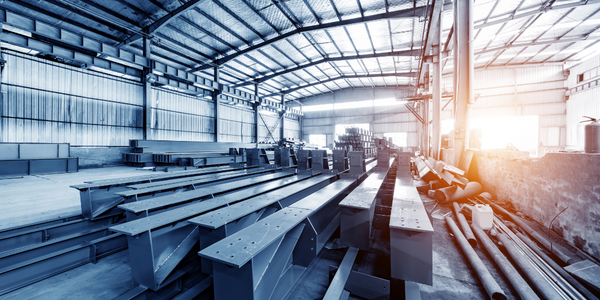
Case Study
Automated Predicitive Analytics For Steel/Metals Industry
Asset to be monitored: Wire Compactor that produces Steel RebarCustomer Faced The Following Challenges:Dependent upon machine uptime.Pressure cylinders within the compactor fail to control compression and speed causing problems in binding the coil.Equipment failure occurs in the final stage of production causing the entire line to stop, can you say bottleneck?Critical asset unequipped with sensors to produce data.