Download PDF
Scalable and Reliable Engineering Solutions: A Case Study of Zamil Industrial
Technology Category
- Functional Applications - Enterprise Resource Planning Systems (ERP)
- Platform as a Service (PaaS) - Application Development Platforms
Applicable Industries
- Cement
Applicable Functions
- Facility Management
Use Cases
- Process Control & Optimization
- Time Sensitive Networking
Services
- System Integration
- Training
The Challenge
Zamil Industrial, a leading provider of market-leading equipment, construction materials, and innovative design and engineering solutions, was facing a significant challenge with its legacy business process automation platform. The platform was initially sufficient for the company's needs, but as the organization expanded and its requirements grew more complex, the platform failed to provide the necessary scalability and reliability. The IT resources were under constant pressure due to frequent bugs and breakdowns that required immediate attention. The lack of adequate support from the legacy system providers led to increased downtime and business interruption, which became a serious issue for the company. Zamil Industrial was in dire need of a workflow engine that could keep pace with its growing digital technology demands.
About The Customer
Zamil Industrial is a leading provider of market-leading equipment, construction materials, and innovative design and engineering solutions. The company is based in Saudi Arabia and has been experiencing rapid growth. As the company expanded, its needs became more complex, and its legacy systems were no longer sufficient. The company was in need of a comprehensive automation solution that could keep pace with its growing digital technology demands and provide the necessary scalability and reliability.
The Solution
After consulting with its Microsoft partner and shortlisting a range of alternative vendors, Zamil Industrial chose Nintex K2 Five as its enterprise workflow solution. The majority of the group’s business processes were moved to Nintex K2 Five, serving critical business areas including Personnel, HR, Training, Finance, Quality Control, Facility Management, and Manufacturing. In 2015, more than 97,000 requests were initiated through Nintex K2 Five, and a further 81,000 in 2016. Nintex K2 Five provided an agile business process automation platform that could scale to meet business demand. It also increased efficiencies within the IT department by significantly reducing the time taken to build and deploy a process application. The effort required to support all users across the group was also drastically reduced by 80%.
Operational Impact
Quantitative Benefit
Related Case Studies.
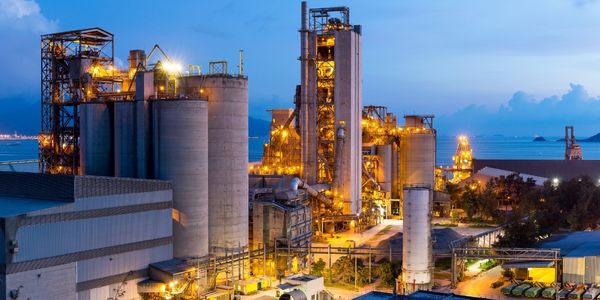
Case Study
System 800xA at Indian Cement Plants
Chettinad Cement recognized that further efficiencies could be achieved in its cement manufacturing process. It looked to investing in comprehensive operational and control technologies to manage and derive productivity and energy efficiency gains from the assets on Line 2, their second plant in India.
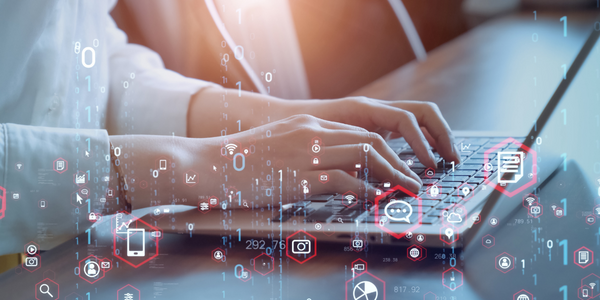
Case Study
Digital Transformation of Atlanta Grout & Tile: An IoT Case Study
Atlanta Grout & Tile, a Tile, Stone & Grout restoration company based in Woodstock, Georgia, was facing challenges with its traditional business model. Despite steady growth over the years, the company was falling behind the web revolution and missing out on the opportunity to tap into a new consumer base. They were using independent software from different vendors for each of their department information and workforce management. This resulted in a lot of manual work on excel and the need to export/import data between different systems. This not only increased overhead costs but also slowed down their response to clients. The company also had to prepare numerous reports manually and lacked access to customer trends for effective business decision-making.
