Download PDF
Saudi Aramco Increases Capacity by 100,000 barrels/day and Upgrades Bottom of the Barrel Products
Technology Category
- Analytics & Modeling - Process Analytics
- Application Infrastructure & Middleware - Data Exchange & Integration
Applicable Industries
- Oil & Gas
Applicable Functions
- Process Manufacturing
Use Cases
- Predictive Maintenance
- Process Control & Optimization
Services
- Software Design & Engineering Services
The Challenge
Saudi Aramco, the state-owned oil company of the Kingdom of Saudi Arabia, was facing a challenge with one of its semi-conversion refineries. The refinery was producing excessive fuel oil, which was limiting the facility’s margin to a level lower than comparably sized refineries. The company decided to revamp the refinery to upgrade the bottom of the barrel products to create more value and improve the refinery’s profit margins. The refinery was also considering changing the crude oil it was processing. The revamp plan included adding new units and modifying existing ones.
About The Customer
Saudi Aramco is the state-owned oil company of the Kingdom of Saudi Arabia. Founded in 1933, the company focuses on hydrocarbons exploration, production, refining, distribution, shipping and marketing crude oil to customers worldwide. Saudi Aramco has a refining capacity of 5.4 million barrels per day from their operations around the globe. One of the company's semi-conversion refineries was producing excessive fuel oil, limiting the facility’s margin to a level lower than comparably sized refineries. To address this, Saudi Aramco decided to revamp the refinery to upgrade the bottom of the barrel products to create more value and improve the refinery’s profit margins.
The Solution
Saudi Aramco chose residue hydrocracker technology to upgrade heavy oil to high-value products and increase diesel production. The company used Aspen HYSYS to analyze the feasibility of the refinery reconfiguration plans by rigorously simulating operations of the hydrocracker, crude distillation unit (CDU), vacuum distillation unit (VDU) and other units. The software helped the team to debottleneck and suggest modifications for critical existing units such as the CDU and the VDU to perform in new operating conditions. Aspen HYSYS Petroleum Refining enabled development of a rigorous model of the new reactor unit, which generated data required for the respective reactor sub model in Aspen PIMS.
Operational Impact
Quantitative Benefit
Related Case Studies.
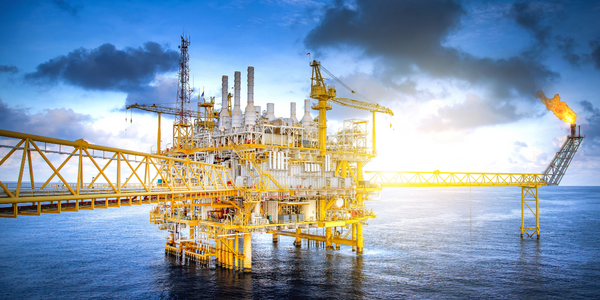
Case Study
Taking Oil and Gas Exploration to the Next Level
DownUnder GeoSolutions (DUG) wanted to increase computing performance by 5 to 10 times to improve seismic processing. The solution must build on current architecture software investments without sacrificing existing software and scale computing without scaling IT infrastructure costs.
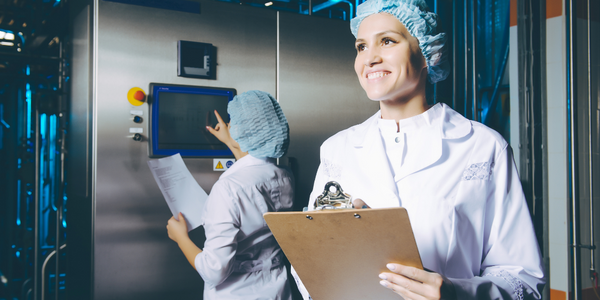
Case Study
Remote Wellhead Monitoring
Each wellhead was equipped with various sensors and meters that needed to be monitored and controlled from a central HMI, often miles away from the assets in the field. Redundant solar and wind generators were installed at each wellhead to support the electrical needs of the pumpstations, temperature meters, cameras, and cellular modules. In addition to asset management and remote control capabilities, data logging for remote surveillance and alarm notifications was a key demand from the customer. Terra Ferma’s solution needed to be power efficient, reliable, and capable of supporting high-bandwidth data-feeds. They needed a multi-link cellular connection to a central server that sustained reliable and redundant monitoring and control of flow meters, temperature sensors, power supply, and event-logging; including video and image files. This open-standard network needed to interface with the existing SCADA and proprietary network management software.
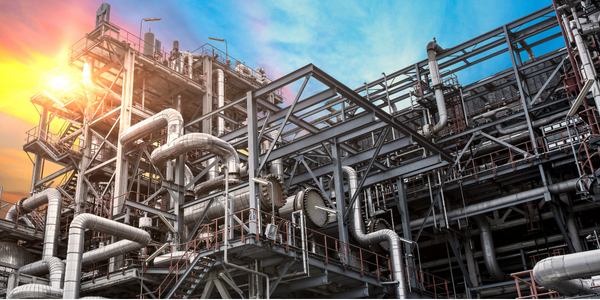
Case Study
Refinery Saves Over $700,000 with Smart Wireless
One of the largest petroleum refineries in the world is equipped to refine various types of crude oil and manufacture various grades of fuel from motor gasoline to Aviation Turbine Fuel. Due to wear and tear, eight hydrogen valves in each refinery were leaking, and each cost $1800 per ton of hydrogen vented. The plant also had leakage on nearly 30 flare control hydrocarbon valves. The refinery wanted a continuous, online monitoring system that could catch leaks early, minimize hydrogen and hydrocarbon production losses, and improve safety for maintenance.