Download PDF
Revolutionizing Airline Seat Testing with IoT: A Case Study on Sicma Aero Seat SA
Technology Category
- Analytics & Modeling - Digital Twin / Simulation
- Infrastructure as a Service (IaaS) - Virtual Private Cloud
Applicable Industries
- Cities & Municipalities
- Electronics
Applicable Functions
- Maintenance
- Product Research & Development
Use Cases
- Manufacturing Process Simulation
- Virtual Prototyping & Product Testing
Services
- Testing & Certification
The Challenge
Sicma Aero Seat SA, a French manufacturer of airline passenger seats, faced a significant challenge in the design, manufacturing, and maintenance of its products. The company's seats, which range from simple to sophisticated models with complex electrical and electronic features, had to comply with stringent safety regulations. These regulations required the seats to withstand a crash impact 16 times the force of gravity, translating into tougher design and manufacturing constraints. Additionally, the seats had to appeal to passengers and adhere to various certification and safety regulations, including those related to crash impact. The company also had to meet customer specifications and use a combination of virtual and physical testing to meet appropriate regulations. The challenge was to improve their seating products, cut certification costs, and reduce product development and delivery cycles.
About The Customer
Sicma Aero Seat SA is a subsidiary of Zodiac SA, a French company that has been in business since 1909. The company is headquartered in France with operations in Germany, Brazil, Dubai, Hong Kong, and the United States. Sicma is renowned for the manufacture of airline passenger seats, convertible passenger seats, passenger seats for low-cost companies, crew and pilot seats, and helicopter seats. It counts the world’s premier airlines – as well as Airbus and Boeing – among its customers. The company offers new generations of competitive, 16 g-compliant seats, which require cabin equipment materials to be able to withstand a crash impact 16 times the force of gravity.
The Solution
To address these challenges, Sicma Aero Seat SA increased the amount of virtual testing performed to improve their seating products. The company used Altair HyperWorks, a simulation platform, for their static and dynamic seat analyses. This included using Altair HyperMesh for finite element (FE) meshing activities, HyperView to visualize FE and multi-body systems results, and HyperCrash pre-processing technology for crash and safety modeling tasks. The company also used Altair’s RADIOSS solver for static and dynamic simulation and optimization. This solution allowed Sicma to find the best solution faster when a new seat failed a test, providing a better understanding of the failure phenomena. It also helped avoid lengthy and costly prototyping and physical testing processes to evaluate design alternatives.
Operational Impact
Quantitative Benefit
Related Case Studies.
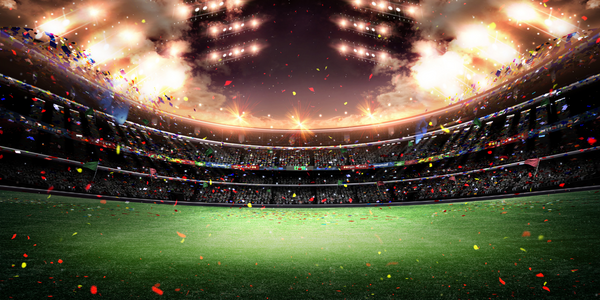
Case Study
Turning A Stadium Into A Smart Building
Honeywell created what it called the “intelligent system” for the National Stadium in Beijing, China, turning the venue for the opening and closing events at the 2008 Summer Olympics into a “smart building.” Designed by highly controversial artist Ai Weiwei, the “Bird’s Nest” remains one of the most impressive feats of stadium architecture in the world. The 250,000 square meter structure housed more than 100,000 athletes and spectators at a time. To accommodate such capacity, China turned to Honeywell’s EBI Integrated Building Management System to create an integrated “intelligent system” for improved building security, safety and energy efficiency.
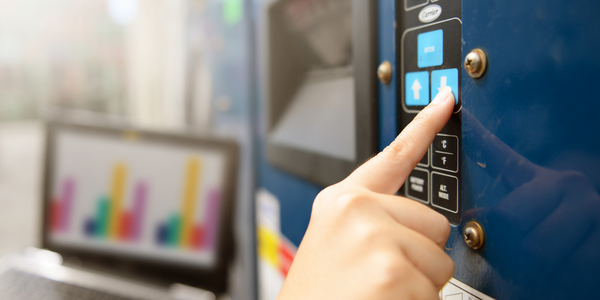
Case Study
Remote Temperature Monitoring of Perishable Goods Saves Money
RMONI was facing temperature monitoring challenges in a cold chain business. A cold chain must be established and maintained to ensure goods have been properly refrigerated during every step of the process, making temperature monitoring a critical business function. Manual registration practice can be very costly, labor intensive and prone to mistakes.
.png)
Case Study
Smart Street Light Network (Copenhagen)
Key stakeholders are taking a comprehensive approach to rethinking smart city innovation. City leaders have collaborated through partnerships involving government, research institutions and solution providers. The Copenhagen Solutions Lab is one of the leading organizations at the forefront of this movement. By bringing together manufacturers with municipal buyers, the Copenhagen Solutions Lab has catalyzed the development and deployment of next-generation smart city innovations. Copenhagen is leveraging this unique approach to accelerate the implementation of smart city solutions. One of the primary focus areas is LED street lighting.
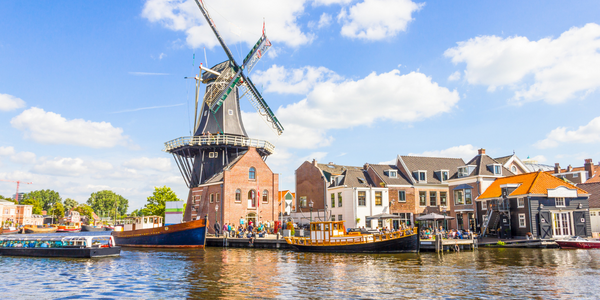
Case Study
Buoy Status Monitoring with LoRa
The Netherlands are well-known for their inland waterways, canals, sluices and of course port activities. The Dutch Ministry of Infrastructure indicates that there are thousands of buoys and fixed items in and near water environments that would profit from IoT monitoring. One of the problems with buoys for example, is that they get hit by ships and the anchor cable breaks. Without connectivity, it takes quite some time to find out that something has happened with that buoy. Not to mention the costs of renting a boat to go to the buoy to fix it. Another important issue, is that there is no real-time monitoring of the buoys at this moment. Only by physically visiting the object on the water, one gains insight in its status.