Download PDF
Revamping Conveyor/Separator System Design with Solidworks
Technology Category
- Functional Applications - Product Lifecycle Management Systems (PLM)
- Functional Applications - Computerized Maintenance Management Systems (CMMS)
Applicable Industries
- Automotive
- Packaging
Applicable Functions
- Product Research & Development
- Quality Assurance
- Business Operation
Use Cases
- Predictive Maintenance
- Digital Twin
Services
- Software Design & Engineering Services
- System Integration
- Training
The Challenge
Resolve design data compatibility issues and improve teamwork during the development of components and assemblies for custom-designed conveyor and separator systems to shorten design cycles and satisfy customer demand for shorter lead-times.
About The Customer
Crizaf is a leading developer and manufacturer of custom-engineered conveyor belts, separators, filling and storage systems, and weighing and counting systems. Founded in Italy in 1954, the company has grown to become a multinational organization with production sites in Italy, the United States, Brazil, and India; distributors in 30 countries; and a worldwide sales force. Crizaf products are used in a range of fields, including the automotive, container, cosmetics, electric, electronic, food, household appliance, medical/pharmaceutical, packaging, and recycling industries.
The Solution
Crizaf implemented SOLIDWORKS Standard and SOLIDWORKS Professional design software to resolve their issues. The company standardized on SOLIDWORKS in 2015 because the solution is easy to use, facilitates design changes, and encourages collaborative teamwork. Since implementing SOLIDWORKS, Crizaf has improved its ability to leverage AutoCAD 2D data for new projects and has enjoyed greater flexibility and stability when making design changes. The move to SOLIDWORKS has allowed Crizaf to reduce design cycles and shorten time-to-market for its custom-engineered systems by 15 to 20 percent.
Operational Impact
Quantitative Benefit
Related Case Studies.
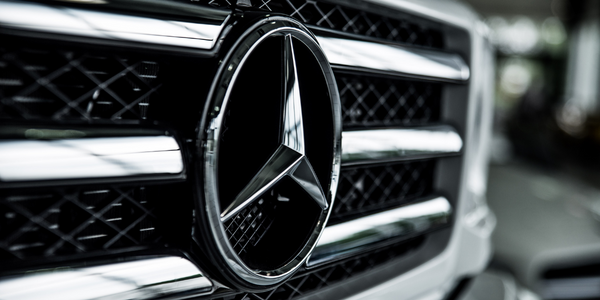
Case Study
Integral Plant Maintenance
Mercedes-Benz and his partner GAZ chose Siemens to be its maintenance partner at a new engine plant in Yaroslavl, Russia. The new plant offers a capacity to manufacture diesel engines for the Russian market, for locally produced Sprinter Classic. In addition to engines for the local market, the Yaroslavl plant will also produce spare parts. Mercedes-Benz Russia and his partner needed a service partner in order to ensure the operation of these lines in a maintenance partnership arrangement. The challenges included coordinating the entire maintenance management operation, in particular inspections, corrective and predictive maintenance activities, and the optimizing spare parts management. Siemens developed a customized maintenance solution that includes all electronic and mechanical maintenance activities (Integral Plant Maintenance).
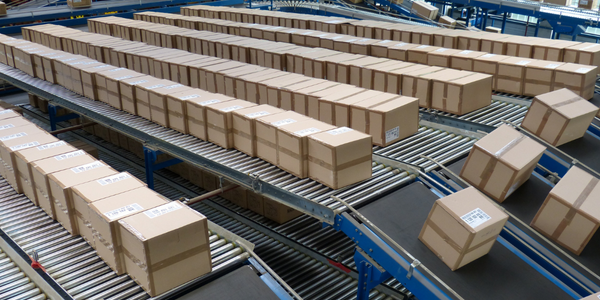
Case Study
IoT Data Analytics Case Study - Packaging Films Manufacturer
The company manufactures packaging films on made to order or configure to order basis. Every order has a different set of requirements from the product characteristics perspective and hence requires machine’s settings to be adjusted accordingly. If the film quality does not meet the required standards, the degraded quality impacts customer delivery causes customer dissatisfaction and results in lower margins. The biggest challenge was to identify the real root cause and devise a remedy for that.
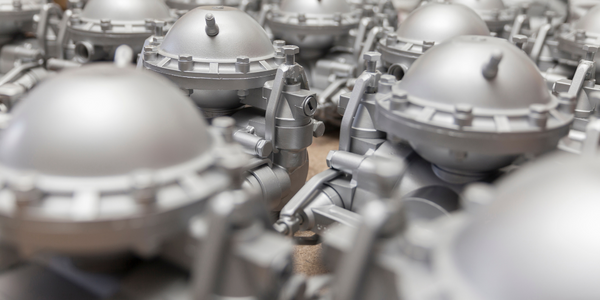
Case Study
Monitoring of Pressure Pumps in Automotive Industry
A large German/American producer of auto parts uses high-pressure pumps to deburr machined parts as a part of its production and quality check process. They decided to monitor these pumps to make sure they work properly and that they can see any indications leading to a potential failure before it affects their process.