Download PDF
Renault Nissan Mitsubishi Alliance Accelerates Chassis Development with Altair SimSolid
Technology Category
- Analytics & Modeling - Digital Twin / Simulation
Applicable Industries
- Automotive
- Equipment & Machinery
Applicable Functions
- Product Research & Development
- Quality Assurance
Use Cases
- Manufacturing Process Simulation
- Time Sensitive Networking
The Challenge
Renault Nissan Mitsubishi Alliance, a strategic partnership between Renault, Nissan, and Mitsubishi Motors, was facing a significant challenge in reducing the weight of their vehicles to stay competitive in the automotive industry. The company aimed to decrease the mass on chassis components by combining new, lighter material Alu with topology optimization. However, the traditional simulation methods such as finite element analysis, while helpful in developing lighter and affordable cars, were time-consuming. The company needed a new, easy-to-use simulation tool that would enable non-experts, part-time analysts, and designers to gain insights and accurate results in the early design phases of Renault vehicles chassis projects and projects for production line tooling/conveyors. The challenge was to find a solution that could reduce the lead time on the development of its products, aligning with the corporate initiative “FAST” (Future-Ready At-Scale Transformation).
About The Customer
Renault Nissan Mitsubishi Alliance is a strategic partnership between the automobile manufacturers Renault, Nissan, and Mitsubishi Motors. The alliance has 122 manufacturing plants worldwide with nearly 450,000 employees controlling ten major brands: Renault, Nissan, Mitsubishi, Infiniti, Renault Samsung, Dacia, Alpine, Datsun, Venucia, and Lada. The ambition of the alliance is to offer autonomous drive, connectivity features, and services on a wide range of affordable vehicles. The Renault Chassis Le Mans plant, which is building car-to-ground connecting components for the Renault Group and for the Alliance, houses the CTC Chassis Technical Center, a CAD engineering center where 350 engineers and technicians focus on testing and validation.
The Solution
The Renault Chassis department, which had been working with Altair’s solutions since 2010, decided to use Altair SimSolid. This solution does not require any expertise in analysis, allowing users to work with the raw CAD data and perform structural analyses on fully featured CAD assemblies within minutes. It eliminates the time-consuming, expertise-extensive, and error-prone tasks of geometry preparation and meshing performed in a conventional structural simulation. The CTC team started an evaluation project for the Chassis activities to find out how this simulation tool for structural analysis could be implemented in the Renault design process. The goal was to provide their designers with a software tool which enables them to design quickly in total autonomy based on their calculations results.
Operational Impact
Quantitative Benefit
Related Case Studies.
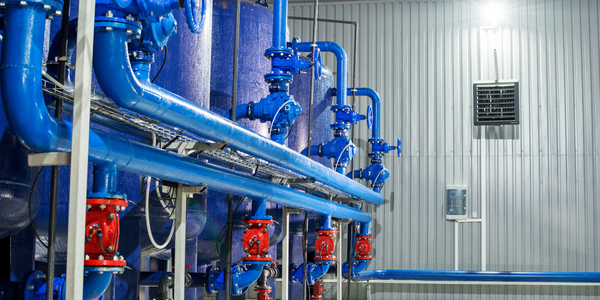
Case Study
Smart Water Filtration Systems
Before working with Ayla Networks, Ozner was already using cloud connectivity to identify and solve water-filtration system malfunctions as well as to monitor filter cartridges for replacements.But, in June 2015, Ozner executives talked with Ayla about how the company might further improve its water systems with IoT technology. They liked what they heard from Ayla, but the executives needed to be sure that Ayla’s Agile IoT Platform provided the security and reliability Ozner required.
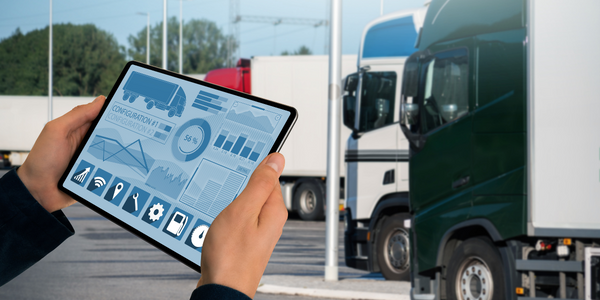
Case Study
IoT enabled Fleet Management with MindSphere
In view of growing competition, Gämmerler had a strong need to remain competitive via process optimization, reliability and gentle handling of printed products, even at highest press speeds. In addition, a digitalization initiative also included developing a key differentiation via data-driven services offers.