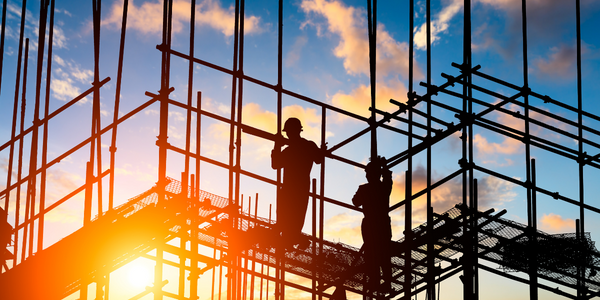
Case Study
Revolutionizing Construction Equipment Rental: A Case Study on ProsRent and ENO8
ProsRent, a startup that won the 'Best Financial Opportunity' and 'Best Pitch' at CodeLaunch 2016, aimed to revolutionize the way construction professionals source and rent heavy equipment. In the construction industry, project managers and contractors typically rent heavy equipment from supply companies. However, predicting inventory can be challenging, and finding the required equipment at the right time and place can be a hassle. If the preferred vendor doesn't have the required equipment, it results in wasted time and money in searching for it, often leading to higher costs due to non-preferred rates and increased delivery costs if the vendor is located far from the job site. Suppliers, on the other hand, desired access to a wider base of trusted renters that they didn't have to vet themselves and wanted to offer dynamic rental pricing based on demand and availability in their market. ProsRent's challenge was to produce a minimum viable product that was fast and first to market but also strong enough to engender loyalty and repeat business from the target market.
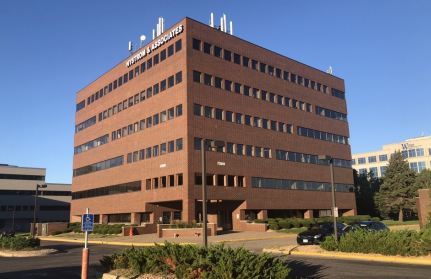
Case Study
IoT Solution Enhances Comfort and Energy Efficiency at Apple Valley Commons Office
Apple Valley Commons, a mixed-use office complex built in 1986, was facing significant comfort and energy efficiency challenges. The building, which houses a variety of businesses, was experiencing extreme temperature imbalances, causing discomfort to employees and clients. Despite outdoor temperatures being consistently high during summers, occupants had to use space heaters to keep warm. The electricity bills from the constant operation of the heat pump were exorbitant. The building's elevator room on the roof was also overheating, reaching temperatures of 130 to 140 degrees, causing the elevator equipment to shut down. The building's existing controls solution did not provide a front end for diagnostics or remote control. The building management was seeking a solution that could address these temperature issues, improve occupant comfort, reduce operational costs, and increase building visibility.
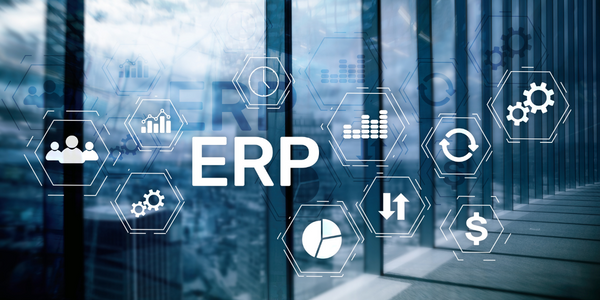
Case Study
Revamping EE's Legacy ERP: A Case Study on BT's Strategic Transformation
EE, even after its merger with BT, was operating its ERP estate on legacy infrastructure, hosted on the premises of a third-party supplier. This outdated system resulted in a volume-based operational model, higher time to market, longer delivery cycles, and unsatisfactory customer experience. BT recognized the need for a strategic transformation of these aging ERP systems and sought a partner who could proactively manage application services. The partner was also expected to handle development requirements associated with application management services, drive accountability, and ownership with a time and target-driven transformation of these services. BT's primary goals were to improve customer experience, reduce cycle time, and measure these improvements with precision.