Download PDF
Safety and Productivity Solutions: Intimo Lingerie Speeds Up Deliveries with Honeywell Hands Free Solution
Technology Category
- Functional Applications - Remote Monitoring & Control Systems
- Functional Applications - Warehouse Management Systems (WMS)
- Networks & Connectivity - Bluetooth
Applicable Industries
- Consumer Goods
- Retail
Applicable Functions
- Logistics & Transportation
- Warehouse & Inventory Management
Use Cases
- Inventory Management
- Supply Chain Visibility
- Warehouse Automation
Services
- System Integration
- Training
The Challenge
Although Intimo as a business has rapidly grown its operations over recent years, the actual product picking processes within its distribution centre still relied on inefficient paper-based systems that were open to errors and were labor-intensive and time-consuming. Recognising the need to operate an efficient supply chain and the importance of accuracy in its direct to home product delivery processes, Intimo recently turned to VoiceID to discuss the use of Honeywell solutions for their picking process.\n\nThe Needs\n• Technology that enhances stock management process and increases warehouse efficiency.\n• Upgrade the current manual system of warehouse management to a more powerful automated solution that delivers more accuracy and reliability.\n• A fast, easy-to-use, and scalable solution that grows with the changing needs of the facility.
About The Customer
Established in 1995, Intimo has built an enviable reputation as one of the leading lingerie brands across Australia and New Zealand. Today, Intimo is known for reflecting the modern woman’s aspiration for quality, style, and function. To supply its wide range of customers across Australia and New Zealand with quality, supportive and wearable lingerie, Intimo operates a streamlined direct-to-customer distribution model out of a centralised distribution centre in Port Melbourne.
The Solution
To demonstrate the benefits of using Honeywell for picking in a real-world scenario for Intimo, VoiceID implemented a Proof of Concept (POC) process. VoiceID’s POC method has been developed to allow companies with little investment, to have a demonstrable look at how the voice process would improve their business,” said Paul Phillips, Senior Business Consultant at VoiceID.\n\nFor Intimo, the entire VoiceID POC process took four hours to complete and involved two different employees being trained and filmed completing hands-free and paper picks for review. The POC process highlighted a potential productivity increase by 50 percent over the existing process. As a result, Intimo elected to proceed with a voice deployment paired with hands-free scanning.\n\nTo enhance its stock management processes and increase warehouse efficiency, Intimo implemented an advanced order picking and distribution system. Under it, the Manhattan Associates SCALE WMS first records the orders and then batches them for picking. Orders are picked using the Honeywell A710 Talkman, SRX2 Headset, and 8670 Bluetooth Ring Scanner. Receipts, putaways, replenishments, and stock management are all handled by the Honeywell CK3X rugged hand-held computer.
Operational Impact
Quantitative Benefit
Related Case Studies.
.png)
Case Study
Improving Vending Machine Profitability with the Internet of Things (IoT)
The vending industry is undergoing a sea change, taking advantage of new technologies to go beyond just delivering snacks to creating a new retail location. Intelligent vending machines can be found in many public locations as well as company facilities, selling different types of goods and services, including even computer accessories, gold bars, tickets, and office supplies. With increasing sophistication, they may also provide time- and location-based data pertaining to sales, inventory, and customer preferences. But at the end of the day, vending machine operators know greater profitability is driven by higher sales and lower operating costs.
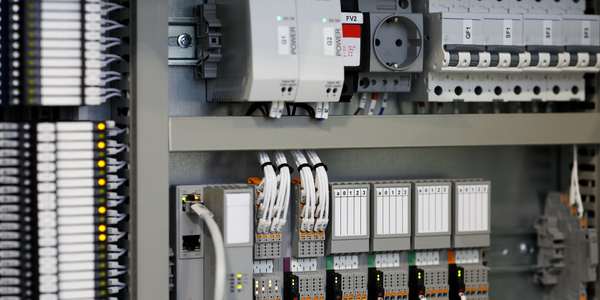
Case Study
Improving Production Line Efficiency with Ethernet Micro RTU Controller
Moxa was asked to provide a connectivity solution for one of the world's leading cosmetics companies. This multinational corporation, with retail presence in 130 countries, 23 global braches, and over 66,000 employees, sought to improve the efficiency of their production process by migrating from manual monitoring to an automatic productivity monitoring system. The production line was being monitored by ABB Real-TPI, a factory information system that offers data collection and analysis to improve plant efficiency. Due to software limitations, the customer needed an OPC server and a corresponding I/O solution to collect data from additional sensor devices for the Real-TPI system. The goal is to enable the factory information system to more thoroughly collect data from every corner of the production line. This will improve its ability to measure Overall Equipment Effectiveness (OEE) and translate into increased production efficiencies. System Requirements • Instant status updates while still consuming minimal bandwidth to relieve strain on limited factory networks • Interoperable with ABB Real-TPI • Small form factor appropriate for deployment where space is scarce • Remote software management and configuration to simplify operations
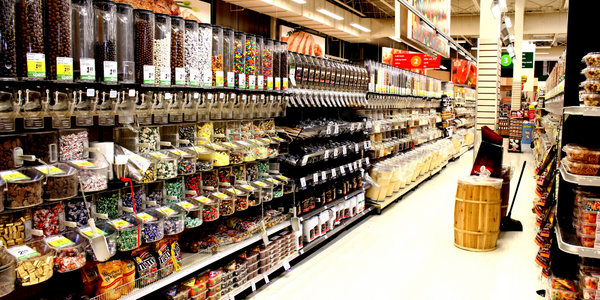
Case Study
How Sirqul’s IoT Platform is Crafting Carrefour’s New In-Store Experiences
Carrefour Taiwan’s goal is to be completely digital by end of 2018. Out-dated manual methods for analysis and assumptions limited Carrefour’s ability to change the customer experience and were void of real-time decision-making capabilities. Rather than relying solely on sales data, assumptions, and disparate systems, Carrefour Taiwan’s CEO led an initiative to find a connected IoT solution that could give the team the ability to make real-time changes and more informed decisions. Prior to implementing, Carrefour struggled to address their conversion rates and did not have the proper insights into the customer decision-making process nor how to make an immediate impact without losing customer confidence.
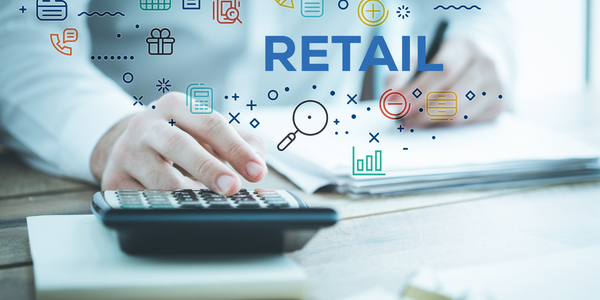
Case Study
Digital Retail Security Solutions
Sennco wanted to help its retail customers increase sales and profits by developing an innovative alarm system as opposed to conventional connected alarms that are permanently tethered to display products. These traditional security systems were cumbersome and intrusive to the customer shopping experience. Additionally, they provided no useful data or analytics.