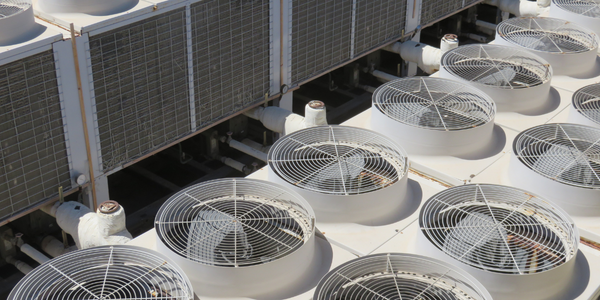
Case Study
Predictive Maintenance for Industrial Chillers
For global leaders in the industrial chiller manufacturing, reliability of the entire production process is of the utmost importance. Chillers are refrigeration systems that produce ice water to provide cooling for a process or industrial application. One of those leaders sought a way to respond to asset performance issues, even before they occur. The intelligence to guarantee maximum reliability of cooling devices is embedded (pre-alarming). A pre-alarming phase means that the cooling device still works, but symptoms may appear, telling manufacturers that a failure is likely to occur in the near future. Chillers who are not internet connected at that moment, provide little insight in this pre-alarming phase.
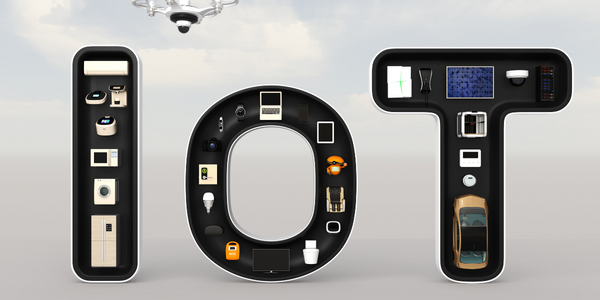
Case Study
Premium Appliance Producer Innovates with Internet of Everything
Sub-Zero faced the largest product launch in the company’s history:It wanted to launch 60 new products as scheduled while simultaneously opening a new “greenfield” production facility, yet still adhering to stringent quality requirements and manage issues from new supply-chain partners. A the same time, it wanted to increase staff productivity time and collaboration while reducing travel and costs.
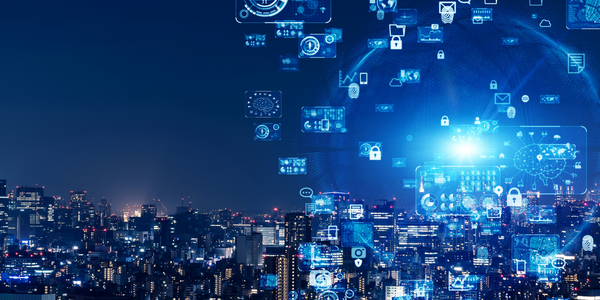
Case Study
Integration of PLC with IoT for Bosch Rexroth
The application arises from the need to monitor and anticipate the problems of one or more machines managed by a PLC. These problems, often resulting from the accumulation over time of small discrepancies, require, when they occur, ex post technical operations maintenance.
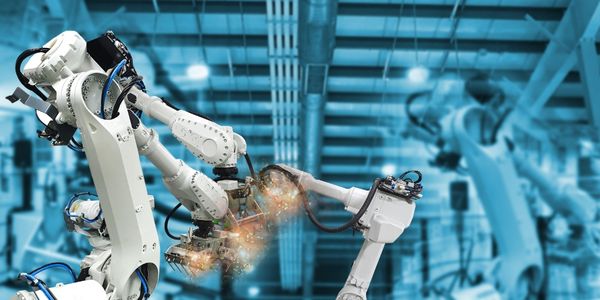
Case Study
Robot Saves Money and Time for US Custom Molding Company
Injection Technology (Itech) is a custom molder for a variety of clients that require precision plastic parts for such products as electric meter covers, dental appliance cases and spools. With 95 employees operating 23 molding machines in a 30,000 square foot plant, Itech wanted to reduce man hours and increase efficiency.